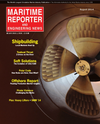
Page 46: of Maritime Reporter Magazine (August 2014)
Shipyard Edition
Read this page in Pdf, Flash or Html5 edition of August 2014 Maritime Reporter Magazine
46 Maritime Reporter & Engineering News ? AUGUST 2014 processes, based on our performance analysis of the systems they are support-ing,? said Berends. ?We can also estab- lish accurately the exact moment when it becomes most effective for both Imtech and its customers to dispatch a service engineer to the vessel. We identify the point when saving costs in one area has cost implications elsewhere.?Today, Berends says that around one half of inquiries dealt with by Imtech?s Global Technology Assistance Centers from shipboard personnel are resolved by changing settings, rather than initiat-ing maintenance. ?The situation reß ects what landside IT users experience, and comparable troubleshooting takes place, which is particularly effective when dealing with intermittent faults.? Remote DeliveryBerends said that the economic melt-down of 2008 and lingering global economic malaise had a strong hand in slowing progress towards full condition-based monitoring, partly because owners have been unable to invest. In addition, in order to fully maximize equipment availability, optimize operating costs and minimize maintenance costs relies on collaboration involving operational-, IT- and Þ nancial managers in an inte- grated business case. But Berends is blunt: ?It has proved a challenge to get the right stakeholders at the same table.??Life-cycle management of vessels is surely available, but owners are skepti-cal about making investments based on promises that there will be savings later on. They are more receptive to straight- forward propositions that are economi-cal, rather than complex proposals whose beneÞ ts are hard to measure. Our position is that we can do pretty much anything the owner requests, but our ex-perience is that it is better to offer gains that are simply understood and tangible.? Berends cites Imtech Marine?s Ad- vanced Support Agreement with Seaway Heavy Lifting (SHL), covering all of the systems onboard. He offers the example of the vessel Oleg Strashnov, where crew working offshore in the Indian Ocean discovered issues with the telephone system but Imtech Marine was able to carry out a remote repair. This avoided a six week application process covering service engineer permits to get onboard.Berends said that remote monitoring of equipment is, by now, an implicit ex- pectation when it comes to meeting the agenda set by regulators. ?Regulatory compliance and environmental protec-tion, such as the veriÞ cation of CO2 emissions, rely on this type of reporting capability. Data collection is also simply the Þ rst step of the staged approach for further measures to increase ship efÞ -ciency as proposed at IMO.?However, to bring home the true po- tential of the remote approach, one of Imtech?s recent initiatives has been to offer customers an audit after one year. He believes any owner resistance will be best addressed by offering solutions that can be proven to work every step of the way. For this reason, Imtech has bro- ken down its remote services offer into a phased and digestible commitment for owners. ?At the new build stage, where the equipment still has to be delivered, we not only include lay-out and cabling speciÞ cations that will facilitate Remote Monitoring; we are prepared to agree a MoU that includes key performance in-dicators,? said Berends.?Once the capability is in place, after an agreed period, we as supplier and the end user are in a truly informed position. After 12 months, for example, we take the opportunity to sit down with our cus-tomer to evaluate and discuss the way forward, and whether their experience persuades them to include more vessels/other types of vessels in the program.?Earlier this year, Imtech put another building block in place to enhance re-mote capability by taking its VDR- connectivity concept live, working with Danelec to offer real time communica- tions between ship systems and shipping ofÞ ces on the safety critical information harvested from real operations. ?All VDR data from ship to shore are presented via a web interface to the customer?s of Þ ce, for scrutiny by su- perintendents and ß eet managers,? said Berends. ?This provides an overview of navigation equipment data and perfor- mance, and the ability to check opera-tional performance such as speed vs. fuel consumption on a random basis. Safety is also enhanced; as well as the chance to review compliance using precise data, Imtech offers an option for real time alerts on non-compliance. ?Reviewing VDR data means the ser- vice company can correct settings re-motely or, optionally, the remote con Þ g-uration of all automation and processing technology can be reviewed in advance of the vessel being attended by service engineers.?Van Leeuwen believes the building blocks have been put in place to over- come owner skepticism on the beneÞ ts of the remote service offer. ?Identifying problems using consistent data that can be interrogated in the right way, having the right processes in place and having the right people available at our GTACs brings direct cost savings,? he says. ?It also ensures that when our service engi-neers are required to board a ship they do so fully informed and ready to act.?Above Right: GTAC at Radio Holland Netherlands in Rotterdam , one of three locations where the VSAT network of Radio Hol- land is monitored and assistance to users of that network is provided. Left: Frank Berends says that around one half of inquiries dealt with by Imtech?s Global Technology Assistance Centers from shipboard personnel are resolved by changing settings, rather than initiating maintenance. REPAIR & MAINTENANCE MR #8 (42-49).indd 46MR #8 (42-49).indd 468/4/2014 12:18:35 PM8/4/2014 12:18:35 PM