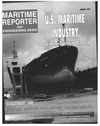
Page 84: of Maritime Reporter Magazine (August 1997)
Read this page in Pdf, Flash or Html5 edition of August 1997 Maritime Reporter Magazine
INTERNATIONAL OFFSHORE UPDATE than comparable solutions.
Buoyform comprises a conical stor- age tank beneath sea level and a deck with living quarters and pro- cessing equipment above it. It reportedly can be moved relatively easily between several smaller fields as each is depleted.
Aker Maritime said that with a 269-ft. (83-m) diameter and a 1,312.3-ft. (400-m) draft, the plat- form's structure has smaller and calmer motions in the sea than either a production ship or a semi- submersible platform. Unlike a production vessel, Buoyform does not require a turret to accommo- date mooring lines and risers — tubes bringing produced oil to the surface from the well — but is held in position with conventional anchor lines.
The combination of drilling, pro- cessing and storage facilities avoids investment in a separate storage system and the cost of hir- ing a separate drilling rig.
Buoyform also can be delivered as a dedicated drilling platform. Aker
Maritime said the development solutions evaluated so far have a 60,000 bpd production capacity and a storage capacity of 570,000 barrels.
Hernis To Provide CCTV For
FPSO
Norwegian company Hernis
Scan Systems A/S will supply closed circuit television systems (CCTV) for a FPSO building at
Korea's Samsung Heavy Industries for Australian oil company
Woodside. The FPSO will report- edly be the largest in the world.
The systems are due for delivery in the latter half of this year, and have a contractual value of approx- imately NOK1.5 million including options for top site camera sta- tions.
In addition, Hernis CCTV sys- tems will be installed on two
Ramform generation ships for PGS currently building at Langsten
Skip & Battbyggeri in Norway.
Delivery of the systems is sched- uled for the fall, and the contract is worth a reported NOK2.3 million.
For more information on
Hernis Scan Systems
Circle 12 on Reader Service Card
EQUIPMENT PROFILE (Continued from page 78) 3,000 to 3,600 rpm output shaft speed regime and geared high speed (to 11000 rpm) compres- sor drive service. This power turbine is an upgraded version of the power turbine currently available on production
LM2500s.
For applications in the 6,100 to 6,200 rpm speed regime, both M&I and Dresser-Rand provide a two- stage, high-speed power turbine (HSPT). Dresser-Rand's HSPT is known as Vectra DR61P.
Continuous operation of both
HSPTs is possible over the speed range 3,050 to 6,500 rpm. Like the
LM2500+ equipped with low-speed power turbine, both the Dresser-
Rand and M&I HSPTs will be available with M&I's DLE and standard combustion systems.
The LM2500+ first-engine-to- test (FETT), a gas generator with a
DLE combustor, successfully com- pleted trials in August 1996. The
LM2500+ reportedly achieved 105 percent overspeed, and showed compressor airflow and efficiency tracking pre-test predictions with
NOx emissions below 25 ppm.
The LM2500+ second-engine-to- test (SETT) was successfully com- pleted in November 1996, result- ing in qualification of the power 84 turbine design and confirmation of power turbine flow function. All performance parameters were reportedly met or exceeded. A third test using a DLE gas genera- tor and M&I's HSPT began in
January 1997. Dresser-Rand's
Vectra DR61P power turbine also began testing in February 1997.
To date, 33 LM2500+ gas tur- bines have been ordered for a vari- ety of gas compression and power generation applications through- out the world.
DATUM
Dresser-Rand introduced the
DATUM line of compressors in
September 1995. These compact compressors are designed to increase well output more effi- ciently. DATUM, in some cases, can handle the same pressure ratio as currently required by multiple compressors. DATUM compres- sors feature standard components for easier maintenance. The bun- dle assembly is modular, and can be removed for maintenance in the shop rather than in the field.
Dresser-Rand was able to signifi- cantly reduce the cost for its
DATUM line, while decreasing delivery cycle times for these prod- ucts. To date, Dresser-Rand has received more than 30 orders for
DATUM compressors for a wide
Heatec Supplies Waste Recovery
Units For Offshore Platform
Pictured is an offshore platform with two Heatec waste heat recovery units.
Schenzhen Petroleum Technology and Development Import and
Export Co. engaged Heatec Inc. to build two waste recovery units for the Shengli oilfield offshore platform in the Gulf of Bo Hai near mainland China. The Schenzhen company is part of the Chinese government and is headquartered in Dong Ying.
Both units recover waste heat from the exhaust of two gas tur- bines used aboard the platforms to drive electrical generators.
Each unit recovers 3,500 kW per hour and the heat is used in the processing of oil and gases from the offshore well.
The exhaust stack of each generator has a diverter gate that routes the exhaust gases through the Heatec units and into the atmosphere. When heat is not needed, the gate diverts the gases so they bypass the heat exchangers and pass through silencers before entering the atmosphere.
Each of the units has a coil that scavenges heat from exhaust gases. The coils, in turn, heat thermal fluid flowing through the coils. The thermal fluid passes through heat exchangers that use the heat for heating the crude oil and drying gases that accompany the oil.For this contract, the Chattanooga, Tenn., based company also supplied a pump package, expansion tank for thermal fluid and electrical and pneumatic controls for the unit.
For more information on Heatec Inc.
Circle 8 on Reader Service Card variety of oil/gas pipeline and plat- form applications. DATUM com- pressors are manufactured at
Dresser-Rand's Turbo Products
Division facilities in Olean, N.Y., and LeHavre, France.
Statoil was able to use Dresser-
Rand's calculations to determine the benefits of using the DATUM compressor. A large North Sea oil and gas field has a 250 to 300-MW capacity. The compressors repre- sent about 50 percent of the installed capacity and up to 75 per- cent of the power actually con- sumed. Factoring in a 15 to 20- year life cycle of the DATUM unit, operating 75 percent of the time over those years, and the cost of the fuel and C02 tax to operate, there is an improved efficiency reflected in savings of $3,000 a kilowatt. Hence, when a five per- cent reduction in power consump- tion is achieved, the life cycle costs are lowered by more than $11 mil- lion. By using the most sophisti- cated turbomachinery equipment available, Statoil will be able to meet the strict environmental reg- ulations in place in Norway.
Statoil will benefit from this tech- nology by the resultant increased efficiency, reduced C02 and NOx emissions during oil production as well as reduced life cycle costs for the fields.
The preceding was excerpted from an article submitted by Elias
Ray, of GE Marine & Industrial
Engines (Evendale, Ohio), and
Odd Guldsten, of Dresser-Rand
A/S (Kongsberg, Norway).
For more information on the LM2500+
Circle 30 on Reader Service Card
For more information on DATUM
Circle 31 on Reader Service Card
Maritime Reporter/Engineering News