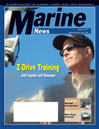
Page 22: of Marine News Magazine (March 2011)
Marine Training & Education Edition
Read this page in Pdf, Flash or Html5 edition of March 2011 Marine News Magazine
22 MN March 2011
MAINTENANCE and it is always best to follow the manufacturer’s recom- mendations for inspection, repair or replacement.
Turbochargers typically last to mid-life on marine engines — about 15,000 hours — but this varies with each engine and application. In engines with closed crankcase breather systems, watch for possible oil and soot contamination of the compressor blades or the charge-air cooler. Buildup on the compressor turbocharger’s blades can slow it down and restrict airflow to the engine, resulting in reduced power and increased fuel consumption. When tur- bochargers do wear out, they are usually replaced rather than rebuilt because rebuilding requires the vessel to be out of service longer.
EXHAUST SYSTEM
During initial engine installation, make sure that the routing of the exhaust system prevents the exhaust from re-entering the engine compartment during operation. If not properly routed, soot can build up on engine room surfaces and clog air filters prematurely. On a regular basis, check for cracks, leaks or corrosion in the entire exhaust system and make necessary repairs.
VALVES AND HEADS
Valves need adjusting periodically to compensate for the wear that occurs in the valve train. In new engines, the amount of adjustment necessary will be higher until the valves seat in. Traditionally, the valve lash has been adjust- ed based on a go, no-go test using a feeler gauge. If a valve clearance was found to be out of compliance, the valve lash was adjusted without ever knowing what the exact amount of wear had been.
Again, here is where trending can help reduce mainte- nance costs. With today’s high costs of labor and down- time, the recommended method is to test early in an engine’s life and actually measure the amount of wear on each lifter and record it. Over time, the operator will accu- mulate a record of how each valve is wearing, allowing a very accurate prediction to be made as to when valves will need to be adjusted in the future.
Trending can also be used to determine wear in cylinder heads. For example, remove a few heads just prior to the recommended change interval to identify any abnormali- ties and to measure and record the distance the valve head has receded into the cylinder heads. Note whether this is more or less than anticipated. By measuring and recording cylinder-head wear, the operator will be able to predict the rate of head wear in that engine and more accurately schedule future maintenance when it is most convenient.
EMISSIONS SYSTEMS
For most marine applications, the emissions system that requires attention is the crankcase ventilation system.
More common on work boats, engines with open crankcase systems all pass some lube oil and combustion gasses into the engine room space, potentially resulting in the plugging of the engine’s air filters. Dirty air filters will lead to higher fuel consumption, higher operating tem- peratures and shorter engine life.
The most advanced marine engines today have closed crankcase ventilation systems that prevent contamination of the engine compartment by capturing oil mist and combustion products from the crankcase. While these closed systems require some maintenance to change filters, they eliminate spills and avoid pollution fines, and result in a much cleaner engine compartment.
MECHANICAL SYSTEMS
In every vessel, the force generated by the engines pro- pelling the boat forward must be ultimately borne by the engine mounts — the connection between the engine and the boat’s hull. These engine mounts are either solid or resilient and are under intense strain and vibration. Each type should be inspected annually for deterioration of the rubber, loose fasteners or cracks in the castings or studs and replaced if necessary.
Another mechanical system that needs attention is the torsional coupling. These devices are mounted between the marine transmission and the engine’s flywheel and help dissipate mechanical shock and stress in the form of heat. Some are fluid couplings and some just rely on resilient components. During operation, these devices are subjected to heat, fluids and vibration. Since none of these devices age consistently, it is important to inspect them frequently for wear, cracks or deterioration.
Bill Mossey is Manager of MTU Sales Engineering with
Pacific Power Products Company LLC in Seattle, Wash., a large MTU distributor. Mossey has 34 years of experience in the marine propulsion, diesel engine and diesel power gener- ation industry including field service, application support, training and sales.