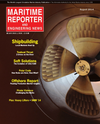
Page 70: of Maritime Reporter Magazine (August 2014)
Shipyard Edition
Read this page in Pdf, Flash or Html5 edition of August 2014 Maritime Reporter Magazine
70 Maritime Reporter & Engineering News ? AUGUST 2014 30% in man hours. It takes a lot of man hours to manufacture ships. So if saving 30%, you are saving time and saving the customer money.? Comer said. Those savings are greatly helped along by software?s ability to aid and enhance the build sequencing (what gets built in what order and in each section, what gets installed in what order) or work schedul-ing process, by enabling the supervisor to pull together all drawings and related data for each part of each module. In fact, some industry observers don?t think this process is possible with the aid of a computer. Another avenue to achieving positive ROI is modularization. Prefabrication came about during WWII, of course, driven by the need to crank out Liberty ships as fast as possible. But many of the techniques developed during that period were not widely adopted after the war, for a variety of reasons. The arrival of desktop CAD and the growth of auto-mated manufacturing, working hand-in-hand, has greatly facilitated the use of modular construction. Building pieces to a whole in different areas was always possible; Þ tting them together accurate- ly was the real stumbling block. Stories abound of sections that were built and brought together with mismatched con-nections. One team thought left, the oth-er right, in a case recalled by Carnevale. Oops.But it takes an integrated system, an organized shop and the ability to work in tandem with many partners during the design process to cost-effectively build ships in a modular manner. Challenges to Overcome Modularity speaks to some of the big-ger challenges facing shipyards: to get the most out of their design and con-struction software, they have to integrate it with their ERP, purchasing and manu- facturing systems ? no small feat. The challenge of ship building nowadays is to Þ gure out how to set up a planning and production process routine that al-lows a scheduler or building sequencer to pull out and package all the data needed about each aspect of each sec-tion of the ship, and which coordinates with materials purchasing, outside sup-pliers, deliveries etc. If you don?t get this part right? You won?t get anything right, insists a 30-year veteran of naval con-tracting with shipyards. Adds Carnevale, ?Nightmares were so widespread that ERP has become a four-letter word.? But integrating these marine applica-tions with the rest of the company?s sys- tems ? Þ nancial, purchasing and manu- facturing ? is critical to success. With so much data being embedded in the design so early in the process, providing that information to other departments allows parallel processes to take place. For example, purchasing can see at an earlier stage what materials are going to be needed, when they are needed and where they?ll be stored or used, and can start working on ordering. And because the design software can more precisely instruct cutting machines on dimensions, weight etc., there is less material waster. The U.S. Navy, which ß oated the Þ rst completely cyber-built vessel when it launched the USS Virginia submarine, struggled with culture and ERP-level systems integration. ?When you have being doing some-thing or 2,000 years, you do get stuck in your ways. There are people in the Pen- tagon who think [ancient Greek math-ematician and engineer] Archimedes is working for some Naval Command [group]and he can be ignored.? jokes CarnevalePush to Open Up Software Complicating this part of the process is the issue of open software: Much of the industry?s applications are propri- etary, which makes trying to exchange or extract data between two different packages cumbersome to impossible, and often in unexpected ways. There was the time, for example, when Ingalls and Bath Iron Works needed to exchange data ? the problem was one set of data was generated out of Cartesian coordi-nates while the other was based on Po-lar coordinates. Mathematical routines enabled the two sets of data to work to-gether ? but with a loss of some accuracy ? enough to drive people crazy. ?The challenge today is that the more intelligence you put into a model, the harder it is to exchange with some other system. Some level of data can be trans-ferred, but not all of it,? explains Gibbs & Cox?s Pinkard. The lack of openness is a major source of frustration in the industry and not likely to abate anytime soon, which forces shipyards to write some of their own interfaces to the pack-ages they need to talk to. A Little of that Human Touch While the software signiÞ cantly cuts down on the introduction of human er- ror, one thing it is no match for, is human experience and intuition. Greater degrees of automation means that ?You don?t have that human er- ror inserted every time you go from a drawing to material, to tech manuals to maintenance,? says Carnevale. He tells a story of a project involving a mixed gas diving system that required special-ized Þ ttings, valves and connectors ? all special orders with long lead times. In particular there were six elbows in the piping system. Once his team, got to the point of installing the parts, it turned out that in several cases, the materials list did not match the number of Þ ttings re- quired, thanks to human error that was never caught. ?It delayed us ? it had a major impact. Simple things like that can be eliminated by a computer system. When a computer system counts, it does not fail to count.?CAD also tackles human error by al-lowing the design to embed all the infor- mation associated with an object into a drawing of it. It?s the Þ rst step in trans- lating an architectural drawing into a material ordering process. However, software is still no sub- stitute for human innovation, ?says Fraunhofer?s Mesing. ?Experience is still a very important factor. Even if you MR 75TH ANNIVERSARY American VULKAN Corporation Ph: 863-324-2424 | [email protected] | www.vulkan.com Your source for premium power transmission solutions for Marine, Indus- trial and Construction Equipment applications in North America (includ- ing Canada and Mexico), the Caribbean and now countries of Central America and parts of South America including the nations of Columbia, Ecuador, Peru and Venezuela. Photo credit: LCS2 American Vulkan MR Jan14.indd 112/19/2013 9:55:54 AM?When you have being doing some-thing or 2,000 years, you do get stuck in your ways. There are people in the Pentagon who think [ancient Greek mathematician and engineer] Archi- medes is working for some Naval Com-mand [group]and he can be ignored.? RDML Joe Carnevale (Ret), Senior Defense Advisor, Shipbuilders Council Of America?I think the time saved to build the ship is the reward. Some people say they can save 30% in man hours.?Joe Comer, principal & naval archi- tect, Ship Architects, Inc. MR #8 (64-73).indd 70MR #8 (64-73).indd 708/7/2014 9:46:30 AM8/7/2014 9:46:30 AM