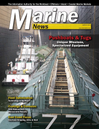
The (Updated) Responsible Carrier Program
By Capt. Katharine Sweeney
A primer: (...and please don’t shoot the messenger)
Last summer, the United States Coast Guard (USCG) announced its intent to accept the American Waterway Operators (AWO) Responsible Carrier Program (RCP) as an acceptable Towing Safety Management System (TSMS) under pending Subchapter M regulations. The acceptance did not come without some major changes to the RCP, changes that were needed to ensure the RCP would meet USCG requirements and become a viable option for operators once new Subchapter M regulations take effect. When that happens is anyone’s guess.
At the AWO Safety Conference in New Orleans in February, the USCG stated their preferred method was for companies to have an audited TSMS in place with the continual improvement aspect of the company’s operation and maintenance of the company’s vessels an audited TSMS brings. Further, the USCG did not want the “USCG Option” available to operators. They also admitted that two years after publication of Sub M, only 25 percent of the current uninspected fleet will have been audited. There will be growing pains, but the Coast Guard remains committed to working with companies to work out the kinks.
RCP Modifications
The modifications are extensive. It is very important to realize all of these changes were the result of input from the USCG and the AWO partnership to ensure all requirements for approval as a TSMS were met. Beyond this, these changes were not proposed by the facilitator of the RCP, the Towing Vessel Inspection Bureau (TVIB). The revised worksheets for both the RCP Management Audit and the RCP Vessel Worksheet were approved by the AWO and are available to download from the TVIB website. Any concern over these changes should therefore not be directed at the TVIB. As Cathy Hammond, immediate past President of the TVIB implored, “Don’t shoot the messenger.”
If you performed internal audits last year of both your offices and vessels, then your document control procedures should have required you to use the most recent version of the RCP checklist or worksheet. If that was the case, then you are ahead of the game, as some of the changes to the management worksheet were already underway. Your procedure for control of records hopefully required you to keep this documentation as it will be of interest at external (RCP initial or renewal) audit time. This year, all vessels will need to be internally audited utilizing 100 percent of the worksheet or whatever internal auditing tool your company develops.
No longer is it sufficient to audit each vessel utilizing a portion of the RCP, merely ensuring 100 percent of the RCP is covered by your fleet at large. Each vessel is required to be audited completely, utilizing all elements of the RCP vessel worksheet. These audits need to happen every 12 months, but unlike the ISM code, the anniversary of when the audit is required for each vessel can remain the same, provided the audit is completed in the three month window prior to the audit anniversary date. Originally when the ISM came out, only periodic internal audits were required. In 2010, the wording was changed to ‘at least every 12 months.’ It is also assumed, that it is a metric of the company’s management system as to the ability to conduct thorough internal audits in a timely fashion. Meaning, that if you don’t get it done in 12 months, this could be construed as a sign that your company is not committed to the continual improvement process.
The internal management audits are much the same story. Every year, 100 percent of the RCP management audit worksheet must now be completed, at all offices of your organization that have an input in managing the vessels. These audits must be completely every 12 months, and they can be completed early (up to three months prior to the annual date) and still maintain the original anniversary date. Unlike the ISM code, towboat operators won’t suffer from “certificate creep.”
Your system should further include a policy for internal audits and that a review of the management system is completed as part of the internal audit (or in addition to) and procedures outlining as to what this review will contain at a minimum. Also required are procedures outlining an internal auditor’s minimal educational requirements, training and experience, as well as any other qualifications required and the procedures should clearly dictate the parameters to allow for independence with respect to the assets being audited.
Renewals: 180 vs. 90 Days
Also starting in 2016, the RCP renewal window for recertification had been shortened from 180 days to 90 days. However, 180 days is being allowed for in the recently published AWO ‘frequently asked questions’ guide. It does appear that when you are at the five year (not the previous three year) renewal of your RCP status, the window will shrink to three months prior to the renewal date. You can still have your RCP audit conducted by a TVIB certified RCP auditor 180 days prior to your RCP renewal date (the date listed on the RCP “status” page of the AWO website), and still keep the same renewal date with no “certificate creep,” but next round, it shrinks to 90 days. The requirement to have all non-conformities corrected prior to recertification is still in place. You’ll only have 180 (then 90) days to correct any line items on the worksheet or checklist with which your company is not in compliance. The need for a pre-audit to find these issues prior to your external audit cannot be emphasized enough.
For vessel RCP audits (each vessel must now get audited once every five years) corrective actions resulting from the RCP audit must be resolved with 90 days. In addition, you are only allowed a maximum of 90 days prior to renewal date to commence an audit. Once the audit is completed on a vessel, another audit is due five years later, and can be completed up to 90 days prior to the anniversary. This is one-half as many audits required by the ISM Code. And, if your vessel does not have any other certificates, Class must sign off annually. You may be having ISM external audits more often than that (as often as yearly, in addition to you thorough internal audit).
