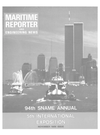
Page 21: of Maritime Reporter Magazine (November 1986)
Read this page in Pdf, Flash or Html5 edition of November 1986 Maritime Reporter Magazine
Principals at LA Metro SNAME meeting included (L to R): Robert Levine. Section chairman;
Paul Cromer, papers chairman; Thomas Junod, author; E.J. Penewell, publicity chairman;
E.V. (Ned) Stewart, past chairman; and Lawrence Levy, secretary.
The first meeting of the 86-87 season for the Los Angeles Metro- politan Section of The Society of
Naval Architects and Marine Engi- neers was held at the princess
Louise II Restaurant in San Pedro.
The author, Thomas R. Junod, marine and offshore manager of
Equipment Engineering Inc. of Cos- ta Mesa, discussed the history of centrifugal cleaning of fuels and lube oils. He said that basic design considerations can greatly enhance the adaptability of these fuel and lube oil cleaning systems. The con- figuration is especially important for service, repair, and modification.
His presentation was followed by discussion of specific application problems by the audience.
PROPULSION
UPDATE
Bird-Johnson Building World's Most
Powerful CP Propellers For DDG-51
In March this year, Bath Iron
Works Corporation awarded to
Bird-Johnson Company of Walpole,
Mass., a contract to supply the con- trollable-pitch main propulsion equipment for the DDG-51, the lead ship of the Arleigh Burke Class of guided-missile destroyers. Delivery of these CP propellers, at 50,000 shp each, will mark a world record CPP power output.
Extensive research and develop- ment enabled Bird-Johnson's engi- neers to develop this CPP system to conform to the unique requirements of the DDG-51, a surface combatant designed to reach speeds in excess of 30 knots. The CP propellers for the
DDG-51 will provide a full range of ahead and astern thrust by changing the propeller pitch without chang- ing the directional rotation of the propulsion machinery. The CPP system will impart a high degree of maneuverability to the ship as well as providing improved power utili- zation, faster acceleration, quicker stopping time, better slow-speed control, and reduced maintenance of engines and gear boxes.
Five major subassemblies will make up the CPP system: the pro- peller blades, hub assembly, oil dis- tribution box, Prairie air emission system, and hydraulic system.
Propeller Blades. Each nickel- aluminum-bronze propeller blade will be finish-machined overall by numerically controlled machining, and skewed in form to minimize vibration and noise. The complete propeller assembly will consist of five such blades and measure 17 feet in diameter.
Hub Assembly. Pitch changes are effected by the hub servomotor, which consists of a crosshead, pis- ton, closed cylinder, piston rod, and main regulating valve. Sliding blocks fit in machined slots in the crosshead, and an eccentrically lo- cated pin on the underside of each crank ring fits in a machined hole in each sliding block. The crank ring, which is a closed die steel forging, fits over and rotates on a centerpost integral to the hub body. This cross- bar and centerpost construction in- sures hub rigidity. Each propeller blade is attached to a crank ring with non-corroding K-Monel blade bolts. A bearing ring retains each crank ring in the hub body. When the piston, crosshead, and piston rod assembly moves axially, the sliding block exerts force on the pin of the crank ring. Axial movement of the piston rod thus causes rota- tion of the crank ring and blade assembly.
All moving parts of the hub work in oil. Blade seals preclude the pos- sible admission of seawater into the hub internals and prevent oil leak- age. The hub body is centrifugally cast of nickel-aluminum-bronze and mounted on the propeller shaft flange with O-ring-sealed bolts.
Dowels transmit all torque between the hub and body shafting and be- tween the blades and crank rings.
Oil Distribution Box. The OD box is mounted on the forward end of the main reduction gear casing. It supplies the passages for pressure oil and return oil, provides a me- chanical pitch indication, and also contains the auxiliary servomotor that actuates the valve rod. The OD box includes provisions for mechan- ically locking the propeller in the full ahead position for safe emergen- cy take-home operation in the un- likely event of failure of the redun- dant hydraulic system.
Prairie System. A rotary seal at the OD box admits air from the ship's air supply to the rotating
Prairie tubing located within the valve rod. Air flows through the tub- ing, enters drilled passages in the hub, and is directed to the base of each blade. Air then passes through a machined channel running along the blade's leading edge from the root to the tip. It is discharged into the water over the blade's surface through holes near the leading edge of the blade. Check valves prevent seawater from entering the system when it is secured.
Hydraulic System. The hy- draulic system is of modular design, employing components selected to meet naval operating, shock, noise, vibration, and safety requirements.
The hydraulic oil power module (factory-assembled to simplify in- stallation) delivers oil to the OD box and thereby to the hub mechanism, with the main pump providing oil flow and pressure under normal operating conditions. The pump discharges oil through filters to the pressure control assembly that regu- lates control oil and pressure oil. A second pump is provided for stand- by operation. Each pump alone pro- vides sufficient oil flow to meet the specified pitch-changing time.
The Bird-Johnson DDG-51 pro- pellers are being designed and man- ufactured for quiet operation. Due to its unidirectional rotation, the CP propeller always maintains the same leading edge, regardless of direction of thrust. The hydrodynamic blade form is never compromised by strength considerations for astern rotation. The result is that highly skewed blades can be used to effec- tively reduce pressure pulses and the resultant noise and vibration.
In addition to the CPP main pro- pulsion system, on-board and shore- based spares have also been con- tracted for the DDG-51. Bird-
Johnson operates a round-the-clock
Parts Department for the prompt processing of all spare parts re- quests. A Service Department is staffed with representatives experi- enced in marine propulsion prod- ucts and with demonstrated profi- ciency in mechanics, hydraulics, and electrical systems. Service represen- tatives undergo intensive training in the design, operation, installation, maintenance, and repair of Bird-
Johnson products to provide su- perior service—anytime and any- where. These representatives are stationed strategically throughout the U.S. to assure timely support of customer requirements.
For further information on Bird-
Johnson's products, service, facili- ties, and capabilities,
Circle 59 on Reader Service Card
Fuel And Lube Oil System Repair
Topic At Los Angeles SNAME Meeting
Propeller Hubs and Blade Assembly
PiSTON/CROSSHEAD
ASSEMBLY FORE & AFT
MOTION TRANSLATION TO
CRANKRING/BLADE ROTARY
MOTION THROUGH SLIDING
BLOCK
November, 1986 103