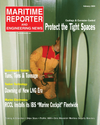
Page 28: of Maritime Reporter Magazine (February 2, 2005)
Read this page in Pdf, Flash or Html5 edition of February 2, 2005 Maritime Reporter Magazine
28 Maritime Reporter & Engineering News
Anyone in the marine business knows the difficulty of maintaining a properly coated ballast tank environment. The ballast tank of an ocean-going ship endures some of the harshest environ- ments in the world, with thousands of gallons of seawater pumped into and out of the tanks, creating an extremely cor- rosive environment. Repairing corroded ballast tanks through traditional meth- ods can cost between $50 to $100 per sq. m. With a ballast tank area of 250,000 sq. m., this could mean an expense of $1.2 million for a complete overhaul.
While protective coatings have tradi- tionally been applied to slow the corro- sion process, the ballast tank areas are notoriously difficult to access for appli- cation and inspection, and oftentimes a missed or incorrectly applied spot can lead to rapid corrosion. A team of com- panies has come forward with a solu- tion: a coating complete with Lumilux luminescent pigments from Honeywell that allows for quick and accurate inspection using ultra-violet light.
Luminous Technologies Ltd., a U.K. manufacturer of colored luminous pastes and concentrates for use in paints and coatings, fabrics and plastics, invented the Optically Active Additive (OAA). A key ingredient in OAA is
Honeywell's Lumilux pigments — com- pounds that absorb energy and emit it as visible light or, in special cases, as infrared or long-wave ultra-violet radia- tion. "Selecting Lumilux was an easy task since no other pigment worked as effectively with the various forms of paint we utilized at the time," said Bill
Cooper, managing director, Luminous
Technologies. When these pigments are added to coatings for application, work- ers using an ultraviolet light can rapidly inspect the coating for coverage. Areas where the coating glows brighter means it is too thick, which wastes materials.
Areas that do not glow or glow less brightly indicate where the coating is too thin or not applied, leaving the tank vulnerable to corrosion. The same ultra- violet detection method can be used for periodic inspection and maintenance to quickly determine if the coating has cracked or otherwise failed.
Standing the Test of Time
Having researched OAA from
Luminous Technologies, a marine tech- nical consultant alerted the Jotun Group, a leading marine coatings, of the new additive. Jotun immediately developed its Balloxy HB Lumi coating system which combines OAA with its own paint formulations. Jotun quickly launched a one-year test cycle and discovered that the Balloxy HB Lumi system offered a variety of benefits compared to tradi- tional maintenance procedures, includ- ing: A 50 percent reduction in inspection time since personnel could inspect large areas more quickly with ultra-violet light; Improved quality of first applica- tion, which can be inspected quickly before a second coat is applied; Substantial materials savings as the system detected areas where too much coating material was being applied; Easier inspection of the coating over its lifespan; Better record-keeping as inspection images can be captured digitally. "Balloxy HB Lumi is the future of bal- last tank protection," said Miles
Buckhurst, product manager, Jotun. "The long-term benefits are clear,
Balloxy HB Lumi protects against dam- age caused by corrosion, improves the standard of inspection while providing considerable savings in time and materi- als." Jotun officially launched its prod- uct in March, 2004, making a major splash in the maritime industry. Balloxy
HB Lumi has attracted interest from shipping companies worldwide and is now in use with several of the world's largest shipping companies.
Circle 15 on Reader Service Card
Circle 225 on Reader Service Card
Circle 234 on Reader Service Card
Coatings & Corrosion Control
Seeing Things in a Different Light
A poorly applied system.
Sigma Adds to its
Coatings Line
Sigma Coatings added another product to its assortment that already includes
Sigma Phenguard and Sigmaguard CSF.
After use in non-marine applications such as land based storage tanks, Sigma
Coatings launched the solvent free epoxy phenolic tank coating Sigma
Novaguard for marine applications.
Sigma Novaguard is designed to offer increased chemical resistance versus other coatings on the market, while pos- sessing the same flow and edge coverage properties of the Sigma solvent free product range. The solvent free nature of
Sigma Novaguard means that it is more environmentally friendly than solvent based products both in terms of VOC emission and health and safety, with the solvent free nature of Sigma Novaguard improving the working conditions for the applicator as well as reducing the explosion hazard. Application can be carried out by brush or roller for small areas and cold single feed airless spray for large areas. Sigma Novaguard can be applied to a dry film thicknesses to 150 microns, enabling a two coat system of
MR FEBRUARY 2005 #4 (25-32).qxd 2/2/2005 10:51 AM Page 4