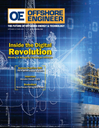
Page 38: of Offshore Engineer Magazine (Sep/Oct 2020)
Read this page in Pdf, Flash or Html5 edition of Sep/Oct 2020 Offshore Engineer Magazine
FEATURE POWER GENERATION equipment to metal handling/bending machines, and, of machinery, for example laser cutting machines that today are course, the quality of the insulation materials themselves. fve times more effcient than machines were 20 years ago, but “The most important aspect is the grade of the material,” at the same price point. And the advent of CFD simulation said Cronauer. “You can buy a 20 mm material for 10 Euros has allowed it to ensure that not only are its insulation solu- or for 7 Euros, but the fact is, this highest technical require- tions optimized for heat and vibration characteristics, but that ment for our material is not temperature, it’s vibration. Even they are engineered for ease of assembly and maintenance by the cheap stuff that you can use for the roof of your house can unskilled workers; to maximize material use, „so maybe we give you high temperature protection, but it’s the vibration don’t neet 2 mm thickness, maybe 1 mm is enough. And do that is a killer with a very bad infuence on the lifetime of the we need 215 screws, or maybe only 120?“ insulation and the machinery.” Thermamax continually invests in R&D to test new mate-
In this regard, for the marine sector Thermamax uses stainless rials, but to date stainless steel and fber materials are still the steel and a stitched and woven insulation fabric that is designed go-to. “There is some movement (at the R&D departments to better withstand the pressures of heat, vibration and time. that manufacture insulation material), but there hasn’t been
Over the years Thermamax has continued to invest in new a real breakthrough. For example, a cladding design without
THE TMAX-RETROFIT n the engine room temperatures are dependent on the price of oil and their 4. Manufacture: First, Thermamax highest and reliable fre prevention willingness to invest.” produces a prototype. Which will be is vital. As 3D details are often not test-installed on a mock-up in order to available for older engines, retroftting 1. A 3D-Scan of the engine to ensure guaranty best ft later on the engine.
I with SOLAS-compliant high-performance the best ft of the exhaust gas and The individual Tmax-Insulation Cladding insulation systems has only been possible turbocharger cladding. Results of the scan is now ready to use and can be installed.
to a limited extent until now. are used as the basis for preparing digital
With Tmax-Retroft, older marine 3D models. 5. Installation: Thermamax installs the engines can now also be upgraded with exhaust gas/turbocharger cladding – frst high-temperature insulation systems 2. Reverse Engineering: Based on the the prototype – on your engine.
which exceed SOLAS guidelines. The scanned 3D profle, Thermamax develops all-in-one package provides all services a CAD model of the engine. For this it 6. Thermography: To ensure that the new – from the preparation of the engine’s frst generates a polygon network in STL insulation system performs as required, 3D profle to the thermography of the format from the available data. This is Thermamax performs a thermography developed and installed insulation system converted into standard geometries and test.
– all from one source. “We see retroft free-form surfaces. From these attributed opportunities, as there are many old surface models and own on-site photos, Tmax offers ships with old engines with old insulation we can then create a CAD model in the 1. a SOLAS-check in order to provide systems which are rotten and do not have STEP or IGES format. a profound assessment to the vessel any fre protection properties anymore,” responsible. Regardless of whether the said Steffen Cronauer. 3. Design and Simulation: Now starts customer buys the insulation, if necessary,
He noted that many engine the classic design process. On the basis of at Thermamax or renews it on his own; manufacturers – Thermamax’s main a 0D/1D thermal calculation Thermamax customers – are not inspired to release defnes material and thickness of the 2. For Tmax-Insulation cladding, the a retroft system for an engine released insulation. The detailled constrution is company offers a regular maintenance 25 years or older, and the decision to made in Creo, a specialized software. service during which the insulation is retroft an insulation system requires The result is a durable exhaust gas/ checked against SOLAS requirements conversation between the ship owner and turbocharger cladding which reliably and takes care of the production and the engine makers. “This is the biggest lowers the maximum surface temperature replacement of the installation if hotspots opportunity for us in the maritime sector. below 220°C and even below 100 °C, are detected.
The offshore sector is interesting, too, depending on requirements.
38 OFFSHORE ENGINEER OEDIGITAL.COM