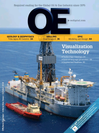
Page 50: of Offshore Engineer Magazine (Oct/Nov 2014)
Read this page in Pdf, Flash or Html5 edition of Oct/Nov 2014 Offshore Engineer Magazine
using an ROV. To meet the project deadline, manufacturing started before the design was complete, using early design
EPIC information to order materials.
Manufacturing was also carried out off IK’s own promises, at a quayside manufacturing facil- ity, in order that the 50-tonne clamp could be shipped directly
A cross section of one of the 35 plugs.
The clamp lowered offshore, instead of needing road in place and closed. he says. “It was a very comprehensive haulage, which would require and intense project and new challenges permissions, adding to the came up all of the time. A safety and risk “The critical element was being able to project timescale. Another manufacturing review highlighted the risk of the sleeve specify and design the equipment, while challenge was sourcing components, at a buckling, so we developed shear plugs carrying out the necessary procurement signifcantly busy time of the year, which to stop this from happening during the and quality control, as well as manufac- meant IK had to source components from elevation, but then we needed a new tool turing and testing in the available time.” across Europe, because some of its usual to install these shear plugs subsea. The suppliers were already fully booked.
Clamp concept for permanently securing the
Plugs platform required 35, 300mm diameter A key part of the project was the clamp. plugs, weighing 250kilos each. We had IK looked at a number of options, taking The plugs, to permanently secure the to make a new tool to drill through the into consideration operational con- pile, were made using carbon steel and steel and grout, in order to install these. straints, as well as manufacturing limita- include wedges, to enable them to be
To make sure the plugs were installed tions, ease of installation and operation. torqued tight by an ROV. This was no
The fnal design comprised, in effect, correctly, we built a 7m-tall fxation tem- mean feat. “We needed to be able to of two parts – the upper clamp, to grip plate, with a common docking interface handle the plugs on deck in a controlled on to the pile, and a lower split clamp on each of the 35 plug slots, for which manner, drill and insert the plugs accu- that closed around pile sleeve, all to be the drilling and installation tool, guided rately subsea while managing the buoy- hydraulically controlled, via ROV panels, by the ROV, could latch. ancy once each 250kilo plug was released
The Strength of Technical Experience and Innovation
Powerful jumper and
Delmar’s experienced engineering team supports mooring installation activities worldwide, umbilical monitoring providing installation analysis, mooring system design, risk assessment,