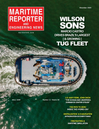
Wilson Sons: Inside Brazil’s Workboat Goliath
Wilson Sons is the largest integrated port and maritime logistics operator in Brazil, operating more than 80 workboats. Marcio Castro, Executive Director Tugboat Division, discusses with Maritime Reporter the size, shape & technical direction of the fleet.
- Mr. Castro, to start, how did you come to a career in maritime?
I graduated in System Engineering at Rio de Janeiro State University (UERJ), I also have an MBA in Business Administration (Coppead/UFRJ). I joined Wilson Sons in 2003, starting a long career, with many positions as System Development Coordinator, Project Manager, Rio de Janeiro Branch Manager, São Paulo & Parana Regional Manager, Operation Director. Currently, I am the Executive Director of the Towage Business.
- I’m sure many of our readers know the Wilson Sons name, but please give an overview of the company as a whole.
Wilson Sons is the largest integrated port and maritime logistics operator in Brazil and offers supply chain solutions based on experience gathered over 180 years. The company is made up of various segments. It manages two container terminals, one in the port of Salvador (Tecon Salvador) and one in the port of Rio Grande (Tecon Rio Grande). It also has 80 tugboats, the largest fleet in Brazil, 23 offshore support vessels, two offshore support bases (Rio and Niterói), dry ports and logistics centers (Santo André and Suape), two shipyards in Guarujá (SP) and one of the largest independent maritime agencies in the country. Allink is one of the largest and most respected companies specialized in ocean freight LCL consolidation cargo and also the only neutral air consolidator in Brazil.
- How is Wilson Sons investing in its Tugboat fleet/division today?
We have just started the building project of six escort tugs with 80 TBP. These new tugboats will help us in our fleet renewal, to serve our customers large vessels that will start calling Brazilian ports. We will also be ready for new opportunities that can arise in projects of new terminals, LNG Operations, dedicated terminal towage and for the oil & gas industry.
We are also investing in new technologies that can improve the efficiency of our operation, like AI in Tug Dispatching. The use of all the data that we have been storing since we launched our Operation Center, will be our focus, either to improve the efficiency of internal processes or to launch new products for the portfolio of our group. To achieve this, our fleet is getting fully connected allowing us to gather all the data our Tugboats can produce during the operations.
“We have a close relationship with our shipyard ... and with Damen, who help us a lot with its projects and its long experience as a ship builder. Damen knows everything about equipment and new technologies being used/launched globally and plays an important role offering the best solution to be implemented.”
Marcio Castro, Wilson Sons
- Are there any other current boat newbuild projects, either recently completed, ongoing, or planned for the near future?
We have just finished the delivery of a series of 14 tugboats. The last units were two 3212 Damen Project that reached 90 TBP, making them the most powerful tugboats operating in Brazilian Ports. All were built in our own shipyard located in Guarujá (left margin of Santos Port).
And we are now starting a new cycle of new buildings. As mentioned, we will be delivering six new tugboats from Q1 2022 until the end of 2024. All Damen 2513 projects, 80 TBP with Escort Tug notation. These tugboats will be IMO Tier III compliant, the very first in Brazil with this European pattern, aiming to attend some customers’ requirements and in line with Wilson Sons Group target on emissions’ reduction.
- Can you give an overview of how Wilson Sons Tugboat Division examines, trials and selects technologies to retrofit on existing boats or incorporate into new boats.
We, as a tug operator, have a close relationship with our shipyard, responsible for building our vessels, and with Damen, who help us a lot with its projects and its long experience as a ship builder. Whenever we have to take a decision on implementing modifications, or the details of new buildings, we have in our opinion, the best team to help us. Damen knows everything about equipment and new technologies being used/launched globally and plays an important role offering the best solution to be implemented.
Our shipyard, on their side, confirm if the implementation is feasible considering Brazilian Port characteristics. With a collaborative process, between these three parties, we can reach the best solution that meets the requirements of all the stakeholders of our industry, crews, clients, pilots, port and maritime authorities.
