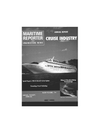
Page 26: of Maritime Reporter Magazine (July 1994)
Read this page in Pdf, Flash or Html5 edition of July 1994 Maritime Reporter Magazine
Ship & Boatbuilding Technology:
Voyager Class Pilot Boat For North Seas (Continued from page 26) eration levels. More importantly, however, came the realization that lightweight construction would have to be employed.
Designs were evolved, specifica- tions written and finally the project was approved in March 1992 — and of two Dutch yards invited to bid,
Engelaer Scheepsbouw, collaborat- ing throughout with naval architect
Alastair Cameron of Camarc Ltd., was awarded the contract. The builder had been impressed with this designer's track record and in particular the innovative and suc- cessful 28-knot, 39.4-ft. (12-m) pilot vessel he had produced for the Scot- tish Port of Dundee some years ear- lier.
Mr. Cameron told Maritime Re- porter that he agreed with the Pilot- age Organization's conclusions and proposed that the yard base its offer on his own double chine hull form which has been proven over 10 years in applications ranging from 23 ft. (7 m) to 69 ft. (21 m). After further FINCANTIERI
IS BUILDING FOR THE SEA
Fincantieri is the largest and most diversified shipbuilding yard in the
Mediterranean, and one of the largest in Europe.
The operational capability and structures of the oldest and most glorious Italian companies of the sector have met in Fincantieri, during its more than two century long history. An accumulated, improved, and continuously updated wealth of experience acquired through the construction of over 7,000 vessels of all types allows today
Fincantieri to offer technologically advanced answers to all marine operators' requirements, thanks to its organisation structure made up of three Divisions:
Merchant Shipbuilding and Conversions, Naval
Constructions, and
Diesel Engines. (=FincAnri€Ri » Cantieri Naval Italani SpA
HEAD OFFICE 34121 Trieste / Italy
Via Genova 1
Tel. (0) 40 3193111
Tlx 461136 FINCTSI
Fax (0) 40 3192305
Circle 228 on Reader Service Card pa • •!• • dlnL •uuuuuuiy[fl
A GMT 28 detailed discussion the final desig was refined to a length overall c 61.2 ft. (18.7 m), 49.5 ft. (15.1 m) a the waterline, a beam of 20.8 ft. (6. m) and 3.3 ft. (1 m) draft.
Initially it was envisaged that total engine output of 1,800 k\ would be required to give a 30-to: vessel the contract speed of 28 knots
However, calculations indicated tha an ideal engine choice would be pair of Deutz/MWM TBD 234 VI: diesels each developing 852 hp (62i kW) at 2,200 rpm (continuous rat ing) providing the weight could b reduced to 26 tons. Employin] smaller engines in itself contribute) to weight reduction, but to achievi higher thrust at maneuvering speed a larger, therefore heavier waterje model was selected. Hamilton H57: jets were incorporated, coupled vii long cardan shafts and Centafle: couplings to ZF BW195 2:1 reduc tion gearboxes, included to matcl engine speed to the optimum je impeller design. Electrical power ii provided by gearbox PTO driven al ternators. The total propulsion sys tem finally weighed in at just ovei nine tons.
Voyager is built in aluminum al loy to ABS rules for high speed craft but with weight reduction the driv ing factor, yard and designer workec closely with ABS to ensure ever} saving opportunity was taken with out bending the rules. As a resull longitudinal flat bar stiffeners were cut from 5083 plate, having a highei tensile strength and better yielc qualities than extrusions and both longitudinal and web frame dimen- sions were reduced in the aft third ol the hull.
Moving the wheelhouse to a posi- tion directly over the engines prompted a decision to make it flex- ibly mounted, making for easy re- moval for major engine work. Again to reduce weight in what now had to be a self supporting structure, alter- natives were sought to the conven- tional stiffened, insulated and lined aluminum construction with a prob- able weight of around 20 kg per sq.- m. Various sandwich construction materials were investigated but a panel incorporating Cetex sheets with a Nomex core was ultimately selected. These are supported on an aluminum frame and finished inter- nally with a Dibond decorative panel leaving a 2-in. (50-mm) insulating air gap giving an average weight of only 6.5 kg per sq. m., a third of conventional construction. All bulk- heads, doors and cupboards in the wheelhouse, galley, toilet and stor- age are made of composite panels and Dibond sandwich panels were used for air ducts. Further weight savings were achieved by using poly- carbonate instead of glass for the side windows.
For the 23-ft. pilot transfer boats,
Engelaer had developed and pat- ented a novel active fendering sys- tem which proved entirely satisfac- tory. These craft often make 50 boardings each per day, and not surprisingly the pilots insisted that this system was chosen for Voyager.
Known as Pop-Safe, it utilizes stan- dard polyethylene tubes and bends located in a U-shaped section fixed to the hull, which is part filled with
Maritime Reporter/Engineering News