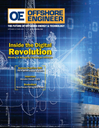
Page 28: of Offshore Engineer Magazine (Sep/Oct 2020)
Read this page in Pdf, Flash or Html5 edition of Sep/Oct 2020 Offshore Engineer Magazine
FEATURE SUBSEA PIPELINE will cost money – and the current PRSI Pool members doesn’t connector systems. DW Rupe, its deepwater equivalent, has have a need for welding at that depth. A bigger need is dealing been running for 13 years. Both are project managed by Stress with bi-metallic materials, found in clad or lined pipelines. Engineering Services (SES) out of Houston.
“There’s no qualifed system in place to repair in-situ and RUPE, founded in 1978, has 35 co-owners covering more that’s a big gap. We are to launch a project where such repairs than 8,570 km of 6 – 36in pipeline around the world. can be done by welding in the future,” says Berge. It currently has 21 clamps, 44 connectors, and 45 misalign- ment ball fanges in stock. As an indication of tool usage within
A Response to Underwater Pipeline Emergencies a 25 year period, RUPE has delivered 57 repair clamps, for
RUPE and DW RUPE are the US-based equivalents to <1m repairs, and 26 connector assemblies for pipe section re-
Norway’s PRS. RUPE, standing for Response to Underwater placements, including misalignment ball fanges, with the busy
Pipeline Emergencies, has been running for 42 years provid- periods usually coinciding with hurricanes. For example, 2005 ing ANSI 900 class diver assisted repair clamps and spoolpiece (hurricanes Katrina and Rita) saw a need for 13 tools, while
The RUPE clamp and connector tooling is stored and cared for by
Stress Engineering Services.
Images from RUPE 28 OFFSHORE ENGINEER OEDIGITAL.COM