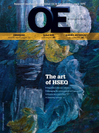
Page 28: of Offshore Engineer Magazine (Jun/Jul 2014)
Read this page in Pdf, Flash or Html5 edition of Jun/Jul 2014 Offshore Engineer Magazine
THE ART OF HSEQ
City Technology’s John Warburton discusses why gas sensors are so essential to high-
Sensory performance gas detection while examining how the right sensor solution can deliver tangible savings and value in offshore applications.
perception wenty years ago, computers were purchased with little such ongoing maintenance value, by its ability to compensate understanding of inner component workings or the effectively for any factors that could be a potential challenge.
T clever technology that actually made the device perform One of the most important jobs of a portable gas detector in so well and effectively. Today, thanks to a an effective global offshore applications is protection in con? ned spaces like tanks, marketing campaign from a leading processing chip manufac- pipelines, drains, culverts and hollow platform legs. Fixed gas turer, we now all appreciate that our computers are only ever detection is featured proli? cally offshore; ? ammable, hydrogen as good as their processing capacity, regardless of any other sulphide and oxygen detection is required at driller stands, impressive functionality they might offer. shale shakers and drill ? oors; compressors, pipelines and seals
This is a good analogy for the gas detection industry; there require ? ammable detection; drains and run-off gullies must is much focus on the gas detection solution itself and all the also be monitored for hydrogen sulphide, carbon dioxide, and value such a device can bring, but the sensor component itself nitrogen oxide. These are just a few examples. is equally important.
Geological and environmental impacts
Aside from the obvious associated industry risks, it is worth
No room for failure
Fixed and portable gas detection forms an intrinsic part of noting that regional factors can have a big impact on sensor use. offshore safety. The sensors used within such devices have a For example, in the Caspian Sea, oil and gas demands have led very hard job to undertake. Not only must they detect gas risks to exploiting sourer wells rich in hydrogen sulphide.
accurately and reliably, but they must do so consistently and Depending on the geology, varying well constituents will be in all environmental conditions. Factors like sea spray or salt extracted presenting a huge variety of ? ammable risks that must particulates, cross-sensitive compounds, poisons and tempera- be negated. A ? ammable sensor must be able to cover all these ture, pressure and humidity ? uctuations must all be considered gases, their differences, and compensate accordingly to deliver and compensated for effectively. A high-quality sensor must be leading-edge performance. Any sensor manufacturer will tell designed in such a way that it can overcome any challenges.
Failure is not an option in such applications: Lives and assets depend on the highest grade of safety provision.
Gas risks are numerous and ever-present offshore, including hydrocarbons like methane, alcohols like methanol, and toxic gases like hydrogen sulphide, sulphur dioxide, nitrogen oxide and carbon monoxide.Standards and minimum provisions vary considerably across the globe. ATEX and EN/UL/FM/CSA regulations are constantly evolving, and they represent a high provision of safety in terms of global standards. As an interest- ing example, the poisoning of ? ammable sensors is a recent hot topic in the Asia Paci? c region, following the Chinese government’s re cent announcement of the new ? ammable gas detection GB153221.1 Standard which becomes effective 2015, designed to enhance safety through more stringent controls over ? ammable detector performance.
Globally, society is becoming increasingly safety conscious, which has resulted in more stringent insurance criteria. This criteria is a catalyst for greater accountability and protection. As a result, today’s sensors need to work harder than ever.
Meeting o