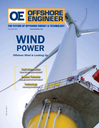
Page 39: of Offshore Engineer Magazine (May/Jun 2020)
Read this page in Pdf, Flash or Html5 edition of May/Jun 2020 Offshore Engineer Magazine
midst the countless challenges offshore drilling and However, these systems have performed poorly after more production operations face, corrosion is a major one. than two years into the testing protocol. Instead, systems
It’s an ongoing issue that acts continuously on struc- featuring select one- and two-coat systems are demonstrat-
A tures, forcing maintenance workers to frequently ing superior corrosion resistance. These results are debunking intervene to blast and recoat steel assets to restore protection. prevailing assumptions, enabling asset owners to alter coat-
Recoating assets can be a costly and ineffcient process that ing specifcations to realize longer maintenance intervals and often slows down production rates. It also requires available lower operating costs.
accommodations for applicators, which are at a premium on
TESTING PROCEDURES MIMIC platforms. Therefore, oil and natural gas producers want to
REAL-WORLD CONDITIONS maximize the service life of protective coatings. To them, get- ting four to six years of corrosion protection from coatings is To ensure testing scenarios were true to real-life coatings an ideal target to contain costs. However, coatings on offshore challenges, technicians tested both typical and atypical sys- structures more often last only 18 to 24 months before re- tems for atmospheric service with different surface prepara- quiring major repairs, leaving producers with higher operat- tions and exposure conditions. They also used various sub- ing costs and more frequent logistical challenges. strate profles to duplicate the angles found on offshore assets.
Because stakeholders are realizing the same diminished lon- Surface Preparations. Lab technicians applied 11 coating gevity results from traditionally specifed coating systems, the systems to test panels featuring different surface prepara- industry could beneft from fnding new solutions that de- tions, including: liver longer asset service lives and reduced maintenance costs.
To help, Sherwin-Williams Protective & Marine initiated a • Grit Blasting According to SSPC-SP10: three-year accelerated testing protocol for offshore coatings in This method removed all dust, coatings and mill scale.
2017. The study is examining the performance of different • Grit Blasting Contaminated with 25 µg/cm2 Cl-: coating systems over various surface preparations to fnd the Lab technicians sprayed these panels with an aqueous optimal combinations for long-term corrosion protection. solution and allowed them to fash rust to a moderate
As the study nears its completion, surprising results sug- grade (as described in NACE No. 5).
gest the industry should consider adopting new specifca- • Ultra-High-Pressure Water-Jetting tion strategies to prolong coating service lives. For example, (per NACE No. 5 WJ-2/Moderate Flash Rust): preliminary results demonstrate superior corrosion resistance Technicians left these panels to rust in a light on assets coated with zinc-rich primers as compared to more industrial environment for 30 days (per SSPC commonly specifed primers that don’t include zinc. In addi- VIS-3 Condition C) and then performed tion, it appears that certain one- and two-coat systems will ultra-high-pressure water-jetting (based on NACE perform better than some three-coat systems. The study’s fnal N o. 5 WJ-2) at 30,000 psi. They let the panels fash conclusions will ultimately help asset owners extend the life- r ust to a moderate grade before coating them.
cycle and reduce the downtime of their offshore assets, while • Power Tool Treatment Contaminated with also saving money. 25 µg/cm2 Cl-: These panels were rusted according to the above procedure before technicians used a po wer tool to prep the surfaces according to
NEW TESTING PROTOCOL SEEKS ANSWERS
The accelerated testing study was designed to better pre- SSPC-SP11. They then sprayed a salt solution on dict the performance of currently used coating systems – the panels and allowed moderate fash rusting to such as epoxy primers, epoxy intermediates, and epoxy or occur before coating them.
polyurethane fnish coats – and to investigate non-traditional coating systems. Exposure Conditions. To mimic offshore stresses, techni-
At nearly the end of the testing and data collection process, cians exposed each set of panels to the following conditions: results are revealing that non-traditional options are enabling improved coating life cycle performance. For example, tradi- • NACE TM0304 (cyclic weathering according to tional three-coat epoxy systems with glass-fake or aluminum- a modifed ASTM D5894-16 exposure), in which fake fller have been thought to provide a longer service life. the electrolyte was synthetic seawater
MAY/JUNE 2020 OFFSHORE ENGINEER 39