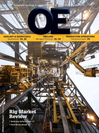
Page 46: of Offshore Engineer Magazine (Feb/Mar 2015)
Read this page in Pdf, Flash or Html5 edition of Feb/Mar 2015 Offshore Engineer Magazine
accuracy is degraded above that dis- tance. However, during processing, the
ODL dimensional control survey (DCS) team flters out all scan data beyond
EPIC 15m, improving the accuracy, reducing the amount of data to be processed, and removing returns from distant spools or modules that would show up as noise.
The digital photographic imagery is
Mapping a platform processed using PTGUI software, which takes 30 images from each survey point and stitches them into a single panoramic image. From this image, six fat images are created, to show the front, both sides,
Laser scanning with behind, above and below the survey real-time results using point.
The colored point clouds are then ofshore-approved tablets registered, using Cyclone, to ensure the is coming, say Carl data from each scan properly aligns.
Bennett and
Finally, Leica’s CloudWorx program, and a CAD (computer aided design) program,
Stewart Buchanan.
ging offshore assets, in the
North Sea and elsewhere,
A require routine maintenance and inspection to ensure their contin- ued integrity. Mobilizing designers and engineers offshore to view and measure equipment and structures takes up scarce bed-spaces needed by maintenance and
Linking together data from multiple surveys to create whole platform virtual model operations personnel.
Images from Wood Group ODL.
An increasingly used alternative is laser scanning, to create precise virtual models of a platform, known as point- modules on seven levels, giving an together into a single virtual model. clouds. These provide onshore engineers indication of the scale of the facil- Using the control network, each with the accuracy (less than 3mm across ity. The offshore phase of the survey surveyor performs the laser scans and an entire platform) and detail required to required 65 days on the platform with panoramic color photography in locations design and fabricate items such as spools, two surveyors. where at least fve control network targets
To put this in context, most surveys vessels and skids. In turn, construction can be seen by the laser scanner.
undertaken require 7-14 days offshore, teams can install the new items safely, Leica HDS6200 instruments are cur- with a single surveyor. Since the DCS rently used, with Nikon digital SLR cam- without encountering any clashes or is used to apply a coordinate system to team was formed about four years eras ftted with fsh-eye lenses capturing failures-to-ft. the database. ago, it has undertaken surveys on 36
Laser scan technology has been avail- color images, and a Nodal Ninja to ensure
Data for decommissioning offshore platforms and foating produc- able to the oil and gas industry for over the camera is in the same aspect as the tion, storage and offoading vessels, and scanner. Each up to fve minute scan, a decade. However, in the last fve years, The laser scan data on the full platform three on-shore facilities, mostly in the performed under ISO 9001:2008, cov- the use of digital color photography to scan was required to model all cut zones
UK sector. ers a 360 degree foor to ceiling volume produce full color point-clouds has fur- and separations to plan a proposed and collects some 50 million pixels, to The scanning was undertaken module ther enhanced its use. The color images method of decommissioning. In addition, provide measurements which will meet by module, and each set of scans were assist designers, engineers, project the surveyors were able to use the point- the tolerances required by fabricators. combined into one database, shown managers, and construction coordinators, cloud to identify the nearest fanges,
For a clash check within a module there in Figure 1. For this project, the scan with visualizing exactly what is on the valves that could be disconnected with- will be 50 scans typically, and a scan of required 1.4 terabytes of data. Some installation, and are ideal for platform out requiring cutting. a platform deck will require hundreds of 220GB of raw data was gathered during familiarization, or considering design The layered CAD drawings, in conjunc- scans. the survey from the total stations, laser options at the start of a project. tion with the model TruView, provide the
The raw data is processed, using scanners and digital photography. as-built information necessary to identify
A full facility frst
Leica’s Cyclone software, to create a sin- and detail all systems that require cuts in
How it’s done gle point cloud; a 3D display of the laser In 2012, Wood Group ODL was tasked each specifc cut zone, allowing complete returns from the scanner in one posi- For a full platform laser scan, a survey with its frst whole, colored-platform module separation. tion. The scanner is designed to ignore team creates a platform control network, scan. The platform topsides are about The decommissioning study team signals returned from beyond 80m, as the to enable all laser scans to be linked 12,200-tonne, comprising 27 individual would not have been able to complete the
February 2015 | OE oedigital.com 48 048_OE2015_EPIC1_Wood.indd 48 1/20/15 6:30 PM