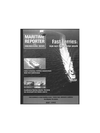
Page 57: of Maritime Reporter Magazine (May 1995)
Read this page in Pdf, Flash or Html5 edition of May 1995 Maritime Reporter Magazine
shields to discovery of underfilm corrosion during visual inspection; and coal tar epoxies, long the favorite of many owners and yards because of their relatively low costs and resistance to water permeation, are losing favor not only because of their inability to be made in light colors for easy inspection, but because coal tar pitch, which increases their water permeation resistance, is a suspected carcinogen.
Meanwhile, the use of surface tolerant epoxy has been on the rise, because they have a wider range of suitable application from near Freezing to nearly 100 degrees F, and better ability to wet less than perfectly cleaned steel than most other tradi- tional ballast tank coatings, providing a better chance for a long-lasting barrier to both liquids and oxygen. (It must be remembered, however, that the degree of cleanliness improves perfor- mance of all coatings.) Light colors are readily available, and newer versions developed in Eu- rope (by Hempel, Sigma and Courtaulds) and
Japan (Kansai) have improved build characteris- tics on edges, where failures have historically occurred first. manufacturer's maximum recommended dry film thickness. The increased film density makes the tank lining less susceptible to damage during butterworthing. Novolac epoxies also reportedly resist absorption of cargo into the paint film better than most epoxies. Extensive studies have been conducted in Europe by Hempel which have veri- fied the excellent properties of Novolac epoxies. • New curing agents increase the adhesion and cureof traditional amine epoxy tank linings. While it is still used in limited quantities with very special precautions in the U.S., it has greatly disappeared from most U.S. manufactured tank linings in favor of new curing agents such as cycloaliphatic amines.
Other countries are not so stringent in preventing its use. • One hundred percent solid epoxy formulations have been introduced by most major manufactur- ers with varying degrees of success. By far the largest problem to be overcome in tank lining application is the removal of solvents from both the tank atmosphere and the coating film. Any residual solvent in the film becomes a potential failure location. One hundred percent solid formulations eliminate this possibility altogether. • An anti-static epoxy tank lining was developed by
Sigma, designed to reduce the risk of explosions caused by a build-up of static electricity. This material is best applied with plural component heated airless equipment. • Several manufacturers are reinforcing their epoxy formulations with increasing amounts of laminar pigments to create better resistance to stress cracking of the coating film and better resis- tance to liquid permeation through the paint film.
Micaceous iron oxide pigment with a specific platelet structure is finding as increasing use for this purpose. • Patented newpolysiloxane systems from Ameron are being tested by at least one major chemical carrier for aggressive cargoes, such as methanol.
The epoxy/siloxane backbone in this formula has shown excellent wettability of the substrate and film density properties in a series of lab and field tests.
Control The Atmosphere
Newer, more sophisticated coatings often require cleaner surfaces to which they are applied and more stringent control of the ambient air during drying and curing cycles. Simple blowdown and ambient air blowers have given way to repeated vacuuming operations and volume, humidity and temperature control of ambient air. Both refrig- eration and dessicant type dehumidifiers are being used to reduce relative humidity below 50 percent inside the tank at all times. Combinations of heaters and dehumidifiers are being success- fully implemented in cold climates. A common failing, regardless of the equipment employed, has been the ineffective use of air circulation. It is essential that wind gauges be used in the difficult recesses of the tank to assure that sufficient flow of air is present above the applied coating film, regardless of the type of coating being used. This is most critical with less than 100 percent solids, solvent-borne coatings, but it is also important with water-based inorganic zincs.
The Cargo: Set Limits
Reputable coatings manufacturers spend a large amount of time and money testing the coatings for their ability to withstand immersion in as large a range of chemicals and solvents as possible. They are usually conservative in their recommenda- tions. Unfortunately, too often the cause of failure is a decision by the captain of the vessel to take on an inappropriate loading in order to increase the profitability of the voyage. Quite often the failure does not occur after that voyage, thus leading the captain to believe that it is acceptable to carry that loading again. However, the softening of the coatings from chemical attack is cumulative, so by the time the failure occurs after the second or third loading, the result is catastrophic failure of the entire tank lining. It is also a mistake to allow too little recovery between loadings, as even mildly aggressive cargoes can cause lining failure if the linings are not given sufficient time to release the liquids or vapors which have soaked into the coating.
Information Is Key
As with most anything in business, the quality and quantity of information on-hand regarding tank linings will help formulate a more cost-effective and efficient solution. Having a coatings expert in- house, or as a consultant, is an obvious first step.
Selecting coatings based on case histories and/or comparative lab tests, and carefully following the coating manufacturer'swritten instructions for sur- face preparation, application, curing, cargo suit- ability and recovering periods between loads is another.
This preceding was from an article by S. G. Pinney & Associates Inc. President Lou Vincent. S.G.
Pinney & Associates is a corrosion and control specialist based in Port St. Lucie, Fla.
For more information on the topic from S.G. Pinney & Associates
Circle 78 on Reader Service Card
Advanced Coating Systems: Cargo Tanks
In the case of cargo tanks, new technology in coatings has been most dramatic. Consider the following examples from major manufacturers in the U.S., Europe and Japan. • Novolac Modified Epoxy formulations have increased the ability of epoxy tank linings to resist aggressive cargoes. The increased resistance to temperature and permeation from liquid cargoes is somewhat offset by the greater internal stress within the coating. This can be controlled by limiting the film build to within 25 percent of the 10,000 tons? No problem!
KAMAG Transporters can handle any kind of heavy or oversize load. A pioneer in the field of self-propelled modular transporters and elevating trucks, KAMAG vehicles have moved some of the most challenging loads in the entire world. Flexibility is the key to success and the
KAMAG system can deliver it. Contact us for further information and solutions to your heavy lift needs.
KAMAG
KAMAG Transporttechnik GmbH & Co.
Daimlerstrasse 14 • 89079 Ulm • Germany
Telefon: (0731) 94 54-0
Telefax: (0731)94 54-707
In North America, call LIFTKING INCORPORATED(216)783-2000
May, 1995 Circle 237 on Reader Service Card 59