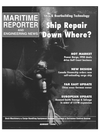
Page 29: of Maritime Reporter Magazine (August 1996)
Read this page in Pdf, Flash or Html5 edition of August 1996 Maritime Reporter Magazine
compensated for by the reduced cost and maintenance of an inter- nal belt. The transfer system is able to achieve a steady 2,000 tons/hour offload speed.
Bottlenecking at the transfer point is always a worry during offload- ing.
To facilitate smooth operation, infrared cameras located in the tunnel and at all transfer points, including the end of the boom, allow operators to monitor belt loading conditions from the pilot- house.
By eliminating shutdowns due to receiving hopper overfills, jammed products, or belt overloads, the sys- tem is designed to easily match the receiving capabilities of most ports. Mr. Sridhar estimates the improved delivery system will save valuable time in port, and, accord- ing to Mr. Jones, the system will "enable the crew to focus on system maintenance instead of operation."
Delivery system
Another new design feature, a 250-ft. (76-m) telescoping boom at midship, capable of 270 degree rotation, is designed to allow for greater flexibility in delivering cargo to onshore hoppers. A hydraulic actuator slews the boom.
Siemens produced a design in which the actuator remains sta- tionary while the boom rotates, propeller-style. The luffing, slew- ing and shuttling action of the boom are all hydraulically con- trolled.
According to Mr. Sridhar, "The biggest challenge of this job is the hydraulics. For hydraulics to work we need the electrical, because it all requires a 20-milliamp control signal, and that's what Siemens controls." The two companies worked closely on the control phi- losophy. Seabulk set forth the sys- tem requirements and Siemens developed the hardware and soft- ware utilizing PLC technology.
Environmental improvements
As more urban ports deny dock- ing permission to bulk carriers due to dust and noise pollution, CSL wanted a system that would elimi- nate these restrictions. To ensure these requirements, Seabulk replaced the standard open-lattice boom with a completely enclosed boom system to contain airborne pollutants. Even the belts within the body of the ship are covered to reduce dust in the internal envi- ronment. Additional dust extrac- tion equipment is integrated into the system throughout the ship, improving air quality for crew members.
Vibration damping on all the dri- ves helps with noise suppression.
The boom chute has a lining of sand between the inner and outer walls for additional noise abate- ment. An indirect benefit of care- ful regulation of product flow is that by eliminating overflows, pol- lution from spilled product is no longer a problem. With these safe- guards in place, these vessels will reportedly be able to unload in any port, even congested urban loca-
August, 1996 tions, without dust or noise.
Selling the idea
Mr. Sridhar presented his design to CSL International in
Boston. To prove it would work,
Seabulk built a $850,000, full-size prototype consisting of one com- plete cargo hold/hopper and con- veyor. They tested gypsum in the prototype and were able to demon- strate the 2,000 tons per hour flow rate.
CSL has purchased exclusive rights to the design for a four-year period. It currently has three ships underway at the Jiangnan
Shipyard in Shanghai, China. Two of these vessels are for CSL
International, and the third is for
Egon Oldendorf.
The Seabulk engineer onsite dur- ing construction, which is sched- uled to begin in October, will be
Brian Carefoot. Seabulk subcon- tracted the fabrication of the boom and the feeder gates back to
Jiangnan.
Other vendors include Siemens, supplying the electrical control system; Flenders, supplying the gearbox and reducers; Continental
Conveyors of Toronto, Ontario, in its first marine project, supplying idlers and pulleys; Fox Fluid Bar of
Toronto supplying the hydraulic actuator; and the Walz & Krenser firm in Rochester, N.Y., designing and supplying watertight doors.
The unnamed vessel's first cus- tomer is New England Power. It will carry coal to New York in the spring of 1998.
YOU'D BE HARD-PRESSED
TORNDA BEnER FENDER.
REALLY HARD-PRESSED.
Large or small, floating or fixed,
Seaward SEA GUARD* fenders cover you from the tropics to the arctic. Seaward
International brings to fender technology the same rigorous quality control and attention to detail we put into all our marine products. From the 2'x4' to the tanker-scaled 12x24', all our fenders meet the most stringent quality and perfor- mance standards.
The SEA GUARD fender combines quality assurance standards with new elastomer technologies such as a reinforced skin, making it the answer to most fender sys- tem requirements.
The first of its kind 20 years ago, the
Seaward foam-filled fender maintains its record of reliability. And we continue to develop and supply the protective marine technologies that keep you on course. All our products tell the same story: Seaward is committed to safeguarding your peace of mind.
Structures, ships, environments, bud- gets: We protect it all.
SEAWARD
INTERNATIONAL, INC. 3470 Martinsburg Pike, P.O. Box 98
Qearbrook, VA 226240098 USA 1-800328-5360 (540)667-5191 . Fax:(540)667-7987
SEA GUARD" Is a registered trademark of the Chetn Ray-SEAGUARD
Corporation. Used under license by SEAWARD International, Inc. 31 Circle 287 on Reader Service Card