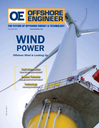
Page 10: of Offshore Engineer Magazine (May/Jun 2020)
Read this page in Pdf, Flash or Html5 edition of May/Jun 2020 Offshore Engineer Magazine
LEADING OFF WALK TO WORK
DUTCH TECH
DRIVES SAFE OFFSHORE
CARGO & CREW TRANSFERS
By Greg Trauthwein ounded in 2007, Ampelmann is a relatively young today,” said Diederick Nierstrasz, Ampelmann’s Manager but fast-growing company that was built on provid- Business Unit Offshore Wind. ing “motion compensated offshore access systems and Ampelmann has worked on a rental and sales business mod-
Fservices” to the offshore energy industry, both tradi- el, the former more so at the beginning when its name and tional oil and gas, as well as offshore wind. While the ‘Walk technology were less well-known. The decision to rent or buy to Work’ (W2W) concept might sound simple in premise, is dependent largely on the scope and duration of the project.
delivery in the offshore environment, one of the most hostile and fast-changing on the planet, is anything but simple.
CONTINUOUS INVESTMENT IN R&D
Working offshore is a challenge, and transferring people
The E1000 system measures 30 meters long and is capable and cargo to and from offshore structures has been the guid- of transferring people and up to 1,000 kg of cargo in wave ing principle of Ampelmann since its beginning.
heights up to 4.5m. Though developed and introduced three
The E1000 a system for lifting heavy loads offshore safely years ago, Ampelmann continues to invest in refning and op- and effciently was launched about three years ago. timizing the system.
At the outset, the system was used exclusively in the off-
For example, the E1000 was designed to transform from shore wind sector, providing an extra bit of stability in an area a gangway for personnel transfers into a crane boom for where, traditionally, the workers are less acclimated to the rig- cargo transportation, and in the past, this transformation ors in working the offshore environment. was manual.
While the E1000 had been used exclusively in offshore
Pins used to be manually deployed to change from people wind, in late 2019, the company identifed an opportunity to to cargo transfer mode, and the entire conversion process took use it in the oil and gas sector, too. at least ten minutes to complete.
The E1000 performed its frst cargo lifts in the O&G in-
As the E1000 gained traction in the market, and effciency dustry for Apache North Sea. It provided not only the W2W became increasingly sought-after, there was the need to reduce solution but also the capacity to lift the necessary tools and operational time and risk, and improve fexibility. Ampel- equipment to the helideck. mann responded by developing a mechanism that made the
As a result, it supported critical maintenance work on a Sin- switch from people to cargo transfer mode easier and faster, as gle Point Mooring (SPM) platform, as well as the refurbish- the E1000 now uses remote-controlled hydraulic pin pushers ment of a helideck. Throughout the 30-day campaign, the to fxate the gangway booms in less than one minute with the system enabled more than 1,925 safe personnel transfers and push of a single button. 354 lifts, transferring 118 tons of cargo. The system was in-
To switch from cargo to personnel transfer mode, the stalled on a 12.1m pedestal and operated at a height of nearly crane hoisting cable is placed in a freewheel mode to allow 40 meters above sea level. the booms to telescope, signifcantly increasing the available “There are about 10 (E1000) systems operating in the feld working time.
10 OFFSHORE ENGINEER OEDIGITAL.COM