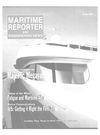
Page 30: of Maritime Reporter Magazine (October 2004)
The Marine Communications Edition
Read this page in Pdf, Flash or Html5 edition of October 2004 Maritime Reporter Magazine
fend-er: 5. Nautical. A piece of timber, bundle of rope, or the like, hung over the side of a vessel to lessen shock or prevent chafing.
This is the definition of a fender' taken from the American
College Dictionary published in 1962. While the idea of ship fenders is ancient in concept, it has, like so many marine systems, evolved to a much higher level of technol- ogy and performance over recent decades. By extension, it is also of higher importance for vessel and facility opera- tors and owners to put this technology to work successfully by choosing the best fender system.
Attracting new business is a necessary and vital component in today's financial planning strategy. Any facility that projects the image of being well maintained, professionally designed and whose goal is to offer the safest berthing for their customers is a facility seeking success. A clean, high performing fender system is an integral part of projecting that image to all your visitors. It is hoped that the following brief explanation of how to choose a fender system will provide some assistance in reaching this goal.
PHASE 1 - Review
Prior to selection of fender sizes and types, it is important to evaluate the specific operational requirements of a facili- ty or vessel and the resultant fender performance criteria.
Important information to gather would include: PierAvharf constmction, the largest berthing vessel size, the vessel's maximum velocity, the allowable reaction force, the vessel's hull profile and the full range of vessel sizes. .All of these factors can then be used in both the subjective and the mathematical evaluations used to define the fender's required capacities.
Subjective design elements include fender positioning and mounting hardware, weather conditions and fender spac- ing. The mathematical evaluation includes using mass and velocity calculations together with specific berthing coeffi- cients to define the kinetic energy the fender system must dissipate during berthing and thus the fender size.
PHASE 2 - Design
Energy: To insure safe operations, the amount of energy generated by a moving vessel must be considered. When a poorly chosen fender system's energy absorption capacity is inadequate or the reaction force is too high, the vessel's energy is transferred to the vessel and shore structure in the form of high loads that result in fatigue or damage.
To prevent this damage from happening to you, it is neces- sary to calculate the energy expected to be generated under all possible conditions and then to choose a fender system in which each fender has the capacity to absorb that total energy. The idea of one fender being able to berth the entire vessel is important for safety factor considerations.
Energy calculations are complex with many variables to be considered. For this reason the support of a competent marine engineer should be sought where possible.
Seaward does offer this engineering support at no charge to our customers.
Overload: .Another important consideration is the poten- tial for overload. Many rubber systems tend to bottom out after their rated compression is reached, resulting in the potential for severe damage to the vessel and shore facility.
In contrast. Seawards foam filled fenders continue to offer protection by absorbing large amounts of energy when overcompressed. Foam fenders also convert a considerable portion of the compression energy to heat, thus making that energy unavailable to bounce' the ship away from the dock, a common problem with pneumatic and some rubber fenders.
Compared to buckling column fenders, foam filled fenders are less stiff in the early stages of compression, which is important in the berthing of smaller ships. A buckling column fender reaches its design reaction force at approxi- mately one half of its rated deflection, and one-third of its rated energy, during which time it is considerably stiffer than a foam filled fender. The foam fender, on the other hand, is softer during the initial compression stages, mak- ing it a good choice for berths that must accommodate a wide range of ship sizes.
Reaction Forces: Reaction force is the total load on both the vessel and the shore sides of a fender. This force must be held within allowable limits to avoid serious damage to the vessel and shore structure.
Each type of fender system has its own characteristic force / deflection curve. For example a buckling column fender will achieve its energy rating at a lower compression dis- tance than a foam filled fender. However, while the foam filled fender reaches its rated reaction force only at the rated energy (full compression), the buckling column fender reaches its rated reaction force at about one-third of its rated energy, (one half of hill compression). Because of this, the highest reaction force occurs during virtually every berthing against buckling column fenders, which decreases the structure's life.
Standoff Distance: Standoff distance, as measured between the vessel hull and the shore facility face, may sometimes be an overriding consideration in the selection of the fender size. Considerations would include:
Crane reach, safety criteria, hull profiles, loading or walk ramps and environmental protection considerations.
Standoff distances for standard size SEA GUARD fenders are presented in the fender data tables available online at www.seaward.com.
PHASE 3 - Selection
Fender Size: After the design considerations are complet- ed, the final step is to select the optimum fender. Fenders too large are unnecessary while fenders too small can represent an unsafe berthing. At this point in the process, the engineer will compile all the important design factors and select the optimum fender size. It must have adequate energy absorption capacity, acceptable reaction load forces, meet the minimum standoff distance, and provide at least two if not three fenders for the smallest vessel to berth against safely.
Quantity and Spacing: At least two fenders are required to keep a ship parallel to a dock, and usually three or more fenders are installed for larger displacement vessels or to provide protection along the entire length of a facility. A commonly used spacing for fenders is 30% of the length of the smallest ship. It should be kept in mind that fender contact can be maintained only along the parallel midbodv of a ship.
PHASE 4 - Installation
Installation should be accomplished in accordance with the site plans if available, or using good engineering practices.
Hardware: There are various approaches to selecting the fender mounting hardware arrangement. A review of typical mounting installations is available by viewing the Seaward website at www.seaward.com.
The definition of a fender system today is much more comprehensive than it was in our maritime past. And so in kind are our investment strategies. For thirty years Seaward has grown with the industry, moved with new technologies, listened to the needs of our customers, and increased our knowledge of what is required to supply the best marine fender available today. For anyone facing the investment of a new fender system, assistance from the Seaward group is available by calling 540-667-5191, or online at www.seaward.com
SEAWARD
SEAWARD is a division of Trelleborg Engineered Products, Inc.
Circle 263 on Reader Service Card 30 Maritime Reporter & Engineering News