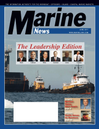
Page 43: of Marine News Magazine (June 2011)
CEO Six-Pack: The Leadership Edition
Read this page in Pdf, Flash or Html5 edition of June 2011 Marine News Magazine
www.marinelink.com MN 43
DIVERSIFIED
Engine Exhaust Systems
HARCO MANUFACTURING CO. 1000 Industrial Pkwy • Newberg OR 97132 800-394-7571 Fax: 503-537-0601 www.harcomanufacturing.com email: [email protected]
ENGINE AND
ENVIRONMENTAL
PRODUCTS
ABS Certified Bureau Veritas Qualified been one of the leading contractors in the Gulf of Mexico as far as cleaning up the messes the hurricanes leave behind. We’ve been doing that for about four years, con- stantly. It’s been a highly successful project for both Veolia and Chevron,” Parker said.
Veolia’s clean-up work includes the preliminary site sur- veys of the subsea area where platforms have been knocked down by a storm, connections of the massive amounts of rigging that are necessary to lift the structures from the sea bottom and the diving support work that goes with actually lifting of the structures and placing them on barges.
Veolia’s 340-ft offshore construction vessel Swordfish was being built when Veolia began talking with Chevron about the project. Veolia made some modifications to the newbuild, including adding a second crane, so that it met
Chevron’s need. “That’s why its been working on that project for Chevron for such a long time,” said Brent
DuBois. “It has a thousand-ft saturation system, two
ROVs, a 150 ton crane, as well as a 70 ton heave com- pensated crane, which makes the vessel rather unique in the marketplace and ideally suited to perform the hurri- cane work.” “Our other flagship project that we’re very pleased with is the Petrobas Cascade Chinook project,” said Parker. “The Petrobras project is in 3,000 meters of water (ultra- deep water) and it involves infrastructure in the Cascade
Chinook field which is unique because it’s the first appli- cation of a floating production storage and offloading unit (FPSO) in the Gulf of Mexico.”
Parker described some of the infrastructure work Veolia has performed on the project. “We’ve installed jumpers on the subsea architecture and we’ve installed flying subsea leads. We’ve done a large amount of subsea survey work for the installation of the different components. We did the pull-in connections for the hybrid risers onto the tur- ret buoy that’s actually connected to the FPSO.”
The 426.5-ft Viking Poseidon, which features the
Ulstein X-Bow design, has been the primary vessel for this project. The benefit of the X-Bow design is better sea keeping capability in dynamic positioning mode and less pitch effect in heavy weather.