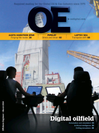
Page 43: of Offshore Engineer Magazine (Mar/Apr 2014)
Read this page in Pdf, Flash or Html5 edition of Mar/Apr 2014 Offshore Engineer Magazine
Production reduced exposure to live pressure control of hydrostatic pressure, attained or V2 was deployed, operated in forward time. calculated once the tool is in the well. and reverse modes, and recovered using •
Increased ef? ciency – increasing the The tractor only stops once battery life electric line.
Autonomous tractoring well access, with multiple entries per is depleted. While operating, the tractor V2 was then taken to ? eld trial campaign; versatility, enabling use in speed can be managed by maintaining onshore, for deployment with a memory became ‘business as usual’ and with it, platform or subsea applications, reduc- back tension on the slickline. production logging tool (MPLT), to further innovations helped to increase ing light well intervention times; data The unit performed two runs, tractor- simulate a full toolstring rig up, and to the applications, from logging operations to desktop, and real time optimization; ing for about 1600ft, at 35-40ft/min on 40 identify possible handling issues, due to to a full suite of mechanical services, reduced equipment footprint; improved minutes battery life. Debris in the well the length of the assembly (>45ft). which includes milling, plug-setting, access to normally unmanned installa- meant it couldn’t be run to the planned The rig up was successfully achieved sleeve manipulation, perforating, and tions, and single well platform structures, depth, limiting function-testing on the (in two stages) and preparations made to • well clean out activities.” Cost bene? t – reduced cost, through motor controller start stop, and a multi- run the tool, after a slickline run prior
BP was aware of several projects, fewer personnel and less equipment. functional timer. to the rig up identi? ed a 950m lock-up which had started investigating the idea “The complexity and technical chal- “Unfortunately due to well debris the depth. of down-hole robots, or autonomous lenges of the project were not underes- tractor didn’t reach target depth however “However, while in the lubricator the intervention units (AIU). Development timated and as such three development important lessons were learned on rig tool prematurely released during pres- work in the US resulted in a caterpillar- phases/versions were identi? ed, namely up procedures, battery re-charging time sure testing, later traced to a ? rmware / tracked prototype tool running in and V1, V2 & V3,” Munro says. along with speed and battery life of the software interface issue,” Munro says. out of a US land well, proving the V1 comprised standard tractor assem- unit ” Munro says. “The back-up tools were then deployed, theory, Munro says. The project bly, tethered to slickline, with forward The goal on V2 was to release the tool, but failed to release at ‘lock up depth.’ was developed by IIC, and the drive only, and additional battery and at lock up depth after it had been con- This was traced to failed insulation on tool system was called micro rig. mission controller sections, to control veyed there on slickline. the release device. Time constraints at the
Further development of this sys- start & stop functions. “It would then tractor in to a desired well site meant that further operations tem however failed to materialize. Its design was based on Welltec’s 2 depth, while recording pressure and tem- were curtailed, and the equipment was
In 2009, BP and Welltec col- 1/8in. standard tractor system, including perature data, before laborated in a project to further the wheels, body, and connections. tractoring back out
The tractor during develop Welltec’s patented Well The aim was to deploy the tractor in a to the initiation testing at the onshore
Tractor system into an autono- horizontal well, using traditional slick- depth, at which live well site, UK. mous unit. Additionally, BP line methods until “lock up depth” was point it would be
Photo: BP.
trade-marked the term “Wireless reached, i.e. the horizontal point where recovered using
Wellwork,” for use in all down- gravity would no longer pull the tools slickline or electric hole operations, where a physi- into the well bore. The mission controller line,” Munro says. cal link to surface was not used. would then signal tractor start up and the “V2 was a sig-
Welltec also moved to adopt the tool would be tractored into, and along, ni? cant technical service “independent well trac- the horizontal well bore. The tool would challenge for the toring” or IWT. then be recovered on slickline. Welltec engineers,
The project aligned both V1 was yard-trialed at Welltec’s R&D since it required a company’s goals to establish a robotized facility in Allerød, Denmark, in a 590ft- release mechanism, means of intervention—i.e. carrying out long, 5 ½in. test loop, then taken to an a reverse tractoring activities without any physical links to onshore well-site, where it was deployed module, additional surface, while providing data from the and recovered successfully. V1 was then battery power, tools to surface, and ultimately being tested in a live well, with 300psi closed- and a casing collar able to optimize the tool from an onshore in tubing-head pressure, on slickline. A locator for depth desktop. Further development could two-stage bottom hole assembly (BHA) correlation, in this result in robots “living” within the well rig up was completed, including perma- case Welltec’s well space, to be activated as and when they nent circulating equipment. hardware scanner are required to undertake either mechani- “The idea was to rig it up, put it in the (WHS).” cal or surveillance functions. lubricator, and set it so that, when it sees V2 was built
Key advantages of this technology are, the pressure test in the lubricator, it goes and then tested according to the project partners: through a test run–the tractor powers up, in Denmark and •
Improved safety – with no wireline the wheels come out for about 30 seconds Aberdeen. Despite connections to surface, other than for and then retract,” Munro says. At this several glitches deployment and recovery; reduced point the tool is ready to be deployed and with the release personnel on location; less complex rig run into the well. mechanism, and the uptime and equipment; no requirement The starting system using a pressure loss of data dur- for winches or complicated mast units; switch, which is activated by a set value ing the yard trial, oedigital.com March 2014 | OE 45 044_0314_ProdOps1_BP.indd 45 2/21/14 12:39 PM