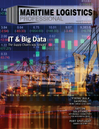
Page 56: of Maritime Logistics Professional Magazine (Mar/Apr 2018)
IT & Software
Read this page in Pdf, Flash or Html5 edition of Mar/Apr 2018 Maritime Logistics Professional Magazine
IT & SOFTWARE
We help people build ships. We help them monitor the performance of the ships; before and as they are being built. What we saw with one of our customers – Seaspan – during one project, there were about 30,000 e-mails going back and forth just to fgure out and follow up on that type of thing.
And, while we continue to build and deploy software for shipping companies, we realized that all of the ‘good stuf’ was actually contained in an e-mail.” – Bill Dobie, Founder and CEO of SEDNA world's major shipping lines with alternatives to vessel owner- a single project, it is more ideal when the whole team knows ship by offering long-term leases on large, modern container- the status. We’re not dealing with dollar signs; usually, we’re ships combined with industry leading ship management ser- dealing with real issues on real ships. SEDNA allows you to vices. A global operation, Seaspan employs more than 4000 know what’s important – time and action – instead of having people on shore and at sea. Three years ago, they turned to to sift through a mountain of E-mail, one by one.” At the same
SEDNA as a way to better organize certain aspects of their time, senior staff often don’t need to be involved in the day- transactional business. Since then, they haven’t looked back. to-day minutia; they can collect that information and then fnd
According to Ian Robinson, Director, Projects and Technol- what they need, when they want it.
ogy at Seaspan Ship Management Ltd., the software wasn’t For the shipbuilding aspect of Robinson’s day-to-day rou- originally rolled out in one fash. “We had teams all around tine, SEDNA has introduced a level of organization and docu- the world so it was a case of building it, team by team. And we mentation that is invaluable. “Sometimes, we’ll have teams built it out for sub-teams, so it started with a defnite central imbedded into a shipyard for more than one year. It might be a plan, and over time, we found more uses and functionality series of ships; sister vessels. And often times, the problem we for it. It’s quite mature now in our organization, but it’s taken might have in one ship, probably will impact the other nine,” about two years to get it set up with the teams the way we he explains, adding, “It’s about having common information wanted it to.” and you realize you don’t have to reinvent the wheel to start
For Robinson and Seaspan, SEDNA is a supplement to his the next vessel that might be getting the keel laid a month apart existing E-mail platform. “I’ll qualify that,” he explains, adding from another. If you have a group e-mail address, then the in- quickly, “For me, it’s a supplement. I have Outlook to deal with formation available for one ship is also available for all ten.” management in the company and more personal, one-to-one Benchmarking what SEDNA has saved his department stuff. Tasks involving things like HR we still approach in the overtime is diffcult, says Robinson. As an example, howev- old-fashioned Outlook way. But, if you are talking about teams, er, Robinson points to specifc transactional advantages that groups or project-based tasks, then it’s defnitely SEDNA.” SEDNA can bring. “SEDNA remembers the issue that we had
Also according to Robinson, when Seaspan teams are deal- with the main engine on the frst ship in a series, so when the ing with the same vessel or the construction of the vessel, ffth ship comes along, we have that knowledge to prevent it one of the things that SEDNA handles very well is guarantee or shorten the pain, even when there is turnover of personnel claims – where you might, for example – be dealing with a over a fve year period (yours and that of the shipyard). All series of issues all under one contract. “With Outlook, you the notes are saved and in one place. The knowledge base is get people sending to people that they think are involved, or there; you can look back and fnd why you made that decision. might not be involved, so pretty quickly, the information is out The shipyard might want to push an extra cost on you, where there, but it becomes fragmented. When you are dealing with prior to that, it was a standard cost and procedure. Or perhaps, 56 Maritime Logistics Professional March/April 2018 | |