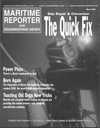
Page 45: of Maritime Reporter Magazine (March 2001)
Read this page in Pdf, Flash or Html5 edition of March 2001 Maritime Reporter Magazine
Coatings & Corrosion Control steel ships are subject to greater degrees of hull flexing at sea. This is important when you consider the corro- sive processes in under-deck and ullage spaces,"
Jansen says. During ballast voyages, inert gas is pumped into the cargo tanks of tankers to prevent the build up of flammable gases from cargo residues. Inert gas is also used to fill up the ullage space left after a cargo has been loaded. The gas used is generally pumped in at a temperature of roughly 45 degrees Cel- sius. At night, the natural drop in temperature will cause the gas to cool to around 20 degrees Celsius.
Even the thermos-flask characteristics of a double- hulled ship cannot prevent this. As a result, the walls lining the spaces filled with gas are covered in conden- sation. Rodney Towers' study suggests that in an inert- ed VLCC as much as 12 tons of condensation can be created each night. "The condensation dissolves sol- ubles in the inert gas mixture that trigger the corrosion process," Jansen explains.
This is particularly damaging for ships with high lev- els of high-tensile steel. Their increased flexing during voyages leads to higher levels of flaking. Flaking exposes fresh areas of steel for the corrosive solubles to do their damage. According to Jansen, "By encourag- ing flaking, high-tensile steel is its own worst enemy."
The good news for owners is that coatings manufac- turers have been hard at work to develop products that will help prevent excessive corrosion. Rodney
Towers' work has been very significant and
Sigma Coatings is addressing the issues raised by his research. Jansen will be helping the company better understand the requirements of modern tanker shipping. "Improved coatings, a clearer understanding of coatings on the part of crews, and investment in coatings by owners at the new- build stage will help prevent double-hulled tankers from causing more problems than they solve," he says.
Wheelabrator Elects New Sales Manager
Wheelabrator Abrasives, Atlanta, Ga., has named
Christopher Pawlicki as the regional sales manager for Ohio, the Northeastern U.S. and Ontario, Canada.
Pawlicki, who has an extensive background in industri- al sales, most recently served as a manufacturer's rep- resentative for various quality products.
See Ship's Store starting on page 55 for more Coatings and Corrosion Control products
Scottish Company To Revolutionize Coating Inspection
Luminous Technologies Ltd. has, after 12 years of research, developed an optically active additive (OAA) that when introduced into an existing coat- ing formulation enables easier inspection during application and through life of the coating — without degrading the performance of the existing coating formulation.
The product, which is targeted for the marine market, concentrates on areas such as ballast tanks that are hard to inspect properly and adequately as the vessel is being built, as well as throughout its life.
The system can be used for the improvement of ballast tank coating, cargo tank coating, confirma- tion of removal of shop primer and any coating application quality.
Instrumental in providing a solution that cur- rently plagues the shipping industry — the product ensures that vessels remain in good condition through life. The protection to the vessel afforded by the coating is increasingly critical and subject- ed to greater inspection by shipbuilders, paint companies, owners and classification societies. In addition, the ballast tank areas have greatly increased as a result of the OPA 90 requirements for double hull vessels
The OAA system, which works in ambient light conditions normally found in a ballast tank during
The two-coat scheme has a reactive first coat that clearly shows up abrasion damage. new construction, is added to an existing formula- tion in such small quantities (less than one per- cent) that the existing formulation performance is unlikely to be affected in any way. OAA causes the coating to become sensitive to certain wavelengths of light allowing for defects within the film such as pinholes and areas of under/over application that cannot be seen by the naked eye.
The system works by adding the first coat of the scheme and using the suitable hand held light so that the coating process can be examined during and after application. The applicator can use the system to ensure that first time application is pro- viding the coverage and not leaving uncoated edges.
Once the coating is dry, the system is designed to enable an inspector to survey a tank using a suit- able hand held torch. The system can enable one sq. m to be examined at a distance of three meters with pinholes easily visible at this distance.
The second passive coat (which doesn't have to be the same color as the first coat) of the scheme is then applied. This coat does not contain an opti- cally active additive. In service, any damage to the topcoat will reveal the active undercoat and there- fore provide a clear and unambiguous indication for maintenance.
Circle 56 on Reader Service Card ...True
So why are your crew using coatings which are not moisture tolerant?
Get longer lasting results with:
NOVA 5000 BARRIER
Long lasting results on crew prepared surfaces*
Allows the ship's crew to control corrosion long term.
Works due to its amazing barrier properties.
Converts and binds rust.
Tolerant to damp conditions.
Safe, 100% solids epoxy and no solvent odour. 1 Recommended for vessels with < 20% corrosion. "compared to high build, modified epoxy and coal-tar epxoy
UMEGUARD MT
As above but recommended for vessels needing more extensive repairs.
Ideal for use with water blasting.
Suitable for all ship areas.
See the light.
Contact your local
Chugoku Marine Paints Ltd.
Chugoku Marine Paints Ltd London
General Enquiries: +44 (0)20 7925 2535
March, 2001 www.maritimetoday.com Circle 214 on Reader Service Card 45