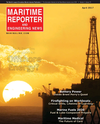
The (Battery) Power Play
By William Stoichevski
Brent Perry [Founder & MD, PBES] & "The Wealth Factory"
This is historic, we tell ourselves, as PBES founder Brent Perry walks us around his still labor-intensive “battery factory” in the heart of Norway, from where ship owner capital controls half of the world’s offshore tonnage. Perry, a shipbuilder himself, has chosen to house his first production center here in the haunt of another ship builder, Selfa Arctic, whose move north left for Perry a young cadre of college-educated workers.
They’ll build PBES’s stackable configurations of batteries that do not catch fire. Lithium cells’ penchant for catching fire or going into meltdown — so-called thermal runaway — has been the bane of an industry, as it struggles to produce a set that withstands the rigors of actual marine use. European environmental authority tests of “leading” designs showed they were not. Only Perry’s solution — steeped in decades of energy storage thinking from Western Canada’s lithium battery brain trust — has shown bankable and insurable safety, power management and surplus horsepower.
Industry Firsts
“This is a front plate,” Perry says, gripping the shell and circuit board that’ll hold the brains of a cell module. Inside, 24 cells are kept as cool at 15 degrees Celsius by specially engineered coolant channels and a heat-exchanging material layer. “Lithium batteries — although they have extraordinary performance capacity — are very temperature-sensitive beasts. Most of the world today produces air-cooled batteries that live in reality an average 40 to 50 percent of their predicted lifespan because you have no control of the ambient temperature that you’re working in. Every time you go over 30o C, you start to seriously erode it.” The heat-removal quality of the PBES systems allow a 100-megawatt-hour storage system to provide 300 MW of power.
Many of the battery’s components are sourced locally, like so much of this made-in-Norway plant. A new ‘Made in Norway’ brand based on Canuck lithium thinking is Oslo’s own very recent idea, proclaimed aloud by Prime Minister Erna Solberg herself. Looking around, an assembly line of box-covered palettes, tables and busy young men is just discernible. There’s space to grow. There are rows of metal shelves and crates ready to ship. There’s a cluster of battery modules being tested.
Producing this way means Perry’s spending “five-times as much” as he will be when his ordered automation arrives, but he’s happy to employ local skills put out of work by the offshore downturn. “They’re almost all college educated on some level. We like the guys. I like boat builders.”
Lucrative Growth
Perry’s “capacity of capacity” stands at 43 megawatt hours of energy storage systems (batteries plus intel). “With this set up alone we’ll be able to deliver about 120 MWh,” he says. Steady business is already ratcheting up, so he’ll have to produce. His partner-clients — system operators like Siemens and ABB — are well established in Trondheim and along Norway’s west coast. “They’re just down the road” and they’re also key movers in Oslo’s plan to electrify several dozen ferry crossings with all-battery and hybrid vessels.
“We’re full on business right now until end-of-June,” Perry says, adding, “I expect that in the next few weeks we’ll bring in enough contracts to keep us busy into 2018. We still have the ability to run this on two shifts and double our capacity.” In square feet per dollar, Perry admits it’s as effective a business “as a software company”. He’s producing 1 MWh every week, and with what he has he can produce 4,000 batteries a year.
“Everything coming out of Norway until the end of the year is going to be marine,” Perry says, although word is he’s just secured an energy storage contract for a major wind farm. Batteries destined for a two-ship order from 2016 are some of what we see. In a couple of weeks, the order for a ferry company will be assembled and tested. There are 80 to 90 batteries aboard a typical ferry, but Perry’s already ramped up from zero to 30 cell modules a day in just a few months. With his easygoing manner, it’s easy to forget Perry founded the first megawatt-scale marine battery company in the world in Corvus, and that he helped grow it into a serious marine industry player in just four years. He remembers how early in his entrepreneurial life, as now, conservative boat owners were resistant to change. “The payback was all about saving fuel money,” he recalls telling them. Payback in less than five years is a message Norwegian vessel owners, operators and propulsion engineers understand immediately from their contact
with Perry. For his and his clients’ clients, there’s a powerful sales point — a way for them to earn.
