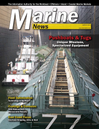
Galley Grease Harms Equipment – and the Environment
By John Paparone
Cleaning up the wastewater stream on marine vessels isn’t just about removing hydrocarbons out of oily separators and bilges. Workboat galleys harbor a tremendous amount of FOGs (fats, oils and grease) that, if not properly disposed of, can be a health risk, damage equipment and add to overall operational costs.
Even if vessels are equipped with sophisticated grease trap systems, the introduction of nontoxic, neutral pH biologic compounds into the trap and/or waste stream is a necessary step to reduce toxic buildup and environmental pollution. Without pretreating the ‘junk’ where it accumulates – and continuing to treat it regularly – the operator never really gets rid of it.
Look, for example, at a typical grease trap issue: passenger vessel restaurants and galleys deal with FOGs on a daily basis. Food grease gets washed down the sink, ground up in the disposal, and ends up in the grease trap. A grease trap is typically a holding tank that separates FOGs from the galley’s drain prior to moving to the gray water holding tank. The solids will naturally build up at the bottom of the trap. But grease and oil will always fl oat to the top of the water, making the water murky. This waste has to be disposed of.
On board, the waste stream from the galley gray water holding tanks – depending on regulations related to vessel size, trading pattern, etc. – is held for pump out at a port facility or may be pumped overboard. This relocates the ‘problem’ and transfers responsibility to someone else to deal with; a costly and time consuming process. Pump out at the port facility is expensive, and discharge into the ocean is nothing but ‘permitted’ pollution.
Industry did the same with plastic over the years, resulting in huge floating gyres (floating plastic debris fields) that we are now trying to clean up. These gyres affect our food supply and needlessly kill and mutate ocean creatures. Wouldn’t it stand to reason that FOGs, detergents and cleaning chemicals – even if they are touted as phosphate free or readily biodegradable – will have a negative impact as well?
This is where the science of bioremediation plays a big role. Bioremediation is nothing new. It has been around for centuries and has been studied more extensively, since the 1940s. It’s been used with success in several industrial industries, but its adoption into the maritime industry remains slow. Why? Because people haven’t been educated on how to compare the mainstream ‘green’ cleaning and cleaner/ degreaser products they use now and the ones that actually stop toxic build up and have no toxic compounds in them.
Bioremediation is the process of using naturally occurring, safe and beneficial microorganisms to degrade environmentally harmful contaminants and turn them into nontoxic compounds. In particular, these organisms will break down petroleum hydrocarbons and transform them into carbon dioxide (CO2) and water. Further, this natural process will produce valuable bio-nutrients that can be utilized by both plant and aquatic life.
According to a study carried out at the student center of the Texas Christian University by the Environmental Science Department entitled “Comparison of Four Treatment Methods for the Removal of Lipids and Food Waste in a Grease Trap Environment,” the use of bioremediation made a significant difference in the amount of FOGs.
The study compared pumping the trap, bacterial inoculation (introducing bioremedial microbes), aeration and a combination of aeration and inoculation over a several month period at the University’s cafeteria. The paper states that “when microorganisms are exposed to contaminants over a period of time, they tend to mutate (due to their rapid cell division) to a strain of microorganism that is capable of utilizing the contaminant as an energy source.” That means that using nontoxic and noncaustic bioremedial products introduces bacterial microbes that love to “eat” grease. These grease-eating microbes start to break down the FOGs, and over time, continually eat them, reducing the amount of “junk” to deal with in the disposal stage.
Any food establishment – whether on land or at sea – increasingly has to keep up with stringent environmental regulations for dealing with grease and hydrocarbons. The standards are getting more complex by the day. That’s why pre-treating wastewater is essential before it goes any farther. In fact, the paper also states: “While frequent pumpouts of the trap can greatly reduce the odor and clogging problems, there is still the problem of disposing the accumulated waste contents (oil, grease, settled food particles and gray water) of the trap … The process of breaking a compound down to CO2 and H20 is very complex, and can only be accomplished by a living organism through many metabolic steps” (Grubbs, 1991).
The study concluded that “Even with the slower-working anaerobic bacteria in treatment II, there was still a significant removal rate that was comparable to having a grease trap pumped every two weeks.” Results illustrate the fact that there is sufficient retention time in the grease trap environment for bioremediation to be effective when the trap environment is augmented using aeration and specific bacteria. The study continues, “This therefore decreases energy usage and costs to the treatment plant and increases the life of the treatment facility.” Aeration may be accomplished via the natural water flow moving through the galley/kitchen drainage system, thus not requiring any additional mechanical insertion of aeration capability.
In another study, a nontoxic, noncaustic bioremediation product called GTO was introduced. Developed for the food processing and manufacturing industries by EnviroLogics BioBased Technologies, Inc., the product digests the grease, fats and organic wastes that accumulate in grease traps and drain lines. GTO was introduced to see if the waste system could work more efficiently at breaking down FOGs and reduce the monthly disposal costs. A comparison of before and after the study began is depicted in Table 1.
By the end of the study period, the BOD level was less than 200 and the TSS was less than 240 – meaning negligible. Best of all, there were no surcharges incurred. All this meant a significant bottom line savings. When maritime problem solvers tend to focus on adding another mechanical device to manage these situations, that ‘solution’ involves additional space, engineering solutions and/or power requirements, just to name a few impacts. And, while Vessel General Permit and other regulations ‘require’ detergents that are phosphate free and degreasers that are rapidly biodegradable, these are NOT standards. Standards should be based on toxicity to the aquatic environment.
The only part of the cleaning detergents that is readily biodegradable is the cleaning solution itself; the result is the chemicals are biodegraded, but the FOG, bacteria, etc., they removed or cleaned, still remain. That’s why it’s imperative to constantly clean and maintain grease traps with the right cleaning solution so they can function as they’re designed.
We have done little to tax the chemical industry to develop cleaning products that fit our definition rather than theirs. The technology to develop cleaners, degreasers, etc., does exist to manufacture nontoxic, noncorrosive and noncaustic solutions for areas such as bilges and galleys. The Centre for Environment Fisheries and Aquatic Science (Cefas) based in the U.K., has demonstrated this in the North Sea. Beyond this, these products will compliment and reduce the strain on existing systems, thus allowing installed mechanical systems to have a longer service life.
The maritime community needs to take the initiative to develop acceptable aquatic toxicity standards and drive industry to meet those standards. Bioremedial products are not an end-all, but rather compliment existing technology, will extend the useful service life of existing systems and will save money in disposal costs.
John Paparone is Principal of Environmental Solution, Inc., a veteran owned business that sells and distributes more than 30 EPA-approved products to marine and other industrial industries. Contact him at [email protected] T: 919-940-0546 / W: totalbiosolution.com
(As published in the March 2016 edition of Marine News - http://magazines.marinelink.com/Magazines/MarineNews/201603)
Read Galley Grease Harms Equipment – and the Environment in Pdf, Flash or Html5 edition of March 2016 Marine News