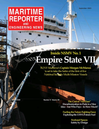
Page 55: of Maritime Reporter Magazine (September 2023)
Marine Design Edition
Read this page in Pdf, Flash or Html5 edition of September 2023 Maritime Reporter Magazine
TECH FOCUS: WELDING everyone involved.
• Weld Design and Sequencing:
Plan out weld sequencing during fab- rication to minimize distortion. Weld design for economical and improved
At E4 POWER LLC, we are dedicated to revolutionizing the marine industry fabrication.
by providing exceptional services and installations for ships, with a focus • Practical Welding Experience on our cutting-edge modular exhaust systems and vibration isolators. As at all Stages of Vessel Design: Practi- proud distributors for SCHIEDEL METALOTERM and TRELLEBORG AVS, cal experience provides a pool of under- our mission is to rede? ne ship exhaust technology, offering solutions that standing to draw from in solving today's are up to 60% lighter than traditional systems while offering unmatched welding challenges. customization possibilities and noise reduction. Our partnership with
SCHIEDEL METALOTERM, a renowned manufacturer of high-quality fully
Theory: Engineering Analysis insulated exhaust systems, ensures that we deliver the latest advancements
As the maritime industry continues to in marine exhaust technology to our clients. Additionally, our collaboration advance, the signi? cance of precision with TRELLEBORG AVS’s cutting-edge noise and vibration reduction welding extends beyond mere joining technologies enhance the comfort and safety on board, creating a quieter of materials. The lifespan, safety, and and more pleasant environment for crew and passengers alike.
operational effectiveness of marine ves- sels are factors explored by professional www.e4powerllc.com [email protected] engineers through technology. EBDG leverages its analysis background to better inform the science of welding, Thermal Analysis service of the structure using structural and thermal Finite Ele- EBDG has used thermal FEA to bet- • Easier for the welder to execute ment Analysis (FEA). ter understand heat input and cooling • Cheaper - in materials or labor or rates for complex weld procedures. A both
Structural Analysis transient thermal analysis can capture • Fewer defects = less rework
Structural analysis using FEA enables the effect of an arc weld traveling along • Reduced time to create a deeper understanding of complex a joint, showing the dynamic thermal loading and structural con? gurations. contours in the material that gives in- Joint Design
EBDG has the capability to quickly sight into the heat affected zone and Metals much thicker than 3/8" (9.5 model the target structure in three di- resulting material microstructure after a mm) typically require some level of mensions, apply design loadings, and joint is completed. This can have a pro- joint preparation to create a complete iterate through structural design. Both found effect on the resulting strength of penetration weld. This type of weld smaller scale and large-scale structures the base material after welding. completely ? lls the joint and is critical can be treated in this manner, from mi- for butt joints in hull plating. The joint nor structural features like mooring bitts Practice: Welding Process Improve- preparation in this situation opens up all the way up to complete hull analyses ments the cross section of the weld and allows of vessels. The heart of a good weld is the pro- the welder to access the "root" of the
The scope of a structural analysis can cess used by the fabricator. These pro- joint and build the connection from the include static structural, modal/vibra- cesses can range from the ad-hoc expe- inside out via multiple weld passes.
tion, and fatigue. Often FEA is used as rience of each individual welder, up to The joint preparation allows for this a forensic tool to ? nd root causes of in- a formally approved weld procedure ac- access by providing a chamfer or other service failures or to design structural cepted by the cognizant class or regula- cutaway on the edge of the adjoining detailing that eliminates failures due tory body. The weld procedure, whether plates. The decision of what type of to fatigue effects. Finding solutions to formal or informal, is the recipe through joint preparation style can have a pro- these issues ultimately saves the opera- which a skilled fabricator can make a found impact on the economics of the tor from expensive down time and re- quality weld. Through this spectrum of weld. Chamfers are easier to create but curring repair bills. practice "where the arc meets the metal" require more weld passes to ? ll the re-
Why keep making the same crack there are opportunities to create "better" sulting gap. repairs year after year when a redesign welds. The de? nition of "better" is proj- J-cut edge preparation needs more ex- of the structural detail could supply de- ect and even joint speci? c: pensive machine tooling but could more cades of trouble-free service? • Higher quality - appropriate to the than pay off through reduced welding www.marinelink.com 55
MR #9 (50-60).indd 55 9/6/2023 5:06:03 PM