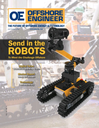
Page 39: of Offshore Engineer Magazine (Jul/Aug 2020)
Read this page in Pdf, Flash or Html5 edition of Jul/Aug 2020 Offshore Engineer Magazine
For instance, a cast component can be less expensive to That said, it’s precisely those folks who can bene?t from produce and more durable than one welded together from learning more about the tremendous potential of these new multiple pieces of steel. Computational engineering software technologies. such as nTop Platform not only provides Design for AM ca- It’s important to understand that 3D printing has been in pabilities but also advanced part-consolidation and topology- development since the mid-80s and is now a mature, well-un- optimization work?ows that can quickly turn a welded design derstood manufacturing process; Boeing, Airbus, and many into one suitable for casting or forging, greatly automating other industry leaders wouldn’t be as invested in it as they are otherwise cumbersome design procedures while decreasing now it if it weren’t proven, certi?ed and cost-effective in the development lead-times. This is why oil & gas industry en- right applications. gineers are beginning to take a deeper look at their product Secondly, the powdered metals used with direct metal laser inventory and ask, “Can we run some of our legacy parts sintering (DMLS), electron beam melting (EBM), direct en- through a computational engineering work?ow and ?nd ergy deposition (DED), and other metal AM technologies are more effective, optimized ways to manufacture them?” nothing new. They are, in fact, the same metal powders—al-
Such design-optimization work?ows can also be applied to beit on a ?ner, more well-controlled scale—used in metal in- mold or forging dies used to make these redesigned components. jection molding, a process that gained popularity after World
Indeed, tooling-geometry generation is an integral part of the War II and is itself used to make diamond-coated oil and gas design process with the software, extending its uses well beyond drilling tips (which themselves present opportunities for the the world of additive manufacturing. And since the software gen- generative design and topology optimization capabilities of erates 3D objects mathematically—via a function called implicit advanced computational engineering software). modeling—rather than the boundary-based generation used What’s most notable about all this is the game-changing with most engineering packages, multiple design iterations can potential of these new technologies. Cutting heads, heat ex- be created and tested far more quickly, further reducing costs and changers, pumping and ?ltration equipment, drill motors— product lead-time. Part consolidation through design optimiza- pick an oil and gas component and chances are excellent that tion also offers the bene?ts of decreased assembly times and sim- it can be improved through new digital redesign tools and pler supply chain logistics even for traditional process operations. either 3D-printed or produced via more traditional means.
Further ahead, the integration of advanced sensors and other electronics into such components raises previously unimagi-
Developing the confidence to move forward nable prospects for ?nely tuned, real-time measurement and with new technologies monitoring of drilling operations.
Despite these robust capabilities, neither advanced computa-
Software providers are beginning to work on creating speci?c tional engineering software nor additive manufacturing is go- ing to “turn the oil and gas world on its head” anytime soon. toolkits, with input from oil and gas partners, that will provide
Change doesn’t happen overnight, especially in an industry with automated, reusable design work?ows that enhance collabora- a rich, successful history, that is managed by decision-makers tion and serve this speci?c market’s needs best. These virtual tools will help speed optimization of the real-world ones. who tend to prefer the tried-and-true over the cutting edge.
JULY/AUGUST 2020 OFFSHORE ENGINEER 39