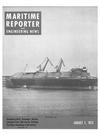
Page 11: of Maritime Reporter Magazine (August 1973)
Read this page in Pdf, Flash or Html5 edition of August 1973 Maritime Reporter Magazine
Columns, temporary support Ring, temporary
TANK ASSEMBLY sketch shows the seven separate tank sections and method of erection.
The Norman Lady— (Continued from page 11) cent nickel steel. For the forged ma- terial, Charpy V-notch impact tests are performed on short transverse specimens oriented with the fracture surface parallel to the longitudinal direction of the forging. Similarly, tensile, yield and elongation minima are checked in both the short and long transverse directions.
Production of the 101-foot 7-inch and the 108-foot 3-inch tanks of 9 percent nickel steel for the Norman
Lady was as follows: The steel was received in the shipyard already shaped and cut to size with the edges beveled, ready for cleaning, fit up, and welding. Each dished plate was inspected for shape (sphericity) and for edge dimension and bevel, and is checked against a master prior to shipment from the mill.
In the Rosenberg yard, the cargo tanks are erected in the hull using large subassemblies with the hull in- ner bottom forming the erection plat- form. In other shipyards, the tank- erection procedures and production sequences are varied to suit the yard conditions. Some of the following considerations need to be integrated in any attempt to optimize the tank building: 1. Hull and tank building time spans. 2. Weld procedures useable, auto- matic versus manual. 3. Capital expense and availabil- ity of welding shops, tank welding jigs, and segment positioning and transporting rigs. 4. Lifting capacity. 5. Space limitations. 6. Availability and skills of labor.
All other things being equal, the shipbuilder feels that there is an ad- signed for carrying LNG at atmos- pheric pressure. The lowest allowable temperature is minus 260° F.
The propulsion plant consists of a single Kvaerner-General Electric steam turbine with a maximum con- tinuous rating of 30,000 bhp at 95 rpm. Steam is supplied by two Moss-
Foster Wheeler boilers, suitable for burning methane and heavy fuel. The trial speed has been set at about 19.7 knots, fully loaded, and at maximum continuous rating.
The maximum discharge rate is about 12 hours by means of sub- merged pumps, one in each tank. Car- go-tank insulation is designed to give a maximum boil-rate less than 0.25 percent per 24 hours.
The Norman Lady is classed by
Det norske Veritas for Tee C and as an BO, Tanker for Liquefied
Gas. It also complies with the U.S.
Coast Guard's rules and regulations for foreign-flag vessels.
Moss Rosenberg Licensees
The Moss Rosenberg LNG design has become an international concept.
Seven foreign shipyards have been licensed to build LNG carriers accord- ing to this design. These are:
Kawasaki Heavy Industries Ltd. of Japan,
Mitsui Shipbuilding and Engineer- ing Co., Ltd. of Japan,
Mitsubishi Heavy Industries Ltd. of Japan,
General Dynamics Corp. Quincy
Shipbuilding Division of U.S.A.,
Howaldtswerke Deutsche Werft
A.G. of West Germany,
Italcantiere, S.p.A. of Italy, and
Astilleros Espanoles S.A. of Spain.
R.S. Kvamsdal, manager, Devel- opment & License Department,
Moss Rosenberg Verft, and J.L.
Howard, president, Kvaerner Moss,
Inc., New York, listed the advan- tages of their LNG system in a re- cent paper as: (1) low cost and high safety, and (2) low 'mainte- nance costs. They feel, that due to the extensive analytical studies and experiments, that the first ships to enter service in 1973 will have any source 'for trouble reduced to minimum.
The Norman Lady
The Norman Lady, Hull 196, has an overall length of 816 feet 7 inch- es, a length between perpendiculars of 777 feet 7 inches, a molded breadth of 131 feet 2 inches, a molded depth of 75 feet 3 J^ inches and a maximum draft with a cargo density of 0.5 tons per cubic meter of 34 feet 3^2 inches.
The ship has five insulated, inde- pendent spherical tanks and is de-
TANK SHELL sketch showing the skirt sup- port for the entire tank, fastened at the equator.
Model of the 87,600-cubic-meter ship with cutaway in the cargo tank area. Built of 9 percent nickel steel, each of two of the tanks have a diameter of 101 feet 7 inches, and the other three have diameters of 108 feet 3 inches. vantage to build the tanks independ- ent of the hull fabrication. Construc- tion outside the ship has the advantage of being more amenable to automated and rationalized procedures and, at the same time, may reduce the build- ing dock time span. Since the hull can be virtually completed and can be moved under its own power before the cargo tanks are installed, the in- dependent tank building can even be performed at a location remote from the shipyard.
August 1, 1973 13