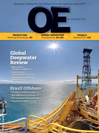
Page 161: of Offshore Engineer Magazine (May/Jun 2014)
Read this page in Pdf, Flash or Html5 edition of May/Jun 2014 Offshore Engineer Magazine
proven solutions and safety gains from its and facility.” For example, a malfunction that might reduce
U.S. oil and gas ? elds to its operations on six output by 200 barrels in a week is caught and ? xed in a day. continents. Before the support centers were conceived, Chevron’s Gulf
Industry results show up to 25 percent of Mexico operations created an Offshore Logistics Decision in operating cost savings, up to 8 percent Support Center to streamline the constant coordination of higher production rates, 2 to 4 percent lower vessels, supplies, equipment and people moving between project costs, and as much as 6 percent im- shore bases and hundreds of structures. Within a year of proved resource recovery within the first opening, the center was logging cost savings from smarter year of deployment of a “digital oil ? eld,” ac- vessel usage and ? eet management, and safety gains as well, cording to global information company IHS Hauser said.
CERA, which is tracking projects at a dozen It is no surprise the Gulf of Mexico presents major chal- companies. lenges for data managers and IT professionals. The dif? cult “Chevron has been a leading light, one of job of tracking and then correcting data issues, such as miss- the early industry drivers, and they’ve worked ing wells and wellbores, was creating a growing resource methodically and thoughtfully to become one of the top three companies working on the digital oil ? eld,” said Judson Jacobs, IHS
CERA research director.
“We used technology to change what we do, rather than optimize what we have
We Have always done,” said Jim Williams, one of the key managers of Chevron’s foray into the digital oil ? eld.
You Covered...
Each day at Chevron’s big Sanha Field off the coast of southern Africa, operators inject millions of cubic feet of natural gas, an essential task at a complex facility that produces millions of barrels of ultra-light oil per year. When a compressor showed subtle signs of overloading, the ? rst person to notice was 6,000 miles away in Chevron’s Machinery
Support Center (MSC) in a Houston of? ce tower.
Now this and other Chevron upstream operations have solid backup to detect any similar situations with the teams and tech- nologies at the global MSC. The MSC actually evolved from an earlier surveillance center designed to monitor compressors in the Gulf of Mexico and California.
“We’ve seen a revolution in sensors to mea- sure what’s happening down in the wells and in production equipment and have seen major advances in process instrumentation. And we’ve connected hardware and data to ? eld performance models, continually analyzing information and making optimum decisions to maximize output,” Hauser said.
INTEGRATED TECHNOLOGY
It’s about automation, but also integration – linking once separate functions, such as maintenance and drilling, and managing them within value chains. This requires streaming all relevant data into asset-decision environ- ments, which fuse humans, data and technol- ogies in a collaborative setting, said Chevron i-? eld specialist Darrell Carriger. “Centralized surveillance allows management of excep- tion, which enables a more ef? cient use of the www.mustangeng.com/automation workforce than manually checking every well oedigital.com 163
May 2014 | OE REVIEW 158_0514OER_Big_Data.indd 163 4/19/14 11:13 AM
AutomationUmbrellaAd.indd 1 4/16/14 6:31 PM