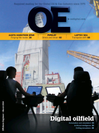
Page 54: of Offshore Engineer Magazine (Mar/Apr 2014)
Read this page in Pdf, Flash or Html5 edition of Mar/Apr 2014 Offshore Engineer Magazine
Subsea
AUV-based 3D laser imaging
Lockheed Martin’s John six major deepwater operators.
Simulation testing included the
Jacobson and Dan McLeod following scenarios which were explain the company’s deemed to be of high interest by the Working Group: latest tool for subsea
Measurement of wellhead • integrity management.
verticality
Performance of jumper • ecent advances in under- metrology • water 3D laser imaging Measurement of anode deple-
R and autonomous under- tion on manifolds and pipelines • water vehicle (AUV) technologies Detection and measurement of hold the potential to deliver revo- pipeline dents, pitting and con- lutionary capabilities for subsea crete coating damage • structural integrity management. Measurement of spoils volume •
Underwater 3D laser sensors now Performance of structural inspec- offer the angular resolution, range, tion against a baseline model • and scan rate to deliver dense, Detection and measurement of 3D-point cloud images of subsea mooring chain pits and chain link structures with millimeter resolu- wear
Simulation testing uncovered tion at tens of meters of standoff
Simulated 3D laser image of a subsea tree several interesting fndings. As distance, while also opening the an example, assume an AUV was door for the application of a wide swimming at 2 knots at approxi- range of software tools from the mately a 5m-standoff from the terrestrial survey industry. target. After insertion of simulated
At the same time, state-of-the-art noise for timing, sensor calibration,
AUVs now include real-time 3D
Results of simulated underwater 3D laser-imaging from a sensor errors, and representative modeling and change detection moving AUV Images: Lockheed Martin.
navigation errors, the results of sim- using high-resolution 3D sonar. ulated measurement of wellhead verticality
Lockheed Martin, supported by fund- Progress to date has included develop- were less than 0.08° from ground truth.
ing from Research Partnership to Secure ment of performance requirements and
Energy for America (RPSEA), is merging interface specifcations between Lockheed Excellent results were also obtained for these technologies through a two-year, Martin’s Marlin AUV and the 3D laser; the measurement of dimensions and/or vol- four-phase project, now in its fnal stage. design, build, and test of the 3D laser; and ume for jumper metrology (<0.5% error),
Using an underwater 3D laser developed integration of the laser into the Marlin. A anode depletion (2-4% error), and spoils at Depth LLC, this new project will enable critical aspect of this development is the volume (<2% error), which all fall well autonomous, real-time, millimeter-resolu- real-time fusion of the 3D laser and sonar within the desired operational accuracies tion 3D modeling, change detection, and data with the vehicle’s navigation and for such inspections.
structural integrity assessment. Results control systems to produce high quality, Simulation test cases involving detec- will be delivered while offering improved motion-compensated 3D models. tion and measurement of dents, pits, and safety, higher-operating effciencies, and
In order to verify proper performance cracks generated errors ranging from 2% reduced costs to the feld operator.
prior to offshore testing, extensive high- to 40%, driven by laser sensor character-
Project objectives include demonstra- fdelity simulation of 3D laser imaging istics and depending on the geometries tion of 3D mapping and change detec- from a moving Marlin AUV platform was used for measurement. Further work is tion using an AUV-based 3D laser. This conducted in Lockheed Martin’s simula- required to understand these errors and will include high-resolution imaging of tion laboratory located in the company’s assess the AUV and sensor operational underwater structures from a moving West Palm Beach, Florida, facility. parameters that optimize these results, but
AUV, generation of high-resolution, geo- Simulation was conducted against a given the range of size of faws being mea- registered 3D models of subsea struc- range of operational scenarios developed sured (1-3cm depth, 1-7cm width) these tures, and detection of changes against a in conjunction with a project working results may be acceptable in many struc- priori structural models. group team consisting of members from tural integrity management applications.
March 2014 | OE oedigital.com 56 000_OE0314_subsea_3.indd 56 2/21/14 12:58 PM