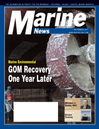
Page 44: of Marine News Magazine (September 2011)
The Environmental Edition
Read this page in Pdf, Flash or Html5 edition of September 2011 Marine News Magazine
44MNSeptember 2011by Chauntelle Baughman, CFPHS; Hydraquip Distribution, Inc. Recycling. Reducing your carbon footprint. Installing fluorescent light bulbs. Everywhere we look, the world is making great strides to ?go green?, and the hydraulic world is keeping up. Over the past several years there have been major efforts made by manufacturers world-wide to pro- mote a greener image, and in doing so reduce the impact on the environment they are working in. Furthermore, regulations are being passed globally requiring those working in or near waterways ? whether they are rivers, ponds or even oceans ? to respect the wildlife who calls that area home. There are two primary standards of biodegradability ? inherently biodegradable and readily biodegradable. All fluids are biodegradable, meaning they break down with- in some undefined span of time. According to the U.S. Army Corps of Engineers, a hydraulic fluid is classified as readily biodegradable when 60% or more of the material is decomposed in 28 days. This is a very important dis- tinction to make when selecting a fluid.While some fluids are biodegradable, that does not nec- essarily indicate that they are also non-toxic. A hydraulic fluid is considered non-toxic if a specific ratio of the hydraulic fluid to water is used and less than 50% of the test organisms die within 96 hours. 1 To meet most new regulations, both the standards for biodegradability and toxicity must be met. BIOFLUID CLASSIFICATIONS There are four major classifications of biofluids, each with their own distinctive characteristics, as shown in Table 1. (Seen on the right) PUTTING YOURFLUIDSTOTHE TESTUltimately, there had to be some test or standard that determines which fluid can hold up to challenge. The RPVOT (ASTM D2272 or Rotating Pressure Vessel Oxidation Test), the Cincinnati Milacron Test (ASTM D2070) or TOST (ASTM D943), do exactly that. These tests are used to monitor oils for losses in oxidation resist- Not all Fluids are Created Equal Why some fluids rise above the rest when put to the test. Table 1 HEPG (Polyglycols):These are commonly referred to as ?water glycols?. As a water-based fluid, they offer poor lubricity and can create major performance issues at high heat because the fluid will begin to boil and form steam bubbles,causing cavitation and rust. These fluids are popular, however, in applications where fire resistance is required. It is important to speak with your hydraulic com- ponent provider when you know you will be using an HEPG fluid, as it may be nec- essary to take into consideration that you may need to de-rate the performance of your hydraulic equipment.HETG (Triglycerides): These are generally plant or animal based oils such as vegetable oil, rapeseed oil, sunflower oil, etc. Unfortunately, many of these flu- ids do not perform well under high heat conditions, as the oil itself will begin to cook and therefore change its chemical composition. They do offer excellent biodegradability and rust prevention, but you must be cautious when using HETG fluids in high-heat applications. HEPR (Polyalphaoelfins):Only a very limited range of PAO base fluids are read- ily biodegradable. These formulating restrictions lead to limited shear stability of the hydraulic fluid, meaning the viscosity is progressively lost as it is run through a system.HEES (Synthetic Esters): These fluids can be broken up into two categories ? saturated esters and unsaturated esters. Unfortunately, all HEES Synthetic bioflu- ids are often grouped together despite their significant performance and longevi- ty differences. Saturation is determined by the chemical bonds within the fluid itself. Unsaturated esters have multiple open bonds which interact with oxygenquickly, leading to oxidation (ageing) of the fluid. This ageing is the cause of extreme thickening and gumming of the fluid, along with deposits and shellac, which lead to major catastrophic system failures. Saturated ester products, how- ever, have significantly fewer open bonds, and therefore they do not oxidize and will last much longer in high-heat, intense applications. The iodine number identi-fies the number of open bonds available, so the higher the Iodine number, the greater the number of bonds that can interact and oxidize. Generally speaking, a saturated ester product has an Iodine number less than 15. (Courtesy Hydraquip Distribution, Inc.) MN#9 (32-49):MN 2011 Layouts 9/6/2011 12:27 PM Page 44