Photo: Wilson Sons
- Maritime is in a transcendent phase, with sharp focus on reducing emissions. Please discuss marine emissions reduction in the macro, and specifically discuss how it is materially impacting how your fleet is built, operated and maintained.
Despite the fact that the emissions from the shipping industry is a small part of the total, it is important to have this awareness, that we all have to do our best to reduce the impact of our activities on the environment. All the players that are part of the maritime and port industry must work in a collaborative way to find solutions to minimize the emissions specially when they are in the port areas, located in crowded cities.
Wilson Sons, as a member of Brazilian GHG protocol program, is working to find and implement solutions to reduce our emissions for the operating vessels and for new buildings as well. In recent years, we’ve been reducing our emissions working on solutions like COR (Tugboat Operational Centre, from the Portuguese acronym), where we are always seeking efficiency in our fleet. At this moment, we are running three pilot programs with companies offering technologies that promise important reductions in fuel consumption and emissions.
We are also investing in an AI Tug dispatching algorithm that will give us the best location to await the next maneuver, and the right moment and speed to sail to approach the vessel. For the new buildings we decided for IMO tier III complaint tugboats, the same pattern required for European ports. This decision is fully aligned with our clients and the Wilson Sons Group
- In step with emissions is discussion on the “fuel of the future.” Have you/will you experiment with alternative fuels and/or hybrid battery solutions for your fleet?
We are permanently analyzing the solutions that are being developed, to understand how viable they are for our operations. From the supply chain of a fuel in Brazil, to our operations profile, we check all the aspects of implementing these new fuel technologies. Hybrid and Electrical tugs are some examples of projects that we have studied taking into consideration also the Capex and Opex.
- Which solution(s) do you see has the most potential to significantly impact your fleet’s emissions.
Electrical projects would be the best solution in our opinion. But the battery technology must evolve in terms of time for charging and storage, allowing a higher autonomy. With diesel engines we have an autonomy of more than 30 days without refueling, the tugs are ready for operations most of the time, and sail long distances for moving between ports and for vessel assistance. Nowadays, electrical projects are feasible for very specific situations like a dedicated terminal towage with very few maneuvers per day, and plugs for recharging available all the time.
LNG is also a good solution, but we will need to wait for a better supply of the product. In Brazil, we have some small scale LNG projects that are creating a good expectation for our industry. As soon as we have a reliable supply chain, this solution will be on the table for new buildings.
“Autonomy” and “Digitalization” are increasingly discussed as a means to make vessel operations more efficient. How has Wilson Sons invested in ‘digital’ technologies to increase vessel and fleet efficiency.
Since we launched our Operation Center responsible for the tug dispatching we realized that we could use all the data generated to make better decisions in our operation. Ten years later, we are now using all that data to create products adding value to our operation. With our fully connected tugboats, we are now creating a Big Data warehouse with information coming from its equipment to go even further. We aim to be able to reduce the unavailable time of our equipment, and increase efficiency in fuel consumption, and safety.
Besides that, we have reviewed all our operation processes, digitalizing them and eliminating all paper on board. This revolution was promoted by our TugLab, a permanent initiative responsible for identifying, and making use of new technologies to guarantee the competitiveness needed to keep Wilson Sons as a leader in the Brazilian market.
- Do you see “Autonomous Workboats” in Wilson Sons’ future? If so, please explain.
I think that we still have a long journey ahead until we have Autonomous tugboats running in Brazilian ports. As a tug operator, what we sell to our customers safety for their vessels. During a vessel berthing/unberthing, many unpredicted situations may occur. An autonomous tugboat must be extremely tested to react to them, offering a higher safety level to the shipping companies, without adding risk to them, the terminals or port authorities. However, I also think that all technologies on board of autonomous vessels, will be gradually integrated by the current equipment, allowing the crew to test them and take advantage to the efficiency that they can bring to the maneuver. As soon as we have the reliability needed, the autonomy will naturally come.
