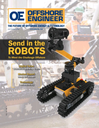
Page 36: of Offshore Engineer Magazine (Jul/Aug 2020)
Read this page in Pdf, Flash or Html5 edition of Jul/Aug 2020 Offshore Engineer Magazine
FEATURE DIGITAL TWINS
The model, which provides a 360º view, is constantly up- UK, a rundown of the safety case through visualization re- dated throughout the asset’s life. Any changes made within duces the requirement for the Health and Safety Executive to the systems it interfaces with are immediately re?ected in the make on-site visits.
VAIM3D twin. Through its integral project management By providing a visualization of risks through simulation and module capability, it allows shutdowns and turnarounds to be respective mitigation, digital twinning can provide insurers optimized, signi?cantly reducing planning time, and it allows and underwriters with a better understanding of the risks and the preparation of maintenance and modi?cation workpacks, control measures being taken. A greater appreciation of the to be done remotely. decommissioning project may assist in driving down premi-
It assists in the execution of, and preparation of mainte- ums. Indeed, insurers have suggested such increased visibility nance and inspection reports, and the results are automati- could remove a zero from the cost of premiums.
cally visualized in the twin to re?ect the asset’s real condition. For operators, digital twinning represents an opportunity to
Furthermore, it helps operators anticipate issues, easing the reduce costs through optimization, ef?ciency gains, collabora- move toward predictive asset management, bringing with it tion and the potential for improved relationships with regula- reductions in operational costs, inspections, maintenance, tors and the broader supply chain. and repairs. Bureau Veritas, with one of its clients, has es- The broader values to the industry include standardization timated digital twinning is reducing hull maintenance costs of approach and processes, a reduction in carbon footprint (OPEX) by 25% over ?ve years. through fewer site visits and better scheduling of vessels, the
For remote operations or where assets have been de- ability to manage across a portfolio of assets simultaneously, manned, the monitoring of equipment has traditionally been potential economies of scale and the simulation of a range of an expensive operation. However, the introduction of 4G or infrastructure and topsides assets.
5G connectivity has signi?cantly reduced such costs allowing Bureau Veritas discovered that by using its digital twin and data to be fed back into the digital twin and enabling a rapid smart data system, operators could save between 9% and 15% assessment of equipment or asset integrity. on total decommissioning project costs. Data from the com-
With the bene?ts of a digital twin system well established pany, which was shared with the UK industry regulator the in cutting maintenance costs, maintaining safety and perfor- Oil and Gas Authority, showed operators could save more mance, and extending asset life, Bureau Veritas then consid- than £2 million on project costs for assets with topsides of ered its bene?ts to the decommissioning sector. 10,000 tonnes, increasing to more than £8.5 million for assets
It was assessed that the value from digital twinning could be with topsides up to 40,000 tonnes. realized across a range of spheres, including environmental, societal, wells, the asset, and regulatory requirements. Digital twinning was identi?ed as a method of improving the de?ni-
A tion of work scope, the quality of proposals, and execution
VERISTAR ef?ciency while lowering estimated and actual costs.
Bene?ts for the supply chain include: the provision of a mir-
AIM3D ror image of an asset which everyone can view and estimate
DIGITAL against the ‘as it is’ information; mitigation of inconsistency
TWIN across tenders; the elimination of additional cost due to access and egress issues on site; a compilation of accurate engineer- ing work packs with minimal requirement for site visits; more ?xed price certainty, and time and opportunities to evaluate alternative scenarios, approaches and technologies.
From a safety perspective, digital twinning enables virtual simulation to run hazardous activity without a physical pres- ence and thereby eliminate or mitigate risks; familiarisation with an asset prior to the mobilization of personnel; the lay- down and storage of plant and equipment offshore; links into
Permit to Work (PTW) systems and the simulation of access and egress from hazardous operations for personnel. In the 36 OFFSHORE ENGINEER OEDIGITAL.COM