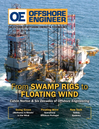
Page 34: of Offshore Engineer Magazine (May/Jun 2025)
Read this page in Pdf, Flash or Html5 edition of May/Jun 2025 Offshore Engineer Magazine
GOING GREEN BIOFOULING CONTROL
Images courtesy Hydrex
I've seen an FSO in Africa, which had been in the water for 13 or 14 years, and the ship’s bottom was completely perforated from stem to stern." – BOUD VAN ROMPAY,
FOUNDER AND CEO OF
Diver cleaning biofouling
THE HYDREX GROUP concern. “If we have signifcant amount of marine growth and CEO of the Hydrex Group. “I've seen an FSO in on our hull and thrusters, this will impact fuel usage dur- Africa, which had been in the water for 13 or 14 years, ing transit and in operations but may also, under extreme and the ship’s bottom was completely perforated from cases, impact the performance of the vessel.” stem to stern, straight through. And that was a 25-mil-
The need for underwater inspections in lieu of dry limeter plate.” docking (UWILD) drives biofouling management for Epoxy (polymer) coatings are very porous, he says. static assets such as FPSOs. Mark Barnbrook, Technology “That lets the water through, but also creates an opening
Manager for FPSOs at SBM Offshore, says typically bands for the secretions of the animal fouling. Their glues are of conventional TBT-free self-polishing or polymer coat- very tenacious and they penetrate. They’re designed to ings are used on the hull. For sea chests, a silicone coating penetrate because how do you cling to a rock?” This hard is used. “These are easy to clean, but very easily damaged, fouling cannot be removed without causing further dam- so they are not applied on the shell,” he says. age to the coating, exposing more steel to corrosion. It is
Inspections are typically done on fxed schedules of 2.5 a vicious circle, he says. Van Rompay has found that im- or fve years for FPSO conversions, but the company is permeability can be achieved with a thick, glass-platelet moving towards risk-based inspections for its newbuild reinforced vinyl ester coating.
FPSOs. “Quite often we use high pressure water jets to The foating offshore wind industry faces some unique remove bioflm,” Barnbrook says. “If you’re too severe challenges. The diameter of mooring lines and dynamic with cleaning tools, then you start to damage the coating cables are substantially smaller than those used in the oil and risk corrosion.” and gas industry. Dr. Stefania De Gregorio – Principal Ma-
The root cause of corrosion is the use of coatings which rine Ecologist at Fugro, says biofouling can cause fatigue are porous and fragile, says Boud Van Rompay, Founder life reduction, as it increases the effective mass of a structure 34 OFFSHORE ENGINEER OEDIGITAL.COM