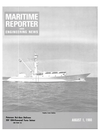
Page 40: of Maritime Reporter Magazine (August 1980)
Read this page in Pdf, Flash or Html5 edition of August 1980 Maritime Reporter Magazine
Will Ships Use An Abundant Fuel In The 1980s?
Coal-Fired Marine Boilers
A Coal-Fired Marine Steam Plant Can Be Offered Today
Which Will Provide The Same High Traditional Reliability.
Carl F. Horlitz Jr. and Steven E. Sabo*
The origin of the steam boiler can be directly related to the in- vention of the steam engine, and its development has been a vital element in the successful gener- ation of power by steam.
The earliest types of marine boilers consisted of large pressure vessels filled with water with external furnaces located under- neath and were fired with solid fuels; initially wood and then coal.
Eventually the well-known Scotch marine boiler evolved and was readily accepted by marine en- gineers.
As the demand for larger and faster vessels grew, power de- mands also increased. At the end of the nineteenth century, the development of the steam turbine by Sir Charles Parsons prompted even further demands on the boil- er designer. Improved materials led to increased capacities, pres- sures, and temperatures. Stiff commercial as well as naval com- petition urged the development of newer boiler designs. Various types of water-tube boilers were initially adopted because of their ability to fit into restricted spaces.
Oil firing of marine boilers be- gan to appear around the turn of the century. Although not readily accepted initially, the advantages of firing oil gradually became more apparent and it eventually became the standard for most vessels. Oil not only proved more convenient to handle, store, bunk- er, and burn; but it also proved more convenient from a man- power utilization standpoint. By the end of World War II, coal firing was essentially phased out of most vessels. One area of ex- ception was the Great Lakes. Be- cause of the longevity of these vessels, their somewhat limited trade routes, and their easy ac- cess to coal, many of these ves- sels continued to operate on coal.
During the 1960s and early 1970s, there was a great demand for increased speed. Fuel oil was relatively inexpensive and readily available. Larger and faster mer- chant vessels were constructed, and more advanced plants utiliz- ing higher temperatures and pres- sures were adopted.
In 1973, the Arab oil embargo created conditions which required a complete re-evaluation of vessel operation and design. Throughout the remainder of the 1970s, the price of crude oil continued to rise at unprecedented rates. Also dur- ing the latter part of the 1970s, political unrest in the Middle East made the availability of crude oil uncertain.
Concern over meeting energy demands became paramount. Both government and industry began to investigate alternate energy sources and their possible appli- cation to particular energy de- mands. Although there appear to be many alternate energy sources which can assist in solving this problem in the future, such as synfuels, solar power, fusion, etc., these will be of little assistance to the marine operator in the near future.
One alternate fuel that is read- ily available, and is suitable for marine applications, particularly in light of the economic and po- litical factors which are currently affecting oil, is coal.
Therefore, in evaluating any powerplant for a vessel today, an operator must consider the future availability of his fuel source, its quality, and the effect its price might have on the operation of the vessel. In such an evaluation, the economics for certain types of vessels appear to justify con- sidering coal-fired steam plants.
Methods Of Coal Firing
Three methods of coal firing are presently available to the marine boiler designer for his consideration: pulverized firing, fluidized bed combustion and stok- er firing. The use of coal-oil slur- ries may be considered as a fourth alternate, however, this method of firing requires many of the ancillary components indigenous to the coal-fired plants such as ash handling equipment, coal pul- verizers and stack-gas cleanup equipment, as well as a rather large furnace. Due to the large quantity of oil (50 percent to 60 percent) required in the slurry, the same economics associated with full coal firing cannot be realized. This method of firing is currently in use to a small extent in the utility and industrial sec- tion as a retrofit for plants orig- inally designed to fire oil. The capacity of these plants retro- fitted for slurry firing would be approximately 40 percent less than with oil firing.
Pulverized firing involves the suspension firing of coal which has been reduced in size by a bowl mill or other form of coal pulverizer to a powder consist- ency. This method of firing is a virtual necessity for plants de- signed to produce more than 300,- 000 pounds of steam per hour, since a stoker for this application would be impractical due to its large size. The pulverized sys- tem requires a significantly great- er volume for a given machinery installation due to additional fuel preparation and transport equip- ment as well as a 20 percent larger furnace volume than for stoker firing.
Fluidized bed combustion, wherein fuel is introduced into an aerated bed of limestone, sand or suitable material and burned at temperatures usually in the range of 1,600°F, may ultimately have application in the marine sector. The principal advantage would be its somewhat compact (continued on page 44) •Mr. Horlitz and Mr. Sabo, C-E Marine
Power Systems, Combustion Engineer- ing, Inc., Windsor, Conn., presented the paper abstracted here before a recent meeting of the Great Lakes and Great Rivers Section of The So- ciety of Naval Architects and Marine
Engineers.
COAL
OIL 1.25 W 1.25 D 1.10 W 1.20 D »
GAS 1.60 H 1.20 H
Figure 1 — Comparison of furnace sizes for coal, oil and gas-fired boilers. 42 Maritime Reporter/Engineering News