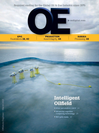
Page 56: of Offshore Engineer Magazine (Mar/Apr 2015)
Read this page in Pdf, Flash or Html5 edition of Mar/Apr 2015 Offshore Engineer Magazine
This “hot-swappable” architecture can only occur if the two SEMs are physically separate from each other and provide enough space for a remotely operated underwater vehicle to remove the decom- missioned SEM without touching or
Advancing
Automation interfering with the operational SEM.
A subsea control system should use
Greg Hale takes a look at a standard programming environment subsea electronic modules. recovery to ensure easy integration, regardless of which manufacturer’s oom and gloom,” equipment the controls “ and “scaling integrate with, Skipp says.
D back” are phrases
The control systems also not heard in the industry should have a minimum in the last fve years. But, 25-year lifecycle to support now there is an opportunity decades of production. to wring more productivity
The controls should have and proftability out of exist- a demonstrated ability to ing assets.
operate “no touch” for a
Norway’s Åsgard feld, minimum of fve years. about 125mi off the coast, Additionally, control sys- has been producing gas tems based on commercial since 2000, but its supply off-the-shelf technology dwindles. Operator Statoil will reduce time spent on created the frst subsea customized programming gas-compression facility and engineering.
to boost rates. The facility
Understanding details will become operational this year and Statoil says it As more sophisticated
Åsgard project. should increase recovery by equipment deploys to
Images from Aker Solutions.
about 278 MMboe and also the seabed, diagnostics help keep production running into 2050. costs by as much as 50% compared to becomes even more vital. Details have
Statoil needed a control system for the costs of building, staffng, operating to delve deeper than just knowing high availability and reliability. They and supplying a topside platform, Skipp something is wrong. Diagnostics should want to cut down on production stop- says. Because subsea installations are provide knowledge of the problem, what pages that end up costing big bucks, said also unmanned, they offer inherent safety it is, and why it happened, so operators
Pete Skipp, engineering manager applied benefts. This presents opportunities to can understand the specifcs of a failure technology at Rockwell Automation. expand production to more inhospitable and build a response plan.
With real estate at a premium, control locations. Subsea production facilities Detailed diagnostics can support overall systems will reside in subsea electronic also can recover as much as 20% more system management and more accurate modules (SEM). from producing felds compared to top- troubleshooting. Diagnostics also plays “Most oil and gas producers opt for con- side facilities, because less pressure ends a crucial role in a subsea system’s SIL trol systems that have already been proven up required to pull the product out. coverage. Basic diagnostics is adequate in topside applications,” Skipp said. “We
Two SEMs coordinate using secure for SIL 1, but additional comprehensive scaled these systems down to Eurocard cir- “black channel” communications links. diagnostics is a must to achieve the more cuit-board format to ft into existing SEMs.
While performing no direct safety demanding rating of SIL 3. The addition
Right-sizing the control system to an exist- function, the links are purely commu- of a second processor to an architecture ing, subsea-qualifed SEM is less expen- nications vehicles. The SEMs carry out increases diagnostic coverage and can sive and less burdensome than designing, peer-to-peer communications on these provide SIL 3 fail-safe coverage.
building and testing a completely new channels, exchanging diagnostic, status Using technology can not only boost
SEM. It’s also crucial that all electronics and input/output (I/O) information, safety, but keep proft levels increasing used in subsea systems be hardened in while also relaying the status of feld during an industry downturn. every practical sense and thoroughly tested devices.
Gregory Hale is the
If a single device or I/O module fails on for the environmental challenges they’ll one SEM, the presence of multiple data
Editor and Founder face, including extreme temperature fuc- of Industrial Safety paths ensures continued operation using tuations and severe vibrations.”
This architecture provides a small and Security Source data from the same device on the second equipment footprint while providing (ISSSource.com) and
SEM, Skipp says. Subsea operations would high availability and high integrity (up is the Contributing only come to a halt if the same two devices to safety integrity level (SIL) 3). Subsea Automation Editor at failed on both SEMs or if topside commu- systems can also reduce overall operating Offshore Engineer.
nications were lost to both SEMs.
March 2015 | OE oedigital.com 58 058_OE0315_Automation.indd 58 2/22/15 11:08 AM