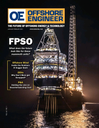
Page 34: of Offshore Engineer Magazine (Jan/Feb 2021)
Floating Production Outlook
Read this page in Pdf, Flash or Html5 edition of Jan/Feb 2021 Offshore Engineer Magazine
FEATURE DRILLING & COMPLETIONS
Subsea Connector
Delivers Cost Savings,
Improves Safety for Critical
Service Environments
TESTING UNDER EXTREME CONDITIONS PROVES THE
RELIABILITY OF INNOVATIVE SUBSEA CONNECTOR DESIGN
By Scott Elisor, Dril-Quip arket conditions have painted the oil and gas in- weakness in the wellhead pro?le design. Findings revealed dustry into a corner, where cost containment is that the BOP connector, in some cases, exhausted fatigue life critical to survival. At the same time, the indus- in as few as 12 days during drilling. The bolts at the top try is pushing the limits of system performance of traditional connectors were found to be one of the most
M as exploration and development move into increasingly harsh signi?cant design weaknesses. These bolts bear most of the and more demanding environments. In many cases, areas of load in the system and are susceptible to embrittlement and operation are characterized by high fatigue and severe bend- hydrogen-induced stress corrosion cracking. Failures – the ing in shallow water, and high-pressure/high-temperature consequence of a design that places the bolts in the primary (HPHT) deepwater conditions, all of which can affect the in- load path where they can experience cyclic fatigue loading – tegrity of subsea systems. The need to adapt to the demands have occurred in connectors commonly used in the industry.
of complex offshore ?eld developments continues to raise the Improving system safety meant creating a connector bar for performance at a time when E&P companies can ill without these weaknesses and testing it to con?rm its per- afford costly downtime or unforeseen safety incidents. formance in high-fatigue, high-bending conditions, and
Reliability is vital for subsea systems because the cost as- HPHT environments. sociated with replacing worn components can have serious re- percussions, interrupting operations and negatively impacting
A BETTER SOLUTION project economics. Now, more than ever, offshore companies
The Dril-Quip engineering team evaluated traditional con- need solutions that improve performance, minimize nonpro- nectors and applied their understanding of the vulnerabilities ductive time (NPT) and decrease maintenance costs.
to de?ne design requirements for a new wellhead connector that could accommodate stresses in the load path caused by
COMPREHENDING CONNECTOR rig mechanics, ocean currents, vortex-induced vibration, and high-pressure environments.
CHALLENGES
The result was the DXe connector, which, when combined
Results from research carried out separately by Statoil (now Equinor) in Norway and the Bureau of Safety and with the DXe pro?le, delivers superior fatigue resistance and
Environmental Enforcement in the U.S. exposed a critical versatility that allows it to be con?gured easily for both the 34 OFFSHORE ENGINEER OEDIGITAL.COM