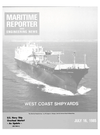
Page 13: of Maritime Reporter Magazine (July 15, 1985)
Read this page in Pdf, Flash or Html5 edition of July 15, 1985 Maritime Reporter Magazine
to complete the work on a very tight schedule.
Another recent major retrofit was the Cable & Wireless cable ship
Cable Enterprise. The last of a four- frigate refit contract for the Canadi- an Navy is under way with the dry- docking of HMCS Saskatchewan at the company's Esquimalt yard on
Victoria Island, following comple- tion of the HMCS Yukon in January this year.
DILLINGHAM
Circle 12 on Reader Service Card
During the past 12 months, Dil- lingham Ship Repair in Portland,
Ore., has performed some major re- pair and conversion jobs. Mitsui In- tegrated Propeller Ducts were in- stalled on four 165,000-dwt tank- ers—Brooks Range, Exxon North
Slope, Kenai, and Thompson Pass.
These ducts, each weighing 70 tons with a diameter of 35 feet, were manufactured by Mitsui in Japan and shipped to the Portland yard via containership.
Another noteworthy job was the rebuilding of the rudder stock and rudder of the 225,000-dwt tanker
Bay Ridge. The rudder weighed 180 tons and the stock 150 tons. This was a 17-day job; similar work on two sister ships performed in Rot- terdam and South Africa took 40 and 70 days to accomplish.
A six-month job on the Alaska
State ferry Matanuska involved a complete re-engining of both main engines, reduction gears, shafting, and propellers. The original fixed propellers were replaced with CP units. The job also included refur- bishing of the engine room controls, pumps, piping, and electrical other than the generating sets.
Other jobs included the installa- tion of a Foster Wheeler inert gas generating system on the tanker
Chevron Colorado, and the replace- ment of the main reduction gear on the tanker Exxon North Slope.
Recent upgrading of facilities at
Dillingham included the purchase and installation of two 100-ton chain air hoists manufactured in
West Germany, and the installation of a test rack for valves up to 36- inch. This latter unit cut valve test- ing time from several hours by sev- eral employees to a matter of min- utes.
Other facilities improvements in- clude a new blasting room 12 by 12 by 24 feet, a dehumidification sys- tem for use when blasting tanks, four additional vacuum material re- movers, and a 12- by 40-foot, multi- ple-head, computer-controlled plate burning machine.
Dillingham recently was awarded a $20.5-million contract by the Mar- itime Administration for the con- version of the containership ex-
President Polk into an auxiliary crane ship (TAC-S-3) for assign- ment to the Navy's Ready Reserve
Fleet.
FOSS SHIPYARD
Circle 24 on Reader Service Card
Foss Shipyard in Seattle and Dil- lingham Maritime Services (DMS) recently completed a major conver- sion of the oil barge Foss 255, which is used for supplying Chevron petro- leum products to Alaska's Gulf
Coast and Aleutian Island commu- nities. DMS won the Chevron USA distribution contract, and put the conversion contract out for bid. The
Foss yard won the contract in highly competitive bidding.
Conversion of the Foss 255 was carried out to Chevron specifica- tions, creating an all-weather, year- round floating distributor of Chev- ron products. Replacing the Alaska
Standard, a tanker retired because of age, the converted Foss 255 is a
U.S. Coast Guard Grade A petro- leum vessel, featuring 12 segregated tanks and four separate pumping systems. It will carry three grades of automobile gasoline, two grades of aviation gas, jet fuel, No. 2 disel fuel, home heating oil, drums of lube oil, and cases of gas station type products to more than 15 Alaska communities. The barge is 250 feet long, with a beam of 76 feet and a capacity of more than 40,000 bar- rels. Foss Shipyard completed the conversion on schedule.
GUNDERSON
Circle 14 on Reader Service Card
A group of Oregon investors re- cently purchased FMC Corpora- tion's Marine and Rail Equipment
Division in Portland, bringing cor- porate ownership back to the State, (continued on page 16)
Your Best Source for Repair Parts and More.
Our Repair Parts Facility enables us to meet your repair needs for Jered
Brown Brothers Steering Gear,
Elevators, Deck Machinery, Sewage
Treatment Systems, Plus ... Draw- ings, patterns, tooling and capabil- ity to manufacture to spec; equip- ment built as far back as 1867.
Including: Jered Industries, C.H.
Wheeler, American Engineering, and Baldwin - Lima - Hamilton.
Jered Brown Brothers is also your
American source for:
Brown Brothers - Steering Gear,
Stabilizers
John Hastie- Commercial Steering
Gear, Cranes
Michell Bearings - Oil Lubricated
Bearings
Stone Vickers - Controllable pitch propellers, Thrusters, Azimuthing thrusters, Watertight doors
If you have equipment operating in this hemisphere you can minimize international red tape, and down time. Simply give us the ship name and part or assembly no. We can provide expeditious service to ex- tend the life of your equipment and quickly return it to service.
Call or write for free literature.
Jered Brown Brothers Inc.
A Vickers Marine Engineering Company
USS HARRY W. HILL (DD 986) Ingalls Shipbuilding Photo.
Marine Services Group • 56 S. Squirrel Road • Auburn Hills, Ml 48057 • Phone: (313) 852-5114
Circle 224 on Reader Service Card
Y
July 16, 1985 15