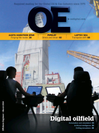
Page 38: of Offshore Engineer Magazine (Mar/Apr 2014)
Read this page in Pdf, Flash or Html5 edition of Mar/Apr 2014 Offshore Engineer Magazine
4.6m-wide cube. They form high-strength and fatigue-resistant nodal joints to con- nect the main leg and brace tubulars in the truss section of the spar platform.
EPIC
They also connect to the heave plates and the hard tank.
“The truss nodes are dif? cult castings because of their sheer size and complex geometry,” Mockford says. “Up to eight brace stubs connect onto the leg can. It is very important to optimize the method of casting in order to ensure a high quality of casting. The casting method is veri? ed by computer simulation of the ? ow and solidi? cation of the steel within the cast- ing. This gives us the ability to get each casting right ? rst time.”
Casting
The ? rst truss node was cast at the end of
June 2013, and the ? rst four truss nodes will have been completed by press date.
A completed mold section.
The production timescale for a typi- cal large node such as the truss nodes and deck nodes is about eight months,
Mockford says. This comprises of: 10 weeks for design and pattern making; 24 weeks for production. Further cast- ings are produced concurrently and completed.
Production time would typically involve: four weeks for core and mold- making; one day for casting; three weeks for cooling; one week burning off the risers and feeder heads; two weeks for an initial heat treatment (normalize, quench and temper); seven weeks for surfance clearning, or fettling, NDT, and weld repair; ? ve weeks for machining; three days for a ? nal heat treatment; and one week for ? nal inspection and release.
Once a cast component is designed, a mold has to be created. First, craftsmen
The mold being assembled in the pit.
Images: Vulcan SFM.
Norway’s ? rst spar – Aasta Hansteen
Aasta Hansteen is 300km west of Bodø and 140km north of the Aker Solutions will provide the subsea production system, nearest existing o