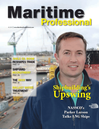
Page 38: of Maritime Logistics Professional Magazine (Q4 2013)
Shipbuilding, Repair
Read this page in Pdf, Flash or Html5 edition of Q4 2013 Maritime Logistics Professional Magazine
AKER PHILADELPHIA SHIPYARD rea. Nevertheless, it was clear that Aker mostly closely aligns itself with a more European model.Locally, the Aker shipyard has a very European feel to its atmosphere. This extends from the style of furniture in the reconverted ofÞ ce spaces to the distinct Norwegian accents that can sometimes be heard in the hallways. A small percent- age of AkerÕs approximate 1,200 employees are in fact from Europe. Rokke declined to quantify that number, but it was clear that these involved management visas and the process of taking lessons learned from both European shipyards as well as its own Norwegian parent. And, he added, ÒWe have also learned a great deal from our sister companies, both in the marine and oil and gas sectors.Ó Aker Solutions, for example, has deep marine roots.ÒWe have put a high emphasis on harnessing best practices from other shipyards around the world since our start-up. For example, in 2005 we pioneered a partnership with the Korean shipbuilding industry which we continue to reÞ ne and develop today.Ó Aker, he said, emulates some aspects of German auto- mation and parts marking. He added, ÒWe have invested over $400 million in our facilities from the beginning. It starts with an efÞ cient shipyard set up and layout to optimize shipbuild- ing processes, work ß ow and material logistics. We melded best practices from many shipyards and ended up with a world class facility that weÕre proud of.Ó Asked about improvements in efÞ ciency achieved over time involving the economy of scale afforded by repeat, series- build experience, Rokke again declined to be speciÞ c, saying only, ÒWe have gone from delivering one ship annually to our present capability of producing three annually in a relatively short time period.Ó RokkeÕs bottom line is simple: come 2018, Aker will be proven across multiple ship classes. At that point, he says, business should take care of itself. That remains to be seen.At Aker, best practices also extend to giving virtually 90 percent of all shipyard employees off during the holidays (26-31 December), something which Aker says allows them to do necessary equipment maintenance and upgrades. It also makes for a happier shipyard worker. Jeffrey Theisen, the Þ rmÕs Chief Financial OfÞ cer, told MarPro that Aker had in- vested as much as $350 million in its workforce, including training. All steel work is done in-house, with multiple plasma cutters and heavy assembly lines. Today, Aker can build ves- sels up to 116,000 tons DWT and 43 meters beam. Finally, and with regard to the joint venture and proÞ t shar- ing hulls, we asked Aker if these close relationships created extra incentives to do a better job and perhaps, a more moti- vated shipyard employee. Aker executives deny that this is the case, saying that their workforce does the same job on every single hull and regardless of the terms of the deal. And, while it shouldnÕt make a difference, it probably does. Especially when people know that the hull they are working on might be leaving the yard, but it wonÕt leave the bottom line. ThatÕs not a bad thing. The Rally: Sustainable or Cyclical?The U.S. Department of Transportation recently said that 15 commercial tankers are on order or under construction at the Hull NumberClient Type / DWT Delivery 19SeaRiverAframax Tanker / 115,000 Q2 - 201420SeaRiverAframax Tanker / 115,000 Q4 - 201421CrowleyProduct Tanker / 50,000 Q3 ? 201522CrowleyProduct Tanker / 50,000 Q4 ? 201523CrowleyProduct Tanker / 50,000 Q2 ? 201624CrowleyProduct Tanker / 50,000 Q3 ? 201625 ? 28CrowleyProduct Tanker / 50,000 (*) OPTIONS ?29MatsonContainership / 3600 TEUQ3 - 201830MatsonContainership / 3600 TEUQ4 - 2018Aker Philadelphia Newbuilding Backlog ? November 2013 38 | Maritime Professional | 4Q 2013MP #4 34-49.indd 38MP #4 34-49.indd 3812/11/2013 1:24:45 PM12/11/2013 1:24:45 PM