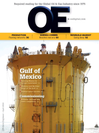
Page 47: of Offshore Engineer Magazine (Apr/May 2014)
Read this page in Pdf, Flash or Html5 edition of Apr/May 2014 Offshore Engineer Magazine
levels are optimized to deliver maximum epoxy resins and cable insulations, addi-
Drilling performance. For example, if the additive tional electrical measurements are carried level is too high, it might have a detri- out on sub-assemblies throughout the test mental effect on the electrical insulation period.
properties or form deposits on mechani-
Conclusion cal seal faces. By developing an oil with increased thermal stability, the ? uid is Functional testing to ensure performance more likely to meet the current and future assurance is increasingly critical, and needs of more powerful pumps and Castrol Offshore has designed a method compressors. In addition, the lubricant to demonstrate the superior performance may need to cope with upset conditions of a lubricant. The approach involves such as seawater contamination and high testing the ? uid beyond the expected breakdown voltage requirements. The conditions to provide enhanced reliabil- lubricant must also successfully pass all ity assurance. The screening tests that original equipment manufacturer (OEM) are carried out take place on bespoke test functional testing. rigs to ensure that the performance of the lubricant is monitored in an environment
The importance of validation testing that is as close to operational as possible.
Thermal stability is a key product attri- Due to the comprehensive testing pro- bute, and once the initial thermal stabil- gram, Castrol Offshore has recently been ity tests are complete the formulation involved in the development of a lubricat- must then undergo physical and chemi- ing/barrier oil that meets the machine per- cal testing at higher temperatures and for formance and environmental needs of the longer durations. This involves testing current and the next generation of subsea
Lubrication evolution legislation covers the North East Atlantic at up to 220°C, with samples monitored boosting pumps and wet gas compressors. and states that all ? uids that have the during the test period to ensure the ? uids The lubricant is fully compliant with the system and are designed to leak a small potential to be discharged to sea by remained stable with no visible deposits. tightest OSPAR environmental legislation amount of barrier oil to the process operational discharge or by leaks that can- The aged samples are then subjected to and outperforms conventional mineral oil stream. The frictional losses in mechani- not be prevented should be assessed and more in-depth testing, including infra- solutions on thermal stability, whiledeliv- cal seals are related to rotational speed registered. OSPAR currently requires that red (IR) analysis which uses a ? ngerprint ering good electrical insulation and drying and pressure and result in local tem- every individual component in a product technique to identify any changes in the capability. The ? nal lubricant solution perature rises. As shaft sizes and speeds is tested for marine toxicity, biodegrad- chemistry compared to an unexposed will increase the operating envelope of increase, the heat generation at the ability and bioaccumulation. To meet sample. If the IR traces remain virtually subsea pumps and compressors. sealing interface is signi? cant, and may evolving environmental legislation, it is identical, this indicates that the ? uid has lead to high peak temperatures. The ? uid essential that environmentally-responsible remained stable throughout the test. Chris Morrissey is required to reduce friction, remove components are used in the development It also is essential that the formulation joined Castrol heat and retain its integrity. Formation of of a lubricating ? uid. performs well against testing for insula- Offshore in 2004 as deposits will upset the seal gap causing tion properties (breakdown voltage). This product advisor for
Lubricating ? uid increased leakage and potential failure. is determined by running an IEC156 test, the subsea business. development process
Together with ever-increasing perfor- in which two electrodes are immersed in He moved on to mance demands, the environmental leg- Conventional, low viscosity lubricating the oil, and the voltage is increase until manage the technical islation relating to chemicals discharged oil formed the baseline for the product an electrical short occurs. This value must service team, and by the offshore industry development program, with the ? rst step be high enough to prevent shorting under then to specialize in product quali? ca- continues to become tighter being the selection of a suitable base high voltage operation within the motor. tion, where he worked closely with many and more widespread. The ? uid. The oil needs to be The ? nal lubricant will subsea equipment vendors. He is legislation was ? rst devel- of a low viscosity to reduce be exposed to internal currently team leader for offshore oped for operations in the shear in rotating elements, pump and compressor product development within Castrol’s
North Sea, but now extends provide low levels of leak- parts such as elastomer central technology function.
to other regions including age across the mechanical and thermoplastic seals Before joining Castrol, Chris has held the Gulf of Mexico, Canada, seals, effectively remove and motor internal parts several design and development posi-
West Africa and Australia. heat from the electric motor and there are methods in tions within Parker Hanni? n UK, and
However, the Oslo and and be environmentally place to analyze the com- John Crane Ltd. These positions allowed
Paris (OSPAR) Convention compliant. Performance patibility of materials. The him to gain a wide experience in the requirements remain the enhancing additive compo- seals need to be tested for design and application of hydraulic most stringent. The OSPAR nents are then chosen that compatibility with the equipment and high performance will deliver the key func- oil by immersion testing mechanical sealing. This work spanned tional requirements, and according to NORSOK many different business sectors such as
Castrol oil blend, 220C, at 4 weeks, with anti-corrosion
M710 procedure. They chemical processing, paper making, additives. Its color clarity Typical mineral oil, 150C, are aged at higher tem- automotive manufacture and oil & gas.
indicates that it is stable at 4 weeks. The darkening peratures to accelerate Chris has a B Eng. Degree in after exposure to high indicates degrading after the testing. For the motor Mechanical Engineering from the temperatures. thermal aging. internals that contains University of Hertfordshire.
Photo from Castrol O