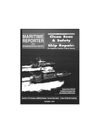
Page 35: of Maritime Reporter Magazine (October 1995)
Read this page in Pdf, Flash or Html5 edition of October 1995 Maritime Reporter Magazine
50 degrees F to cure
Catalyzed:
Toughness and durability, extended maintenance painting intervals
Epoxies:
Slow cure below 50 degrees F
Vinyls, vinyl/acrylics, chlorinated rubbers:
Fast dry, excellent inter-coat adhesion, low temp, cure
Silicone alkyds:
Excellent color and gloss retention, poor low temp, cure
Polyurethanes:
Excellent color and gloss retention
All of the coating types shown above are impacted to varying degrees by environmental health and safety regulations.
Compliance of many types of coatings for use in topside environments has been accomplished.
Performance Criteria • Cargo Specific • Intermittent Wet & Dry
Protective coating systems for tanks ore cargo-specific. Coat- ing system selection is also determined by method and degree of surface preparation achievable, current surface condition, and economics. Proper surface preparation is critical if satisfactory coating performance is to be achieved within a storage or ballast tank environment. A wide variety of protective coatings have been employed in the coatings of tanks on ships, including: catalyzed epoxies, coal tar (vinyls), coal tar epoxies, etc. Coatings for potable water storage tanks must be approved by the National Sanitation
Foundation and be listed in NSF Standards 60/61.
Economic and regulatory considerations are driving the development of high performance coating for ballast tanks and other areas that are difficult to protect and maintain.
Significant monetary savings will be realized by the enhance- ment of coating performance and the extension of mainte- nance painting intervals in tank environments.
BILGE AREA
Performance Criteria • Corrosion Resistance • Salt Water Immersion (intermittent wet and dry) • Chemical Resistance
Bilge areas require high performance coatings due to the aggressiveness of the environment. Protective coatings used in new construction bilge areas should be high performance materials applied over the best degree of surface preparation achievable. Phenolic epoxies, epoxy amines, and mastic epoxies are representative of coating types used in bilge areas. Volatile organic compounds are generally low in the high-solids, high-build epoxies selected for bilge areas.
Hazardous air pollutants and materials such as crystalline silica may require reduction or elimination depending on the specific products and levels of objectionable material.
MACHINERY & INTERSPACE
Performance Criteria • Corrosion Resistance • Color and Gloss Retention (exterior surfaces only) • Adhesion with Minimal Surface Preparation • Ease of Application
Machinery and interspace areas are generally top-coated with an alkyd coating preceded by a vinyl wash primer and/ or an alkyd anti-corrosive primer (note: alkyds should not be used over zinc-coated or galvanized surfaces). Exterior machinery frequently receives a silicone alkyd topcoat to provide long term color and gloss retention. High tempera- ture machinery is usually cooted with a heat resistant coating such as a silicone aluminum. M^yi primers and enamels have required extensive reformulation to comply with VOC and hazardous material regulations.
Marine Coating Technology
Compliance with environmental regulations and improvements in marine coating performance can-
October, 1995 not be accomplished completely by modification and tweaking of exist- ing products. As with any technol- ogy, research into new and improved products is the way to create a better future. In the area of indus- trial and marine coatings, technical advancements will come not only from the research and development laboratory, but from successful transfer of coating technology in related industries to solve marine coating problems. Many of the new high solids and waterborne tech- nologies will not resemble conven- tional materials with respect to application, performance, and maintenance. Therefore, a learn- ing curve will be required to opti- mize the use of these coatings. The coating technologies discussed in the following paragraphs range from budding new coatings that are truly the result of innovative work by coating manufacturers and their raw material suppliers, to tech- nologies that have existed for some time, but have not been used in marine coating work. This listing is by no means all inclusive, but rather a sampling of areas worthy of con- sideration. • Polyurea Elastomeric Coatings:
Polyurea has been used for some time as a reaction injection molded (RIM) plastic, but only recently has
Circle 239 on Reader Service Card 37
Large or small, floating or fixed,
Seaward SEA GUARD* fenders cover you from the tropics to the arctic. Seaward
International brings to fender technology the same rigorous quality control and attention to detail we put into all our marine products. From the 2x4' to the tanker-scaled 12x24', all our fenders meet the most stringent quality and perfor- mance standards.
The SEA GUARD fender combines quality assurance standards with new elastomer technologies such as a reinforced skin, making it the answer to most fender sys- tem requirements.
Ihe first of its kind 20 years ago, the
Seaward foam-filled fender maintains its record of reliability. And we continue to develop and supply the protective marine technologies that keep you on course. All our products tell the same story: Seaward is committed to safeguarding your peace of mind.
Structures, ships, environments, bud- gets: We protect it all.
SEAWARD
INTERNATIONAL, INC. 3470 Martinsburg Pike, P.O. Box 98
Clearbrook, VA 22624-0098 1-800-828-5360 (703)667-5191
Fax: (703) 667-7987
SEE US AT AAPA, BOOTH #63 & 64
AND ASCE, BOOTH #35 & 36.
SEA GUARD® Is a registered trademark of the Chem Ray-SEAGUARD
Corporation. Used under license by SEAWARD International. Inc