Little Things
He used the same arguments in Australia, where he used to talk tugboats. “Tugs are fun because they’re a great place to demonstrate just how powerful a battery is, where a 500-horsepower battery produces 5,000 horse … that is some interesting power.” In Norway, he doesn’t sell directly to the market, just to the end distributors who understand that his “smart” battery systems “talk to each other” and really are “the Internet of things”. They see they can get the voltage they need by ordering the right number of cell modules and that they can get exponential power, safely, because the storage systems remove heat more efficiently that chemistry can build it up.
They get that the front plate assembly Perry’s holding is equipped with a breaker rather than the industry standard fuse because it protects battery and DC buss from damaging each other. “We’re the only company I know of that are actually using breakers on the battery.” Apart from winning over engineers among his clients, his service mind drives a quality focus that’s evident in detail like the touch screen “for managing and observing” cell states in the storage system; the battery module’s simple disconnect rather than pricy power lock to open a module. “We have execution capabilities to match anybody else’s, but we do think a little bit more like mechanics in terms of how to make things friendlier technically.”
Customer Payback
A special orange insulator wrap protects the metal of the cell carrier from any current coming out of the cell itself. It’s more of the detail system integrators inspect in their pre-audits of his factory processes. In fact, it’s the details that make the PBES system work.
The company colors of one module we see are Siemens’, but Rolls-Royce is understood to also have been by to audit his plant. From the system integrators’ point-of-view, the battery systems represent most of the CAPEX in projects they’re pitching their clients. “We’re an intel-inside business. Intel inside, B2B,” Perry explains. “They get a price and they turn around and package it out and sell it the way they want to.”
His customers come to see the tests of their orders before they ship, and we see a 700 volt system being tested for high and low peak power. “It’s way cheaper to find a problem here than to find it out in the field,” Perry says. Onboard a vessel, or under factory testing, an orange and yellow meter shows whether a system is being fired up or whether it’s in shut-down sequence. “There’s nowhere you can’t acquire and monitor data,” Perry says about the factory, installed systems, the production chain and his own supply chain. While his plant will soon have in place the monitors, bar code devices and other tools of cutting-edge, lean production, the storage solutions themselves are all traceable. Barcoding and data structures allow PBES to pinpoint the slightest failure to a plant, process, component and country.
“We monitor these systems 24/7. If we see a slight variation in voltage, we know it before the customer does. We are very proactive in maintenance and service and support, and so we can give a much better warranty because we always have eyes on the system. This energy storage system is a wireless hub. This is the Internet of Things. We can dial into these from anywhere in the world and fix something, change programming, update software. We don’t have to be on the boat.”
The batteries and their two to four millimeters of armor casing have survived vibration tests that would kill a man, making the PBES solution “The Sherman tank of batteries”.
Replacing the battery room with the battery has also cut “by 90 percent” the space aboard ship that needs fire protection and extra ventilation. The battery has its own extraction system for gases like hydrogen and nitrogen.
“It’s all approved and validated by type approval agencies and insurance companies. We’re the only ones in the world who do that. These are all Class projects,” Perry says. After all, he did help write Class’s rules on energy storage.
(As published in the April edition of Maritime Reporter & Engineering News)
Read The (Battery) Power Play in Pdf, Flash or Html5 edition of April 2017 Maritime Reporter
Other stories from April 2017 issue
Content
- Lines in the Water page: 12
- New Horizons: Cruise Industry Challenges & Solutions for 2017 page: 14
- Firefighting on Workboats page: 16
- Op/Ed: CBP’S Lawful Jones Act Revocation page: 20
- IMO 2020: The Future of Fuel page: 22
- The (Battery) Power Play page: 26
- A Rising Sun of Change page: 32
- TUMSAT: More than a Rowing School page: 40
- Updated Forecast: Floating Production System Orders page: 42
- CFD Simulation of a Fully Featured Offshore Platform Model page: 44
- The Future (of Maritime) Care page: 48