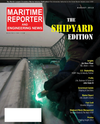
Page 58: of Maritime Reporter Magazine (August 2012)
The Shipyard Edition
Read this page in Pdf, Flash or Html5 edition of August 2012 Maritime Reporter Magazine
58Maritime Reporter & Engineering News ShipbuilderAUSTAL USA Austal USA has recentlyReceived Award for Excellence in Safety for 3rd year in a row from the Shipbuilders Council of America (SCA) for commitment to improving safety and health in the workplace. The industry average Total Recordable Incidence Rate in 2011 was 9.2, four times higher than Austal USA?s rate of 2.3. Received Navy construction con- tracts for 4 Joint High Speed Vessels (worth $634.7 million) and 4 Littoral Combat Ships (worth $x billion). Celebrated the opening of three new shipyard facilities, including: Phase 2 of our Module Manufacturing Facility (MMF) (350,000 sf), a new office com- plex (108,000 sf), and a new final as- sembly bay (59,000 sf). Honored 38 graduates of Austal?s 4- year Apprenticeship Program who re- ceived their certificates of completion and designation as Department of LaborClass A Journeymen. The program is governed by the Department of Labor Standards of Apprenticeship and is cer- tified by the U.S. Department of Labor, Alabama Department of Post SecondaryEducation, and the Veteran's Adminis- tration.Launched and christened first Joint High Speed Vessel, USNS Spearhead (JHSV 1) for U.S. Navy in September 2011, scheduled for delivery in August 2012.Projects In 2004, the U.S. Navy awarded a final design contract for the Littoral CombatShip (LCS) to Bath Iron Works (BIW). Austal is the LCS 127-meter trimaranseaframe designer and builder for this contract. The first order for a prototype was awarded to the BIW/Austal LCS Team in October 2005. USS Independ- ence was launched at Austal's Mobile, Alabama shipyard in April 2008 and de- livered to the Navy in December 2009. The LCS will be the most advanced high-speed military craft in the world and is intended to operate in coastalareas globally. As a key part of the U.S. Navy fleet, they will be highly maneu- verable and configurable to support mine detection/elimination, anti-subma-rine, and surface ship warfare. The tri- maran hull form provides the ship with superior seakeeping, fuel efficiency, and the capacity to carry a large, modular cache of weapons packages. A contract for a second BIW/Austal LCS was awarded by the Navy in May 2009 and Coronado (LCS 4) was launched and christened in January 2012. In Decem-ber 2010, Austal, as prime contractor, re- ceived a Navy contract worth over $3.5 billion for construction of up to 10 moreLCSs. Austal currently has 5 LCS under contract; 4 of which are from the new 10-ship award. Shipyard Investments Austal USA was created to reach the commercial and defense aluminum ves- sel market in the U.S., and it brings a new dimension in high-speed marine transport, using the company's light- weight aluminum fabrication technol- ogy and capabilities. Austal builds large aluminum ships, including naval surface combatants and theater support vessels, at its 125-acre waterfront facility in Mo- bile, Alabama.Austal USA made more than $100Min expansion and improvements in its shipyard from 2008 to 2010. Austal will invest an additional $300M as it doubles its facilities and completes the transfor- mation of Austal. The investments made by Austal in its facility, partnering with AIDT to develop a hands-on employee training program at the Maritime Train- ing Center and with the Alabama Tech- nology Network to implement lean manufacturing principals into the culture of the workforce, and the partnership be- tween the City/County of Mobile, theState of Alabama, and Austal has al- lowed for a reduction in the cost of the U.S. Navy?s Littoral Combat Ship (LCS): evidenced by the $3.5B-award for construction of up to 10 LCS. The methods introduced at Austal also led to the $1.6B-Navy award of the 10-ship JHSV contract, which has helped tolabel the entire Mobile area as a risingstar in the ranks of U.S. Navy ship- building. Austal is committed to implementingR&D initiatives focused on increasing manufacturing efficiency and improving product quality. According to the com- pany, the single greatest technological advancement in Austal's history is the development of the trimaran hullform (the seaframe for the Austal-designed LCS) which decouples vessel length from capacity and permits the marriageof a cost-effective platform with a longer hull form that offers superior sea keep- ing in a range of conditions. Austal also implemented modular manufacturing techniques in aluminum shipbuilding. Applying lessons learned from indus-tries as diverse as aerospace and auto- motive, a new manufacturing approach for aluminum ships culminated with theestablishment of the 700,000 SF Mod-ule Manufacturing Facility. Austal continues to refine its opera- tions and within its warehouse has im- plemented a number of ?high tech?solutions to include Cribmaster software and hardware which manages its main- tenance and repair operation (MRO) supplies, plant MRO vending machines, and provides daily updates of usage of items. Austal installed ?Accuports? which allow for unmanned material cribs saving considerable labor and re- cently installed an RFID Bar Code/ DataCollection coding system which allows for automatic transactions of inventoried parts, real time updates, and traceabilityof parts throughout the process, reduc-ing data entry errors and improving pro- duction efficiencies. Mobile, Ala.-based builder continues building next generation of U.S. Navy warfighters (Photo credit: Lewis Communications) AboveJHSV module on the move.LeftAustal USA aluminum welder workingon USS Independence (LCS 2).MR#8 (58-65):MR Template 8/9/2012 10:23 AM Page 58