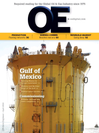
Page 69: of Offshore Engineer Magazine (Apr/May 2014)
Read this page in Pdf, Flash or Html5 edition of Apr/May 2014 Offshore Engineer Magazine
issues associated with a seawater- and analysis of the risks that may be A third approach is the knock on
Subsea fooded annulus.
encountered by the pipe in operations, effect from feld life extension, where
Corrosion can signifcantly reduce and how those risks can be mitigated in a client requires to understand the the operating life of a pipe, which can its design. predicted ability of a pipe to cope with then lead to failure and potentially a A key element of this approach is potentially new demands. In this situ- risk to life or the environment. the implementation of an appropriate ation, a review of the pipe as soon as
As an example, for a typical riser of and ongoing risk-based – rather than possible is recommended to assess any about 350m in the UK North Sea, the prescriptive, time based – integrity damage to it and to calculate the degree fnancial impact has been estimated by program. This should start from the very of impact that will have on the remain-
Flexlife at approximately US$5 mil- beginning of structure selection through ing service life.
lion, once vessel time and replacement the testing and installation stage and All three approaches require the costs have been included. Add to that a beyond, and will consider such factors deployment of modern and novel current lead time of at least a year, with as damage during installation, opera- inspection technology. all the implications associated with tional risk factors, and the design of A relatively straightforward, quick deferred production, and it becomes operational systems, such as the annulus and cost effective method to determine clear that effective repair and ongoing venting system. It will incorporate a whether or not a pipe has an integrity maintenance of risers is a much more regular inspection program to identify issue is an annulus test where nitrogen cost-effective solution.
any immediate issues, or warning signs is introduced under positive pressure
The North Sea has traditionally led the which will require action at a later stage, into the annulus, or a vacuum is created. way in developing robust and proactive as early as possible. In both methods, which involve no riser inspection and integrity plans on Another approach is where a company reduction in production, the aim is to the back of stringent regulation. However, installs a pipe and decides retrospec- establish the size of the free volume in regulatory requirements around the tively that an integrity system and plan the annulus, which will provide infor- world differ. An outer inspection by an is required, or they are faced with an mation on the outer sheath integrity and
ROV may miss outer sheath damage lead- immediate issue and require a solution. therefore any seawater ingress. ing to internal issues in such a complex Of course an integrity plan can be created It is a test which can be undertaken structure as a fexible pipe. It only takes at that stage but activity is very much at any time in the pipe operating life, a hole the size of a thumbnail in an outer reactive. Historically within the industry, but the sooner it is carried out the bet- sheath, letting seawater in, to potentially the retrospective program has been the ter, preferably at the installation stage. create localized corrosion and corrosion more commonly adopted approach. Repeating this test based on a risk-based fatigue. As an example, the majority of timeframe can help identify any annulus
Understanding the risks associated Flexlife’s inspection activity relates to issues at the earliest possible stage.
with riser integrity is critical to the older pipes in excess of fve years old. Of
Deploying Solutions optimal effectiveness of the system. By these, approximately 40% have shown deploying inspection and repair tech- either outer sheath damage or venting As testament to its experience and exper- niques as early as possible the opera- system issues. tise in the sector, Flexlife, has carried out tional life of the pipe can be extended.
Taking a step further back, the development of appropriate integrity systems and planning to this issue because of the hydrostatic can actually help prevent support of the seawater around them. A problems occurring in breach in a subsea fowline experiences the frst place.
fewer corrosion problems, due to reduced
Approaching the oxygenation of the seawater and support problem from the fowline’s cathodic protection (CP) system. There are a number of
By contrast, risers do not enjoy the approaches a company same near-sea surface hydrostatic sup- can take in ensuring port. When over-pressurised, the outer its riser integrity is sheath of the riser will tend to burst at maintained and the the sea surface, or splash zone, where it pipe performs at the is least supported and where there is a optimum. One approach higher incidence of oxygenated seawater is to involve a partner and sporadic – or no support – from the that understands fex-
CP system. This can create signifcant ible pipe, including its general corrosion problems and lead to a design and manufacture, product which is unft for service. at the earliest possible
The service life of the riser can also juncture, to provide a
Regular inspection, monitoring and repair can extend the operational lifespan of the fexible, be reduced due to corrosion fatigue detailed understanding optimising production and mitigating risk.
oedigital.com April 2014 | OE 71 000_OE0414_Subsea3-Flexlife.indd 71 3/22/14 9:04 PM