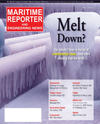
Page 12: of Maritime Reporter Magazine (May 2012)
The Green Ship Edition
Read this page in Pdf, Flash or Html5 edition of May 2012 Maritime Reporter Magazine
12Maritime Reporter & Engineering News INTERVIEWFIVE MINUTES WITH BILL CLIFFORD, PRESIDENT, BAE SYSTEMS SHIP REPAIR BAE Systems has been a prime driver in the consolidation of ship repair business in the U.S. What was the impetus for this expansion?Clifford Our goal has always been to have capabilities and facilities wherever the customer is located. As we have grown, our customer base has grown as well. Our primary customer is the U.S.Navy and we are expanding to encom- pass the commercial market as well. Our current locations allow us the abil- ity to share skilled workforce, lessons learned and efficiencies across the en- tire BAE Systems Ship Repair enter- prise for both the military/government and commercial customer bases in theGoM.These are some tough economic and budgetary times: How has the recent economic slump and budget cutting in Washington affected your business? Clifford Budget cuts in Washington, es- pecially those to the Navy, are always of great concern to our business. The U.S. Navy is our biggest customer and when their budget comes under fire, there is always the threat of decreased workload in our shipyards due to these budget cuts. The slowdown in permitting and drilling activity in the Gulf of Mexico has also impacted our business plans. What do you consider the biggest chal- lenge in running an efficient, profitable ship repair business today? Clifford The biggest challenge is main-taining a stable volume of work to sup- port your core skilled workforce and managing the surges through partners, subcontractors and reliable temporarylabor. Additionally, the sluggish econ- omy affects all business and ours is cer- tainly no different. We have to remain vigilant and seek opportunities whereever they exist. We have some exciting business prospects that we hope come to fruition in the future.In the face of cheaper overseas alterna- tives, what do you count as the biggest challenge to running a U.S.-based ship repair business today? Clifford U.S. shipyards provide high quality repairs and service to our cus-tomers in a very competitive market. The U.S. operates in a free market global economy, which means that we have to compete with countries that have heavily subsidized their shipyards. In order to remain a player in our line ofbusiness, U.S. ship repair companies have to find innovative ways to remain competitive. The Jones Act is an impor- tant government regulation that is criti- cal to the ship repair and constructionindustry as the GoM and off shore wind markets resurge. Over your career, what do you consider to be the leading technologies or devel- opments that have most positively im- pacted the business of repairing ships? Clifford We have worked closely with the Navy to develop innovative and effi- cient processes to weld aluminum struc-tures with extremely high quality. Also, computer aided design and fabrication tools that enable extremely accurate cut- ting, welding and the assembly of very complex steel and aluminum structures. How is BAE Systems investing today? Clifford We invest heavily in workforce development through several programs. Aside from safety, the next most impor- tant aspect of our business is the critical influx of young skilled workers who can learn the trades from our current, agingemployees. When our craftspeople re- tire, they take decades of valuable expe- rience with them. If we can continue toattract young people who are eager tolearn, they can get unparalleled experi- ence in the trade of their choice via theopportunity to work alongside some of the most qualified artisans in their trades.What do you count as the most interest- ing or challenging ship repair job you or your company has ever been involved? Clifford I think the first ever Aegis modernization of the guided missilecruiser USS BUNKER HILL (CG 52) in San Diego Ship Repair a few years back meets the standards of being bothvery interesting and very challenging. BUNKER HILL was essentially the test platform for the Navy?s Aegis modern- ization program. It was our responsibil- ity to get the job done right so that theprogram could continue ? as it does tothis day ? on the remaining cruisersand now it has begun on the early hulls of the Arleigh Burke Aegis guided mis- sile destroyers. Since this was the first job of this type that any of our shipyards had done, it came with countless unex- pected twists during the year that it tookto complete. Fortunately, our employees did what they do best and they executed a highly successful availability, from which we still use the lessons learned today onmodernization jobs to streamline theprocess that delivers a better product to our customers.BAE Systems Norfolk Ship Repair Land Area: ...........................................................109 Acres Principal Drydocks: .....................52,000 ton?950? x 160? ......................................................14,000 ton?570? x 100? Piers: ...........................................................Four (3,015 ft.) Crane capacity: ....................................................to 95 tons BAE Systems Hawaii Shipyard Land Area: ............................................................2.5 Acres Principal Drydock: ...............Pearl Harbor Naval Ship Yard Graving Dock # ...............................................1060? x 135? Piers: .........................................................Three (3,000 ft.) Crane capacity: ..................................................to 150 tons BAE Systems San Francisco Ship Repair Land Area: ..........................................................21.1 Acres Principal Drydocks: .....................56,690 ton?900? x 150? ........................................................14,000 ton?530? x 90? Piers: ............................................................Two (2,557 ft.) Crane Capacity: ...................................................to 60 tons BAE Systems San Diego Ship Repair Land Area: .............................................................20 Acres Principal Drydock: .......................26,000 ton?530? x 106? Piers: ............................................................Five (2,800 ft.) Crane capacity:...................................................to 150 tons BAE Systems Southeast Shipyards Jacksonville/Mayport Land Area: ...........................................................101 Acres Principal Drydock:..........................13,500 ton?608? x 93? Piers/Wharf: ......................................Three/One (1,639 ft.) Marine Railways: ............................Three (1000-4000 ton) Crane capacity:.....................................................to 60 tons BAE Systems Southeast Shipyards Mobile Land Area: ...........................................................423 Acres Principal Drydocks: .....................46,400 ton?788? x 168? .......................................................12,000 ton? 388? x 90? Heavy Lift Barge: ........................14,000 ton?365? x 131? Piers: ...........................................................Four (7,243 ft.) Crane capacity:...................................................to 275 tons BAE Systems Ship Repair(All images courtesy BAE Systems) Work on the historic USS Missouri in 2009 at BAE?s Hawaiian facility. (All images courtesy BAE Systems) The recent dual drydocking of two Aegis destroyers in Norfolk. (All images courtesy BAE Systems) MR May 12 # 2 (9-16):MR Template 4/24/2012 4:44 PM Page 12