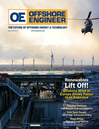
Page 58: of Offshore Engineer Magazine (May/Jun 2019)
Offshore Renewables Review
Read this page in Pdf, Flash or Html5 edition of May/Jun 2019 Offshore Engineer Magazine
TECH FILE Subsea Water Treatment system provides disinfection of raw seawater and reduces the due to the proprietary internal design of the still room mod- number of suspended solids, decoupled from topside water treat- ule resulting in laminar ? ow, causing particles with a higher ment processes. This eliminates the need to push water from the density than water to settle. Standardization is key to the Sea- host facility to the injector. Water treatment and injection can box module design. The module is designed with a treatment now, with this new solution, be provided where and when re- capacity between 20,000 and 60,000 barrels of water per day quired. Water injection and voidage replacement becomes a re- and can be installed at water depths down to 3,000 meters.
alistic and affordable alternative to production by depletion only or by transporting the water from a potentially constrained host,
Test setup to increase the recovery potential of marginal developments.
NOV installed a Seabox module off the coast of Stavanger,
Norway, as part of a veri? cation project in February 2018.
Seabox The objective was to verify the performance of the full-scale
The subsea water treatment module technology aims to pro- module in a representative subsea environment. The project vides high-quality water treatment subsea without compro- was backed by three operators and had a test period of three mising safety, operability or reliability. NOV has made two months. During this period the module’s disinfection and par- operational and quali? ed the system to technology teadiness ticulate settlement capabilities were analyzed. The unit was level (TRL) 6. installed at 220 meters water depth, 550 meters off the shore
The Seabox module is made of glass reinforced polymer from the control station, which supplied power and communi- (GRP) and consists of three major parts: a tray, a still room cation. The subsea pump was installed near the shore and drew and a treatment unit. It is designed to have all interchange- water through the Seabox, where a sample line downstream able parts located inside the easily retrievable treatment unit the pump guided a fraction of the treated water to an onshore to make intervention easy. The module utilizes known meth- facility for water quality analysis. A raw seawater sample line ods toward disinfection of the water and to settle solids. The near the module offered comparison sampling disinfection of water is performed via two in-situ electrolysis processes. First, electrochlorination cells at the inlet of the
Sampling results module produce sodium hypochlorite, and then a secondary
The scope of work, to meet the objective of the veri? ca- oxidizing step where higher order oxidizing agents are gen- tion program, set out an extensive sampling program to verify erated to further decompose dead organic matter. This, com- the module’s disinfection and sedimentation capabilities. The bined with the large volume of the module, will secure enough sampling program was divided into these two major catego- time for the chlorine to react with the organics in the seawater. ries. Together with the project sponsors, NOV created a sam-
The solid settling is provided by sedimentation (gravity), and pling program that involved a total of 13 different types of
Source: NOV 58 OFFSHORE ENGINEER OEDIGITAL.COM 50-64 OE MayJune 2019.indd 58 6/10/2019 10:29:24 AM