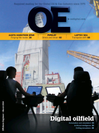
Page 40: of Offshore Engineer Magazine (Mar/Apr 2014)
Read this page in Pdf, Flash or Html5 edition of Mar/Apr 2014 Offshore Engineer Magazine
clean separation of the casting from the mold.
Steel-making, which involves heating the steel up to 1700°C, is carried out on
EPIC site. Liquid steel is then transferred to the mold pit in 90-tonne ladles. Multiple ladle pouring needs to happen at the same time, which means each ladle needs to be heated to a speci? c tempera- ture so that they are about 1560°C when ready for pouring.
A high-strength steel, CSN 400, has been developed speci? cally for offshore structural castings. It is compatible with the steel plate used in offshore structures and is readily weldable.
Liquid steel must steadily ? ow into the mold from below to avoid potential surges created by the pouring process.
Once the casting has cooled, the mold is broken away. To cast the same com- ponent again, additional molds would Three ladles pour the liquid steel into the mold.
need to be created from the original pattern.
Quenching, tempering and fettling
While the pouring takes just minutes, the cooling process can take several weeks, after which the cast piece has to go through a series of treatments.
First, the feeder head and risers, which allow the steel to ? ow in to the mold, are cut away. The feeder head takes an over? ow of liquid steel to “feed” the casting as it shrinks during cooling, so no voids form.
Next, the casting is normalized, quenched, and tempered. During the quenching process, the casting is heated in controlled stages up to 900°C, held for several hours at this temperature, and then water-quenched.
Vulcan’s quench tank is 7.4m-wide, 5m-deep, and holds 79,000 gallons of water. During quenching the tank is agi- tated using impellors and water injection.
This increases the strength of the A truss node is taken from the furnace for quenching, with the quench tank in the casting. However, it also makes it more
Images: Vulcan SFM.
background. brittle. To improve the casting’s ductility, pattern pieces had to be produced. it is then tempered-heated to 580°C and
A mix of black sand and resin is then then allowed to air cool.
packed around the pattern pieces, which Fettling – a re? ned cleaning up process
Scan this page with the Actable app to view are contained in large boxes. The sand – non-destructive testing (NDT), weld- a slideshow of additional and resin is then allowed to dry hard, to repairs, and machining are then per- images. See page 7 for create components, which will make up formed, before the ? nal stress-relieving more details.
the full mold. heat treatment, at 560°C, and air-cooling.
The mold components are then Vulcan worked closely with Technip assembled into a 5.5m-deep pit, forming build a pattern, replicating the external on the design of the hull castings, and the complete mold. pro? le of the casting, from wood, taking with CB&I, the topside designer and man-
Fascia coming into contact with the into account the shrinkage of steel as it ager, to design the deck node castings. liquid steel are coated to prevent any cools to create the precise ? nished size. All castings for the project are due to sand breaking loose and to allow for For the larger truss nodes, 19 separate be complete by the end of May.
March 2014 | OE oedigital.com 42 000_0314_Epic2_Vulcan.indd 42 2/21/14 1:55 PM