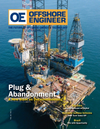
Page 39: of Offshore Engineer Magazine (Sep/Oct 2019)
Big Data and Digitalization
Read this page in Pdf, Flash or Html5 edition of Sep/Oct 2019 Offshore Engineer Magazine
While it doesn’t always grab the headlines when it comes to decommissioning, well plugging and abandonment (P&A) is the biggest cost and headache.
BY ELAINE MASLIN he P&A scope is large and the challenges diverse. pulling casing, and that can take weeks,” says Banks. “So,
It’s also an activity that’s increasing. In 2017, for we’re looking at how to cut or remove sections with thermal the ? rst time, more wells were abandoned in the UK or mechanical means.
TNorth Sea (approximately 160) than new wells were “Another challenge is understanding the condition and the drilled (less than 100), as ? elds reach the end of their produc- integrity of the well and geology surrounding it. A lot of wells tive lives. Here, some 1,400 wells are expected to be plugged have changed hands three or four times, and information is lost. and abandoned over the next 10 years. It’s a costly endeavor But, that information can help reduce risk and uncertainty. So, with no economic return. we’re looking at cheap internal surveys up front and modeling
The UK Oil & Gas Authority’s (OGA) UKCS Decommis- using data and data analytics to reduce risk and uncertainty.” sioning 2019 Cost Estimate Report says P&A activity is esti- mated to account for 44% of decommissioning costs (down Fields trials from 48% in 2016). It’s hoped that bill can be cut by 35%. A number of projects are at ? eld trial stage. For example,
Inroads are being made. The Cost Estimate Report says well the OGTC supported two ? elds trials by operator Spirit En-
P&A costs have bene? tted from improved scoping of required ergy of thermite – a pyrotechnic composition of metal pow- work, and better execution practices, while subsea wells have der and metal oxide – as a way to form a barrier by burning bene? ted from cyclically low rig/vessel rates. But, costs still through tubulars and casing to the formation rock. These saw ? uctuate and more has to be and can be done. Norwegian company Interwell’s thermite technology used in
The Oil & Gas Technology Center (OGTC), a public-funded a well at Caythorpe, in England, in 2018, and also from the body tasked with technology development based in Aberdeen, Audrey platform, in the southern North Sea, earlier this year. is supporting various projects. Malcolm Banks, Well Construc- The OGTC is also supporting work with BiSN, supported tion Solution Centre Manager, at the OGTC, says, “Abandon- by BP, looking at qualifying bismuth alloy as a barrier mate- ment work is increasing in volume and the scope is quite sig- rial followed by a potential deployment. As reported in Offshore ni? cant. Its was one of the ? rst areas the industry wanted us to Engineer (January 2019), BiSN, based in England, is using bis- address (when the OGTC was founded muth alloy that’s melted down hole using in 2016).” Key aims are moving more a thermite heater. When it sets, bismuth toward rigless abandonment technolo- alloy is unique in that it expands. BiSN, gies, reducing the scope involved and whose name stems from Bi for bismuth alternative barrier materials, to replace and Sn, for tin, in the periodic table, has long cement plugs, which would in turn already had a trial in Norway with Aker reduce scope and reliance on rigs. BP, as we reported in January. Another “Historically, cement has been the ? rm looking at use of alloys, deployed default, but it’s not perfect,” says through tubing on electric wireline or
Banks; getting it in place over long slickline and used with thermite down- well sections can be time consuming hole as a replacement for cement, is Ab- and challenging. “So, industry is look- erdeen-based Isol8, led by former Inter- ing at alternatives, as well as economi- well managing director Andrew Louden. cally implementable solutions.” The Isol8 is also working with the OGTC and goal is plugs that can be quicker and looking for ? eld trial opportunities. easier to place, with integrity at least as Separately, Rawwater, in England, is good as cement. That also means ? nd- developing expanding bismuth alloys ing easier ways to place barriers. “His- as sealing elements. The ? rm’s work torically, that’s meant removing whole with bismuth (which it calls ‘molten tubulars, completions and cutting and metal manipulation’) dates back to
Source: Rawwater
SEPTEMBER/OCTOBER 2019 OFFSHORE ENGINEER 39