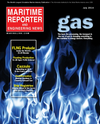
Page 21: of Maritime Reporter Magazine (July 2014)
Offshore Energy Structures & Systems
Read this page in Pdf, Flash or Html5 edition of July 2014 Maritime Reporter Magazine
at reduced load. The modifi cation com- prises computer program analysis, the method of reducing the area of the tur- bine’s nozzles; and “waste gate” (WG) arrangement.
The computer program establishes the optimum nozzle ring area FOPT for the given engine output and type of turbo- charger. The difference between the ex- isting nozzle ring area F and FOPT gives the new nozzle ring area required to achieve the improvement in engine per- formance at a reduced load. The comput- er program determines a new boost air pressure, corresponding to the reduced nozzle ring area, and this new increased air pressure is compared with the design boost air pressure at the engine’s MCR.
To avoid possible surging, the new increased air pressure cannot be higher than the design air boost pressure at
MCR. As a rule, the reduced nozzle ring area is in such proportion that increased scavenging air pressure at operating load is 10% - 15% less than the design scav- enging air pressure at engine’s MCR.
That means that any engine with a modi- fi ed turbo nozzle ring can be loaded, if necessary, at up to 85% of MCR without sacrifi cing turbocharger reliability.
A turbo nozzle’s area reduction is achieved by blocking a few nozzles on existing nozzle rings: nozzles, which should be blocked, are covered by fl at stainless plate (Figure 2). The plate is secured by stainless screws. If required reduction of nozzle ring area is less than 10%, simple bending of nozzle blades can do it. There is no need to buy a new nozzle ring.
The described method of reducing the existing nozzle ring area does not gener- ate any additional stresses to the nozzle or rotating blades.
On the contrary, the thermal stresses become less, due to reduced exhaust gas temperature. Both bending and ten- sile stresses in the blades are less than at design engine load because the turbo- charger RPM remains lower than admis- sible RPM at MCR. It means that there is no potential danger to the normal turbo- charger operation.
M.A.Turbo/Engine Ltd. (in coopera- tion with Vicmar Ltd.) has implemented the turbo nozzle ring modifi cation on 64 different engines worldwide. Some re- sults attributed to the nozzle ring modifi - cations are shown in Table 1 and Table 2.
As can be seen, the fuel savings ranged from 2.8% to 5.0%. Simultaneously, ex- haust gas temperature and NOx emission was reduced. The actual boost air pres- sure is much less than at MCR point: 62% compared to MCR and only 58% of what turbocharger is capable to pro- vide. Accordingly, the turbocharger can supply much more air than it supplies at reduced load, thus reducing exhaust gas temperature and specifi c fuel consump- tion.
However, it is obvious that sometimes the main or the auxiliary engine needs to be operated at MCR. For these cas- es M.A. Turbo/Engine developed the
WG arrangement shown in Figure 3. As shown, an electronically operated WG valve is installed before turbine inlet.
This valve receives signal from either turbocharger’s RPM or scavenging pres- sure and maintain turbo RPM around op- timum effi ciency during any load.
Benefi ts of Turbocharger Modifi cation include: Reduced operational expenses due to less fuel consumption of up to 5%; Less maintenance cost; Greenhouse gas emissions reduction; TC modifi ca- tion cost is 3 – 5 times less than turbo- charger replacement; Pay-back period is usually 1 – 1.5 year.
YOU KNOW IT WHEN YOU SEE IT
Suncor Energy uses HoldTight® 102 to remove salts from its FPSO Terranovaand other similar vessels in the North Atlantic every time it re-coats decks, structural steel, piping and other surfaces exposed to the sea.
NO FLASH RUST = A CLEAN SURFACE
HoldTight® 102 is the standard of performance for preventing flash rust: s NO SALT. Removes all contaminants s NO RUST. Leaves a rust-free surface for 48 hours or more – often 3 to 5 days s NO DETECTABLE RESIDUE. There is nothing left on the surface that might interfere with your coating.
Among rust preventers and salt removers, HoldTight® 102 is the most widely used, reliable, time-proven, lab-tested, field-tested, rec- ommended and approved by coating companies.
Call, email or visit our website today to see why HoldTight® 102 is the best option for low-cost, easy-to-achieve, and easy-to-measure contaminant-free surface preparation.
Contact us today!
International +1 713 266 9339 1 800 319 8802 (Toll Free in N. America) [email protected] www.holdtight.com www.GibbsCox.com ' R \ R X I L J X U H L W R X W D Q G J H W L W G R Q H "
If so, we need you to help lead our Marine Engineering organization as we design leading edge military ships. 15 years of experience including management of design teams at a US Navy-oriented marine engineering and naval architecture service’s company is desired.
BS in Engineering US Citizenship
For more information, email your resume to
[email protected] Call Lorne Epstein - 703-416-3657
Gibbs & Cox is an equal opportunity employer
M/F/D/V. No agencies please.
MR #7 (18-25).indd 21 7/3/2014 1:34:32 PM