- When you look at your business today and consider the future, where do you see opportunity, and how are you investing to fulfill that opportunity?
The use of data will be a game changer for the port and maritime business. All the information that flows between all the stakeholders, if duly managed, can create a good environment for all. The Wilson Sons Group wants to play an important role in this new age.
- When you look at regulations – international, national, local – what do you see on the horizon that has the greatest potential impact – positive or negative – on your business?
Environmental regulations have this potential impact. But I think that the big customer requirements on this green agenda will be ahead of these regulations. The private initiatives on reducing indirect emissions will drive all maritime suppliers. And we think that this impact will be positive for Wilson Sons, once we already have many initiatives aligned with this proposal, that may differentiate ourselves from other towage companies.Photo: Wilson Sons
- What do you consider to be your greatest challenge to running a safe, efficient fleet of tugboats?
In our company, as we have countrywide coverage, from North to South, training our team is our main challenge. To make our messages related to Operations, HSE, M&R arrive clearly to more than 700 crew, is something quite complex.
Our strategy to achieve the results in all agendas is to make use of the best channels to communicate directly to each person. The technology has helped us a lot in this, allowing us to make video calls with interactions from both sides, and creating training sessions that can reach all our employees. Even far from them, we want to be present, understanding their difficulties, reinforcing the values of the company, creating the most efficient environment.
Crewing: In many parts of the world, finding and keeping quality crew is a perpetual problem, as the older generation retires and a ‘life on the water’ is not as attractive to the younger generation. What is the situation with your company? Can you give an overview of your cumulative boat crew team, with insights on how you attract, train and retain the quality crew that you need?
Our company is well-known as good for crew members. They come from the Maritime Authority School without any experience and, along the years, have the opportunity to grow and become a Master of a tugboat or a Chief Engineer in Wilson Sons. They come attracted by the good salary we pay, higher than others with the same education degree.
We have a training Center that tests them before joining the company. They are coming onboard with a better background than in the past. So we teach them by adding practical knowledge of HSE, Operations and M&R, the values and culture of the company, and what is expected from a good crew member. In this training center we have a full tugboat simulator, that lets them experience the hardest situations they could face in their daily activities. Giving them growth opportunities, we are naturally retaining them. It is not common to have our crew leaving the company to join a competitor.
- No business discussion can be had today without discussing COVID19. How has the pandemic materially impacted your Tugboat Division Operations?
The company has been closely monitoring the advance of the pandemic reported by the World Health Organization, related to the spread of COVID-19. Our clients are getting dully attended without delays, and our operations continued to occur normally, following some protective measures implemented in all business units. A technical crisis committee was created to manage the actions resulting from this pandemic and established some measures. We’re closely monitoring the evolution of the virus in the country and the development of the situation. The lessons we have learned and many solutions we provided during this pandemic, will be permanently used by our company.
Size & Shape of the Wilson Son’s Tugboat Division
Wilson Sons’ tugboat division has 80 tugboats in its fleet, most built from projects designed by Damen, including:
• 74 ASD + 6 TSKN
• Four Escort Tugs
• 16 equipped with Fire-Fighting 1
• 53 Tugs over 50 TBP
• 10 ready for Ocean Towage
• Mainly Caterpillar Engines
• Kongsberg and Schottel Propellers
• Average age. of 15 years
Photo: Wilson Sons
Read Wilson Sons: Inside Brazil’s Workboat Goliath in Pdf, Flash or Html5 edition of November 2020 Maritime Reporter
Other stories from November 2020 issue
Content
- Engineering Ethics, Seaworthiness and the Right of Clients to Kill Themselves page: 14
- Cavotec, ASKO Power Forward on Autonomous, Zero-Emission Fleet page: 32
- Wilson Sons: Inside Brazil’s Workboat Goliath page: 36
- Addressing the New IMO Guidelines for Second Generation Intact Stability page: 52
- Interview: Rear Admiral John Okon, Commander, Naval Meteorology and Oceanography Command, US Navy page: 70