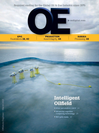
Page 49: of Offshore Engineer Magazine (Mar/Apr 2015)
Read this page in Pdf, Flash or Html5 edition of Mar/Apr 2015 Offshore Engineer Magazine
OneSubsea’s latest boosting system, Technologies avoids the need for big bottom-line. Only by doing that will we
Subsea operating at Chevron’s Jack-St. Malo proj- gravity vessels. get the volume of systems manufacturing ect in 7000ft in the Gulf of Mexico, uses “The next frontier is making these and installation to bring down unit costs a bit more power, 3000 kw, but has four systems more compact, more cost- to where subsea processing becomes times the shut-in pressure, 13,000 psi. effective and easier to deploy,” said FMC commonplace,” he said.
FMC Technologies, which often Technologies spokesman Patrick Kimball. Jon Arve Svaeren, vice president of teamed with Framo Engineering before The technologies needed are available subsea processing systems at OneSubsea, it became part of OneSubsea, has now or within reach, said Ian Ball, director of agrees. “Used in the appropriate situa- joined Sulzer to challenge OneSubsea’s Subsea Domain, a consultancy. “It’s more tions and applied correctly, this tech- dominance in boosting. of an awareness and confdence-boosting nology has proven a very effective tool
The team is offering a new 3.2MW, that’s required,” he said. for increasing production and recovery, 5000psi helico-axial Sulzer pump driven “We need to fnd a way to get more reducing lifting costs per barrel, and by an FMC Technologies permanent operators to qualify and deploy cur- that’s important in today’s environment magnet motor. The motor features a fuid rently proven technologies to boost their of softening oil prices,” Svaeren said. gap in the rotor-stator assembly, reducing friction and increasing effciency.
Progress in oil-gas-water separation
Subsea separation has less of a track record than boosting, but FMC
Technologies is the leader, having installed fve of the last six major sys- tems, often using pumps now sold under the OneSubsea brand.
The history of subsea separation goes all the way back to 1969 when an early version was installed by BP and Total in 79ft at the Zakum Field in the Arabian
Gulf, but the major advances have come since 2000.
In 2001, an oil-water separation built by ABB was installed in 1116ft water depth at Statoil’s Troll feld. Also in 2001,
Petrobras started up a gas-liquid system in 1296ft at Petrobras’ Marimba feld using a Cameron vertical annular separa- tion and pumping system.
Arguably, the frst full-scale system for separating oil, gas and water, with sand- handling capability, was a gravity-based horizontal vessel system built by FMC
Technologies and installed in 2007 at
Statoil’s Tordis feld at a depth of 689ft.
The next big advance was Shell’s
Perdido project at 8000ft in the Gulf of
Mexico. Since 2011, it has run a caisson- based system, built by FMC Technologies, using submersible pumps from Baker
Hughes. Shell put another FMC
Technologies caisson system at Parque das
Conchas off Brazil, started up in 2013.
Total installed a vertical gravity-based system built by FMC Technologies at
Pazfor in 2625ft offshore Angola. It started operation in 2011 and is notable for vessels 30ft tall and 11.5ft in.-diameter with 4in- thick walls to withstand the pressure.
What some consider the most advanced subsea separation system began operation in 2011 at Petrobras’
Marlim project in 2950ft. The horizontal, in-line, cyclonic system built by FMC oedigital.com March 2015 | OE 51 048_0315OE_Subsea1_Transformer_Bruce_em1.indd 51 2/23/15 12:13 PM