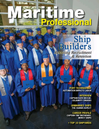
Page 39: of Maritime Logistics Professional Magazine (Q3 2015)
Read this page in Pdf, Flash or Html5 edition of Q3 2015 Maritime Logistics Professional Magazine
An aging workforce can translate into the loss of is aging and we need to ? nd a way to better brand our industry accrued knowledge. Is your organization using for the future generation of workers. technology and e-methods to capture and retain those skills and cumulative knowledge? Arold de Vries: We have 32 shipyards and 13 other type
Arold de Vries: The ship-building industry in Holland had a of operations. The biggest challenge for us is to produce top huge peak in the 1970’s and 1980’s and all those young people quality products at the lowest possible cost. We think we have who joined the company back then are now 50 or 60 years a nice product but competitors are not stupid. They make simi- old. So, we are aware of this and trying many things. First, the lar products and try to do it cheaper. So, we have to bring the retirement age in the Netherlands has gone up and people are costs down and keep the quality at a high level.
staying on a bit longer. We’re trying to keep everybody healthy.
And, we’re trying to transfer the knowledge. That happens at What one thing do all of your employees agree is a couple of levels. The most important thing is that we train the one critical requirement (bene? t / salary / train- some of the traditionally focused workers into being mentors ing, etc.) of their employment at your ? rm?
and coaches so that they actually assist the new generation in Don Keeler: There is no one critical element. Across the being successful. We’re not looking to just tell people how to board, Austal provides competitive compensation and bene? ts do things, but instead, transfer knowledge in a bit more modern reducing an employee’s motivation to leave for better pay or way. And, on paper, it looks very nice but we found out that bene? ts. We are also a company that cares about its people in practice, it didn’t work. So we’re now into a huge training and offers opportunities for employees to be involved in work program where we make sure the older more mature people actually have the tools to transfer the knowledge.
Sue Haley: We provide on-the-job training, and we use our more experienced craftsmen to mentor and train. We also se- lect some Vigor employees to serve as lead teachers for the training centers. With respect to developing our leadership tal- ent, we have those graduating from our leadership programs assist with teaching the next class of leaders.
Don Keeler: We use our subject matter experts to assist with development of training programs and curricula, to sup- port continuous improvement of advanced shipbuilding and manufacturing and to mentor our workforce.
What is the biggest challenge for your shipyard in today’s business environment? Why?
Sue Haley: As we’ve grown and taken on ever more com- plex projects, the biggest challenge is to ensure that our orga- nization evolves fast enough to meet customer demands. This means not only identifying and ? lling skill gaps at every level but also making sure we identify and accelerate the growth of our next-generation leaders so they can help us promote the change that will be needed.
Don Keeler: Austal’s biggest challenge is the ability to se- cure and retain highly skilled shipbuilders and to increase the awareness of the opportunities in the maritime industry. Why?
The industry has been volatile for the last few decades, we continue to lose shipbuilders to other industries, the workforce www.maritimeprofessional.com Maritime Professional 39| | 34-49 Q3 MP2015.indd 39 9/18/2015 10:03:24 AM