Vessel nonconformities also now require action within 90 days. It is through this metric that AWO is requiring members to comply with to ensure that management systems are adept and nimble enough to address problems within three, rather than six month time frames.
Avoiding ‘Procedure Churn’
While not implicitly listed in the changes, having effective measures in place to vet any changes to your management system also is incredibly important. ‘Procedure churn’ – for example, issuing a new procedure merely to ensure conformity, only to have the new procedure itself later revised and re-issued – should be avoided at all costs. It makes for a lot of extra work and an unhappy crew. It is better (and less time consuming) to spend a little extra time making sure the procedure fits, rather than ‘churning’ your management system. The first method embodies the whole notion of ‘continual improvement’ with respect to a management system; the second is its antithesis.
RCP Renewal Cycle Phasing into Five Years
Previously, the RCP renewal cycle was every three years. This has now been increased to every five years, with a mid-period RCP external audit to be conducted between Years two and three, or between Months 24 to 36. The requirement is to be phased in over time, based on the company’s current RCP renewal status date. Also, the requirement to have 100 percent of all vessels audited (as opposed to as little as 10 percent) will be phased in over the five year cycle. Equipment in lay-up status will not need to be audited, however, if they are in use just prior to the five year renewal date and have yet to be audited, these vessels will need to be audited prior to the company being issued a renewal certificate. This adds another item to your lay-up checklist: whether or not to have the vessel go through an external RCP audit prior to lay-up.
External Vessel Audits
Previously, the RCP required vessel audits took place in conjunction with the management audit, with 10 percent of all vessels to be audited during the RCP recertification (or initiation) process. Now, whereas every vessel must go through an audit once during the five year process, the vessel audits are no longer a part and parcel element of the management audit. The vessel audit worksheet has been expanded greatly, and includes many of the line items covered during the management audit. This duplicate work is needed as different RCP auditors may be conducting these audits. Moreover, the management audit may have been conducted a year or two before the vessel audit, which requires more evidence of compliance with procedure. Mere documentation of a procedure is no longer enough; proof of compliance is now required. Any finding of non-compliance with the RCP requires 90 days for correction(s) before the external audit is deemed successfully completed.
Designated Person Ashore (DPA) – More Defined, and Playing a Starring Role
Straight out of the ISM (International Safety Management) Code, the DPA must be an integral part of your management system. A DPA’s minimum educational requirements, training and education, and other qualifications must be clearly documented as well as his or her independence (from the chain of command) and access to top level management. Strictly speaking, your port captain cannot be a DPA. The DPA needs to be a person outside of the fleet management structure and one able to effect change, if needed, for issues regarding safety of the crew and/or vessel, and of the environment. Any crewmember who feels that a safety concern is not being addressed can reach out to the DPA who will then listen to their concern, investigate its merits, and find a solution if needed. The DPA also must have access to resources to implement a solution or plan when warranted.
Personnel need to understand who this person is, his or her purpose and why they might contact this individual. The contact information should be posted on all vessels and in all offices. Resources necessary for this person to perform his or her job as DPA cannot be withheld. In fact, failure to have a designated DPA is a show stopper; it effectively negates the whole system. From a legal perspective, lack of a performing DPA is the equivalent of handing a blank check to a plaintiff. Imagine having an employee that reports an unsafe condition on a vessel to the company’s DPA, but without any follow-up from said DPA, followed by a later injury or circumstance related to the condition that gives rise to a claim. A potentially bad situation has developed into a far worse one, both morally and legally.
Mission Statement: Clear, Concise and Easy to Remember
Myriad other items also need to be included in your management system. Each of these items could be the subject of a valuable article, in and of itself. Lastly, when reviewing you management plan, make sure your company’s overall mission statement is short, clear, and easy to remember; the fewer words, the better. Everyone on board should have a clear understanding as to the company’s principal goals. Ultimately, that’s the route to becoming a Responsible Carrier.
Captain Katharine Sweeney is CEO of Compliance Maritime, provider of independent internal auditing of security, safety, quality and environmental management systems for vessel operators. Captain Sweeney is an experienced Master Mariner, safety expert and federally licensed pilot with over 25 years in the maritime industry. Contact her at [email protected]
(As published in the March 2016 edition of Marine News - http://magazines.marinelink.com/Magazines/MarineNews/201603)
Read The (Updated) Responsible Carrier Program in Pdf, Flash or Html5 edition of March 2016 Marine News